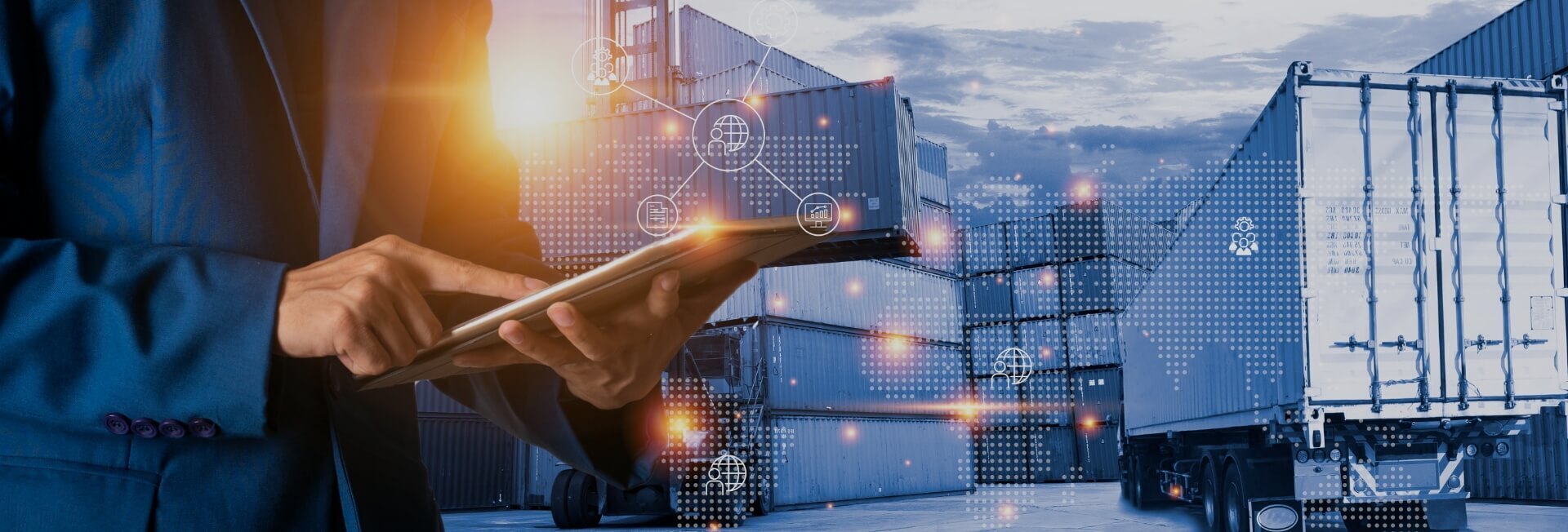
The benefits of implementing a condition-based maintenance schedule
- Home
- Resources
- Fleet Operations and Optimization
- The benefits of implementing a condition-based maintenance schedule
The Benefits of Implementing a Condition-Based Maintenance Schedule
In the world of fleet management and logistics, staying on top of vehicle maintenance is crucial for ensuring smooth operations and minimizing costly breakdowns. Traditional maintenance schedules often rely on fixed intervals or mileage milestones, but these approaches can be inefficient and lead to unnecessary repairs or unexpected failures. To address these challenges, many companies are turning to condition-based maintenance (CBM) schedules, which use real-time data and analytics to optimize fleet maintenance and enhance overall logistics efficiency.
Preventive Maintenance and Fleet Optimization
Preventive maintenance has long been a cornerstone of efficient fleet management. By proactively inspecting and servicing vehicles at regular intervals, companies can identify potential issues before they escalate into major problems. However, traditional preventive maintenance schedules can be based on arbitrary timelines or mileage thresholds, which may not accurately reflect the actual condition of each vehicle.
With a condition-based maintenance schedule, fleet managers have access to real-time data that provides insights into the health and performance of each vehicle. By monitoring factors such as engine temperature, oil pressure, tire wear, and other critical parameters, managers can make informed decisions about when maintenance is truly necessary. This data-driven approach allows for more targeted and efficient maintenance, reducing costs and minimizing downtime.
Streamlined Logistics and Supply Chain Optimization
In addition to improving fleet maintenance efficiency, condition-based maintenance schedules also have a ripple effect on overall logistics operations. By leveraging real-time data and actionable insights, companies can streamline their supply chain and optimize the movement of goods.
For example, with a condition-based maintenance schedule in place, companies can proactively plan for vehicle repairs or maintenance activities. By identifying potential maintenance needs in advance, logistics managers can adjust delivery schedules, allocate resources more effectively, and minimize disruptions to the supply chain. This level of visibility and control allows for more efficient logistics planning and improved customer satisfaction.
Data-Driven Fleet Management and Real-Time Decision-Making
One of the key advantages of implementing a condition-based maintenance schedule is the ability to leverage real-time data for decision-making. By integrating fleet tracking and monitoring technologies, companies can collect and analyze data on a wide range of parameters, from vehicle performance to driver behavior.
This data can then be used to generate actionable insights and drive informed decision-making. For example, if a vehicle's engine temperature exceeds a certain threshold, an alert can be triggered, notifying fleet managers of a potential issue. This allows for proactive maintenance scheduling, reducing the risk of breakdowns and costly repairs.
Furthermore, by analyzing the data collected from multiple vehicles, fleet managers can identify patterns and trends that may indicate systemic issues or areas for improvement. For example, if multiple vehicles in a specific model or age range consistently experience similar problems, it may be a sign of a design flaw or a need for additional training for drivers. By addressing these issues proactively, companies can improve overall fleet performance and minimize maintenance costs.
The Future of Fleet Maintenance
As technology continues to advance, the potential benefits of condition-based maintenance schedules will only grow. Innovations such as Internet of Things (IoT) sensors, predictive analytics, and machine learning algorithms have the potential to revolutionize fleet management and logistics.
Imagine a future where vehicles are equipped with sensors that continuously monitor their performance and condition. These sensors can transmit real-time data to a centralized platform, where sophisticated algorithms can analyze the data and provide actionable recommendations for maintenance and repairs. This level of automation and predictive capabilities would drastically improve fleet maintenance efficiency and optimize logistics operations.
Furthermore, by integrating condition-based maintenance schedules with other technologies such as GPS tracking and telematics, companies can achieve comprehensive fleet management. Real-time data on vehicle location, fuel consumption, and driver behavior can be combined with maintenance data to provide a holistic view of fleet operations. This integrated approach enables companies to make data-driven decisions that optimize both maintenance and logistics, leading to increased efficiency and cost savings.
In Conclusion
Implementing a condition-based maintenance schedule offers numerous benefits for fleet management and logistics efficiency. By leveraging real-time data and analytics, companies can optimize fleet maintenance, streamline logistics operations, and make informed, data-driven decisions. The future of fleet maintenance lies in harnessing the power of technology to automate and optimize maintenance scheduling, enabling companies to achieve comprehensive and efficient fleet management.
Related Blogs
The benefits of implementing a preventive maintenance schedule for facility management
Read More