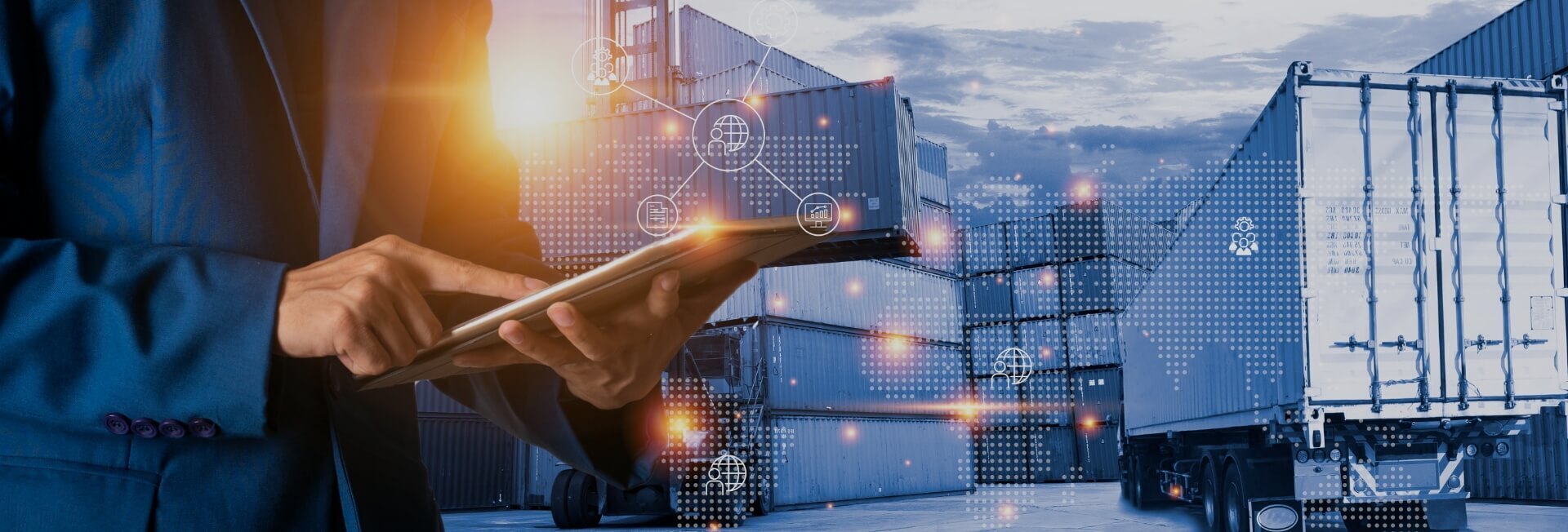
Strategies for reducing vehicle downtime during fleet maintenance
- Home
- Resources
- Fleet Operations and Optimization
- Strategies for reducing vehicle downtime during fleet maintenance
Strategies for Reducing Vehicle Downtime During Fleet Maintenance
Efficient fleet maintenance is crucial for ensuring the smooth operation of logistics and supply chain networks. When vehicles experience downtime due to repairs and maintenance, it can disrupt the entire operation, leading to delays, increased costs, and customer dissatisfaction. To minimize vehicle downtime and optimize fleet maintenance, businesses need to implement strategies that focus on preventive maintenance, fleet tracking, and maintenance scheduling. By leveraging the power of data-driven fleet management and automation, companies can streamline their logistics operations and achieve greater efficiency. In this article, we will explore some effective strategies for reducing vehicle downtime during fleet maintenance.
1. Implement Preventive Maintenance
Preventive maintenance is a proactive approach to fleet maintenance that involves regularly inspecting and servicing vehicles to prevent breakdowns and minimize the risk of unexpected repairs. By implementing a preventive maintenance program, businesses can identify potential issues before they escalate into major problems. This helps in reducing vehicle downtime and avoiding costly repairs.
One of the key aspects of preventive maintenance is adhering to manufacturer-recommended service intervals. This includes oil changes, filter replacements, tire rotations, and other routine maintenance tasks. By following these guidelines, fleet managers can ensure that vehicles are in optimal condition and minimize the risk of breakdowns.
