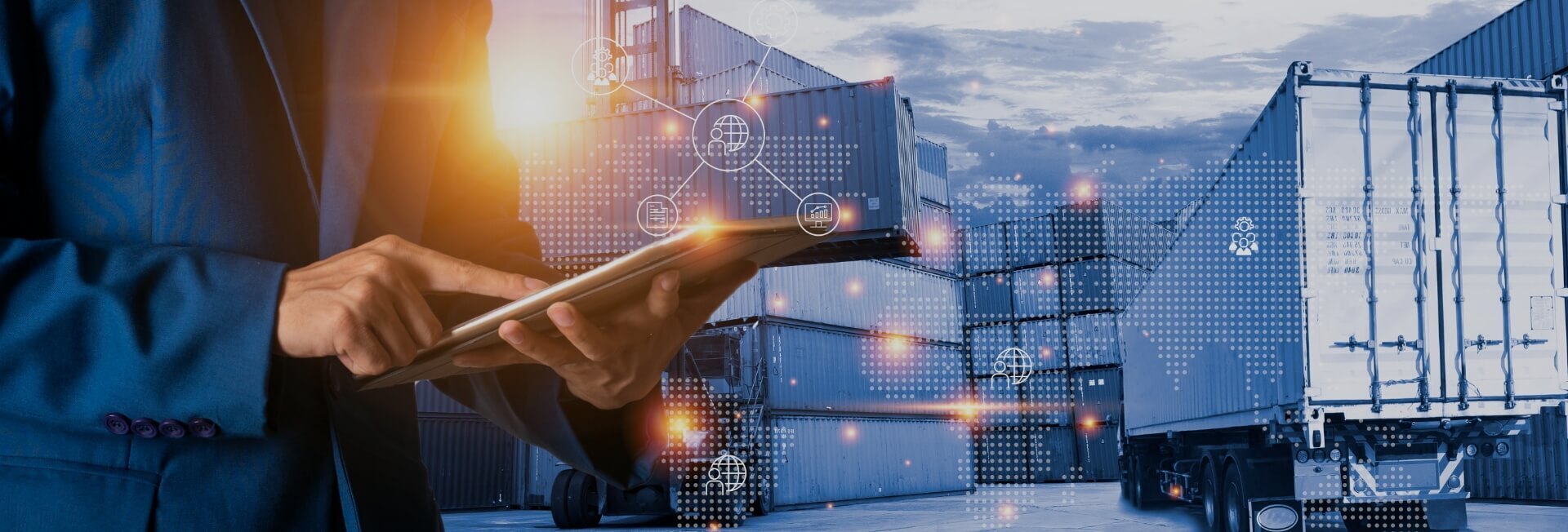
Strategies for reducing order cycle time in logistics operations
- Home
- Resources
- Fleet Operations and Optimization
- Strategies for reducing order cycle time in logistics operations
Introduction
In today's fast-paced business world, efficient logistics operations are crucial for maintaining a competitive edge. One key aspect of logistics operations is order cycle time, which refers to the time it takes to process an order from placement to delivery. A shorter order cycle time can lead to improved customer satisfaction, reduced costs, and increased efficiency. In this article, we will discuss strategies for reducing order cycle time in logistics operations and the benefits it can bring.
1. Streamlined Logistics
Streamlining logistics operations is essential for reducing order cycle time. By eliminating unnecessary steps and optimizing processes, you can ensure that orders are processed quickly and efficiently. This can be achieved through various strategies, such as:
- Implementing automation: Logistics automation can significantly speed up order processing and reduce human error. Automation can be used for tasks such as order placement, inventory management, and shipment tracking. By automating these processes, you can minimize manual intervention and ensure faster order fulfillment.
- Improving supply chain visibility: Having real-time visibility into your supply chain can help identify bottlenecks and delays. By using fleet tracking and supply chain visibility tools, you can proactively address issues and make informed decisions to expedite order processing.
- Optimizing inventory management: Efficient inventory management is essential for reducing order cycle time. By implementing inventory optimization techniques, such as demand forecasting and safety stock calculations, you can ensure that the right products are available when needed, reducing delays caused by stockouts.
2. Maintenance Scheduling and Preventive Maintenance
Efficient fleet maintenance is crucial for minimizing order cycle time. Vehicle breakdowns and delays caused by unexpected repairs can significantly impact order processing. By implementing maintenance scheduling and preventive maintenance strategies, you can reduce the risk of unexpected breakdowns and keep your fleet in optimal condition. Some key strategies include:
- Regular maintenance inspections: Conducting regular inspections of your fleet can help identify potential issues before they cause breakdowns. By proactively addressing maintenance needs, you can prevent unplanned downtime and keep your vehicles on the road.
- Implementing preventive maintenance schedules: Setting up preventive maintenance schedules based on manufacturer recommendations can help ensure that your vehicles receive the necessary maintenance at the right intervals. This can help prevent unexpected breakdowns and extend the lifespan of your fleet.
- Using fleet maintenance software: Fleet maintenance software can streamline maintenance processes by automating tasks such as scheduling, tracking, and reporting. By using such software, you can ensure that maintenance activities are performed on time and efficiently.
3. Data-Driven Fleet Management
Data-driven fleet management plays a crucial role in reducing order cycle time. By leveraging real-time fleet data and actionable insights, you can make informed decisions and optimize your fleet operations. Some key strategies for data-driven fleet management include:
- Utilizing telematics data: Telematics systems can provide real-time data on various aspects of your fleet, such as vehicle location, fuel consumption, and driver behavior. By analyzing this data, you can identify areas for improvement and take proactive measures to optimize fleet performance.
- Implementing predictive analytics: Predictive analytics can help forecast demand, identify potential issues, and optimize routes. By using advanced analytics tools, you can make data-driven decisions that reduce order cycle time and improve overall efficiency.
- Integrating fleet management software: Fleet management software can centralize data and provide comprehensive insights into your fleet operations. By integrating different systems and leveraging automation, you can streamline processes and make real-time, data-driven decisions.
4. Continuous Process Improvement
Continuous process improvement is essential for reducing order cycle time and achieving long-term efficiency gains. By regularly reviewing and optimizing your logistics operations, you can identify areas for improvement and implement changes that streamline processes. Some key strategies for continuous process improvement include:
- Monitoring performance metrics: Tracking key performance indicators (KPIs) such as order processing time, on-time delivery rate, and customer satisfaction can provide insights into the effectiveness of your logistics operations. By monitoring these metrics, you can identify bottlenecks and implement targeted improvements.
- Encouraging employee feedback: Your employees are on the front lines of your logistics operations and can provide valuable insights into potential process improvements. Encourage open communication and regularly seek feedback from your team to identify areas for optimization.
- Implementing Lean principles: Applying Lean principles, such as eliminating waste and optimizing value streams, can help streamline logistics operations. By continuously seeking ways to eliminate non-value-added activities and improve efficiency, you can reduce order cycle time and improve overall performance.
Conclusion
Reducing order cycle time is crucial for achieving efficient logistics operations. By implementing strategies such as streamlined logistics, maintenance scheduling, data-driven fleet management, and continuous process improvement, you can significantly reduce order cycle time and improve overall efficiency. With reduced order cycle time, you can enhance customer satisfaction, reduce costs, and gain a competitive edge in the market.
Related Blogs
The benefits of implementing a preventive maintenance schedule for facility management
Read More