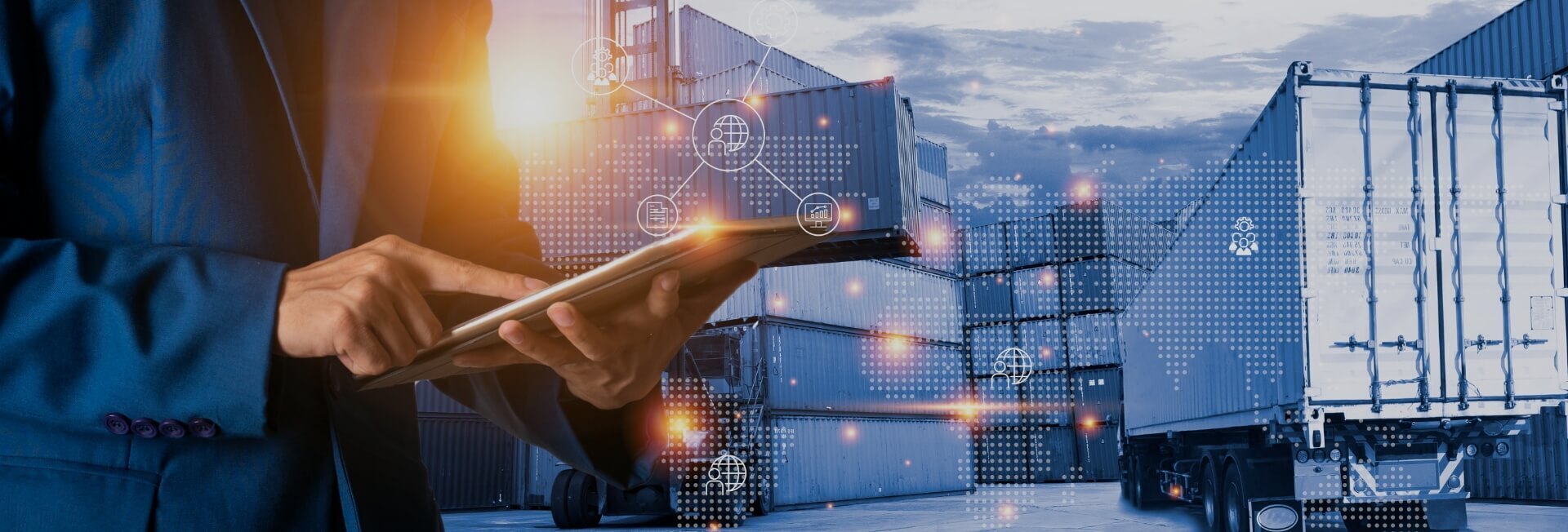
The benefits of condition-based maintenance in automation
- Home
- Resources
- Fleet Operations and Optimization
- The benefits of condition-based maintenance in automation
Improving Efficiency and Reducing Costs with Condition-Based Maintenance in Automation
In today's fast-paced world, businesses are constantly seeking ways to optimize their operations and reduce costs. For companies that rely on automation in their supply chain and fleet management, condition-based maintenance has emerged as a powerful tool to enhance efficiency and drive down maintenance expenses. By leveraging real-time data and proactive maintenance strategies, businesses can keep their operations running smoothly and minimize downtime.
What is Condition-Based Maintenance?
Condition-based maintenance (CBM) is a maintenance strategy that uses real-time data to determine the condition of equipment and assets, and then performs maintenance activities based on that information. Unlike traditional preventive maintenance, which relies on fixed schedules and routine inspections, CBM takes a more data-driven and proactive approach.
By continuously monitoring the performance and health of equipment, businesses can identify potential issues before they cause major disruptions or failures. This allows for more efficient planning and scheduling of maintenance activities, saving both time and money.
The Benefits of Condition-Based Maintenance in Automation
Implementing condition-based maintenance in automation offers several key benefits for businesses:
1. Improved Equipment Reliability and Availability
One of the primary benefits of CBM is improved equipment reliability and availability. By monitoring the condition of equipment in real-time, businesses can detect early signs of deterioration or malfunctions. This enables them to take proactive measures to address the issues before they escalate and cause major breakdowns.
With CBM, businesses can reduce the likelihood of unexpected equipment failures and minimize unplanned downtime. This translates to improved productivity and operational efficiency, as equipment is available when needed and disruptions are minimized.
2. Reduced Maintenance Costs
Traditional preventive maintenance often relies on fixed schedules, which can result in unnecessary maintenance activities and increased costs. On the other hand, condition-based maintenance allows businesses to optimize their maintenance activities based on the actual condition of equipment.
By addressing maintenance needs only when necessary, businesses can reduce the frequency of maintenance tasks and minimize the costs associated with routine inspections and repairs. This leads to significant cost savings in the long run.
3. Increased Operational Efficiency
Condition-based maintenance enables businesses to streamline their operations and improve overall efficiency. By leveraging real-time data and actionable insights, businesses can optimize maintenance scheduling and allocate resources more effectively.
With CBM, businesses can prioritize maintenance activities based on the criticality of equipment and the potential impact of failures. This allows for more efficient planning and execution of maintenance tasks, reducing downtime and maximizing productivity.
4. Extended Equipment Lifespan
By implementing condition-based maintenance, businesses can extend the lifespan of their equipment. Regular monitoring and proactive maintenance help identify and address potential issues before they cause major damage or failures.
By addressing maintenance needs in a timely manner, businesses can prevent minor issues from escalating, which can significantly extend the lifespan of equipment. This not only saves on replacement costs but also reduces the environmental impact of disposing of and manufacturing new equipment.
Implementing Condition-Based Maintenance in Automation
To implement condition-based maintenance in automation, businesses need to follow a few key steps:
1. Data Collection and Monitoring
The first step is to collect and monitor relevant data from the equipment and assets. This can be done through sensors, IoT devices, or other data collection methods. The data collected may include temperature, vibration, pressure, and other relevant parameters.
Businesses should invest in a comprehensive fleet management system that can collect and analyze real-time data from their equipment. This will provide them with the necessary insights to make informed decisions and take proactive maintenance actions.
2. Data Analysis and Predictive Maintenance
Once the data is collected, businesses need to analyze it to identify patterns and trends. This can be done through data analytics tools and predictive maintenance algorithms. By analyzing the data, businesses can predict when equipment is likely to fail and schedule maintenance activities accordingly.
Predictive maintenance allows businesses to address maintenance needs before they cause major disruptions or failures. By taking a proactive approach, businesses can minimize downtime and reduce the impact on their operations.
3. Integration with Fleet Management Systems
Condition-based maintenance should be integrated with a comprehensive fleet management system to ensure seamless monitoring and maintenance operations. This allows businesses to have a centralized view of their equipment and assets, and make data-driven decisions.
By integrating CBM with fleet management systems, businesses can automate maintenance scheduling, track maintenance tasks, and generate reports for analysis. This streamlines the entire maintenance process and improves overall efficiency.
Conclusion
Condition-based maintenance is a powerful tool for businesses looking to improve efficiency and reduce costs in automation. By leveraging real-time data and proactive maintenance strategies, businesses can enhance equipment reliability, reduce maintenance costs, increase operational efficiency, and extend the lifespan of their equipment.
Implementing CBM requires businesses to invest in the right technology and integrate it with their fleet management systems. With the right tools and processes in place, businesses can unlock the full potential of condition-based maintenance and optimize their operations for success.
Related Blogs
The benefits of implementing a preventive maintenance schedule for facility management
Read More