Additionally, businesses can leverage technology solutions such as fleet tracking systems to monitor the health and performance of their vehicles in real-time. These systems provide actionable insights into vehicle diagnostics, fuel efficiency, and maintenance needs. By proactively addressing maintenance issues, businesses can reduce vehicle downtime and improve fleet maintenance efficiency.
2. Utilize Fleet Tracking and Supply Chain Visibility
Fleet tracking systems play a crucial role in reducing vehicle downtime during fleet maintenance. These systems use GPS and telematics technology to track vehicles in real-time, providing businesses with comprehensive visibility into their fleet operations. By utilizing fleet tracking systems, companies can monitor vehicle location, performance, and maintenance needs.
Real-time fleet data enables businesses to make informed decisions regarding vehicle maintenance and repairs. For example, if a vehicle's engine performance starts to deteriorate, the fleet tracking system can alert the maintenance team, allowing them to schedule repairs before the issue worsens. This proactive approach helps in minimizing vehicle downtime and reducing the impact on logistics operations.
Moreover, fleet tracking systems can also provide supply chain visibility by tracking the movement of goods and assets throughout the supply chain. This visibility enables businesses to identify bottlenecks, optimize routes, and streamline logistics operations. By optimizing supply chain visibility and utilizing fleet tracking systems, companies can achieve greater efficiency and reduce vehicle downtime during fleet maintenance.
3. Optimize Maintenance Scheduling
Efficient maintenance scheduling is essential for minimizing vehicle downtime and ensuring timely repairs. By optimizing maintenance scheduling, businesses can allocate resources effectively and reduce the impact on logistics operations.
One strategy for optimizing maintenance scheduling is to prioritize critical repairs and maintenance tasks. By identifying the most critical issues and addressing them first, businesses can minimize the risk of breakdowns and reduce vehicle downtime. This can be achieved by leveraging real-time fleet data and prioritizing maintenance tasks based on their impact on operations.
Another approach to optimizing maintenance scheduling is to leverage predictive analytics and machine learning algorithms. These technologies can analyze historical maintenance data, identify patterns, and predict when a vehicle is likely to require maintenance. By proactively scheduling maintenance based on these predictions, businesses can reduce vehicle downtime and improve fleet maintenance efficiency.
4. Embrace Logistics Automation and Data-Driven Fleet Management
Logistics automation and data-driven fleet management are key strategies for reducing vehicle downtime and improving overall fleet efficiency. By leveraging automation technologies, businesses can streamline their logistics operations and minimize manual intervention.
Automation can be applied to various aspects of fleet maintenance, such as work order generation, parts inventory management, and maintenance task assignment. By automating these processes, businesses can eliminate manual errors, reduce administrative overhead, and ensure timely repairs.
Data-driven fleet management involves leveraging real-time data and analytics to make informed decisions regarding fleet maintenance. By collecting and analyzing data from various sources, such as telematics systems, maintenance records, and driver feedback, businesses can gain actionable insights into their fleet operations. These insights can be used to optimize maintenance schedules, identify potential issues, and improve overall fleet efficiency.
Furthermore, data-driven fleet management enables real-time decision-making, allowing businesses to respond quickly to maintenance issues and minimize vehicle downtime. By embracing logistics automation and data-driven fleet management, companies can achieve comprehensive fleet visibility, streamline their operations, and reduce vehicle downtime during fleet maintenance.
Conclusion
Reducing vehicle downtime during fleet maintenance is essential for optimizing logistics operations and ensuring the smooth flow of goods and services. By implementing strategies such as preventive maintenance, fleet tracking, optimized maintenance scheduling, and embracing logistics automation and data-driven fleet management, businesses can minimize vehicle downtime, improve fleet efficiency, and achieve streamlined logistics operations. By leveraging the power of technology and data, companies can make informed decisions regarding fleet maintenance, reduce the risk of breakdowns, and optimize their supply chain visibility. Ultimately, these strategies enable businesses to deliver reliable and efficient logistics services to their customers.
Related Blogs
The benefits of implementing a preventive maintenance schedule for facility management
Read More