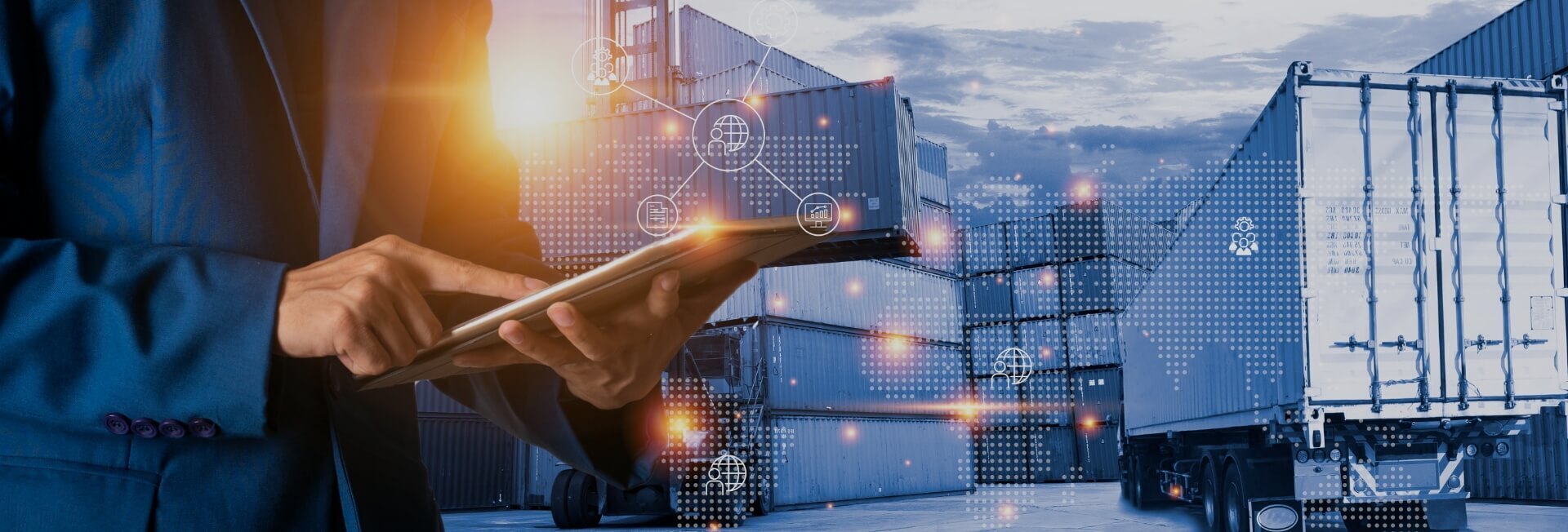
Strategies for optimizing warehouse layout for efficient logistics operations
- Home
- Resources
- Fleet Operations and Optimization
- Strategies for optimizing warehouse layout for efficient logistics operations
Introduction
In today's fast-paced business world, efficient logistics operations are crucial for success. A well-optimized warehouse layout can significantly improve supply chain visibility, streamline logistics processes, and enhance overall efficiency. By implementing effective strategies, businesses can achieve better inventory management, faster order fulfillment, and reduced operating costs. In this article, we will explore some key strategies for optimizing warehouse layout to ensure efficient logistics operations.
1. Analyze Your Current Warehouse Layout
The first step in optimizing your warehouse layout is to analyze your current setup. Start by evaluating the flow of goods within your facility and identifying any bottlenecks or inefficiencies. Look for areas where there is excessive movement or congestion, as these can hinder productivity and lead to delays. Consider using technology such as fleet tracking and supply chain visibility tools to gain actionable insights into your operations.
2. Organize Inventory for Easy Access
Properly organizing your inventory is essential for efficient warehouse operations. Classify your products based on their velocity and popularity, and arrange them accordingly. Place high-demand items closer to the shipping area for quick access and faster order fulfillment. Utilize vertical space by investing in racks and shelving systems that allow for efficient storage and retrieval. Implement a comprehensive inventory management system to track stock levels and facilitate easy replenishment.
3. Optimize Material Handling Equipment Placement
The placement of material handling equipment plays a critical role in warehouse efficiency. Analyze the flow of goods and ensure that equipment such as forklifts, pallet jacks, and conveyors are strategically positioned for maximum productivity. Minimize the distance traveled by these equipment by placing them near high-traffic areas. Regular preventive maintenance and fleet maintenance scheduling are crucial to ensure the smooth operation of your equipment and minimize downtime.
4. Implement Cross-Docking
Cross-docking is a logistics strategy that involves unloading incoming shipments from suppliers and directly loading them onto outbound vehicles for immediate delivery. By eliminating the need for storage, cross-docking reduces handling costs, minimizes inventory holding, and improves order fulfillment speed. To implement cross-docking, you need to have real-time fleet data and comprehensive fleet management capabilities to ensure efficient coordination between suppliers, carriers, and customers.
5. Embrace Automation
Automation is revolutionizing the logistics industry, and warehouses are no exception. Implementing automated systems such as conveyor belts, robotics, and automated storage and retrieval systems (AS/RS) can significantly improve warehouse efficiency. These technologies can handle repetitive and time-consuming tasks, allowing your workforce to focus on more value-added activities. Automation also provides real-time data for decision-making, enabling you to optimize inventory levels and streamline order fulfillment.
6. Optimize Layout for Efficient Order Fulfillment
The layout of your warehouse should be designed to facilitate efficient order fulfillment. Minimize the distance traveled by pickers by organizing products in a logical sequence. Group items that are frequently ordered together to reduce picking time. Implement a warehouse management system (WMS) to optimize picking routes, track order progress, and ensure accurate inventory management. Regularly review your order fulfillment process and make adjustments to enhance efficiency.
7. Create Dedicated Areas for Receiving and Shipping
Separating receiving and shipping areas is crucial for smooth warehouse operations. Designate specific areas for unloading incoming shipments and inspecting goods. This eliminates congestion and reduces the chances of errors during receiving. Similarly, create dedicated spaces for staging outbound shipments, ensuring that orders are accurately packed and loaded onto vehicles. Implement a robust tracking system to monitor the movement of goods throughout the warehouse and provide real-time visibility.
8. Continuous Improvement and Data-Driven Decision-Making
Optimizing warehouse layout is an ongoing process that requires continuous improvement and data-driven decision-making. Regularly review your operations and gather data to identify areas for improvement. Use real-time fleet data, supply chain visibility tools, and analytics to gain actionable insights and make informed decisions. Involve your workforce in the improvement process by encouraging suggestions and feedback. Continuously train and educate your employees to ensure they are equipped with the necessary skills and knowledge.
Conclusion
An optimized warehouse layout is essential for efficient logistics operations. By analyzing your current layout, organizing inventory, optimizing material handling equipment placement, implementing cross-docking, embracing automation, optimizing layout for order fulfillment, creating dedicated areas for receiving and shipping, and continuously improving through data-driven decision-making, you can achieve streamlined logistics and improve overall efficiency. Invest in comprehensive fleet management solutions and utilize real-time fleet data to drive your optimization efforts. By implementing these strategies, you can enhance your supply chain visibility, reduce operating costs, and achieve efficient logistics operations.
Related Blogs
The benefits of implementing a preventive maintenance schedule for facility management
Read More