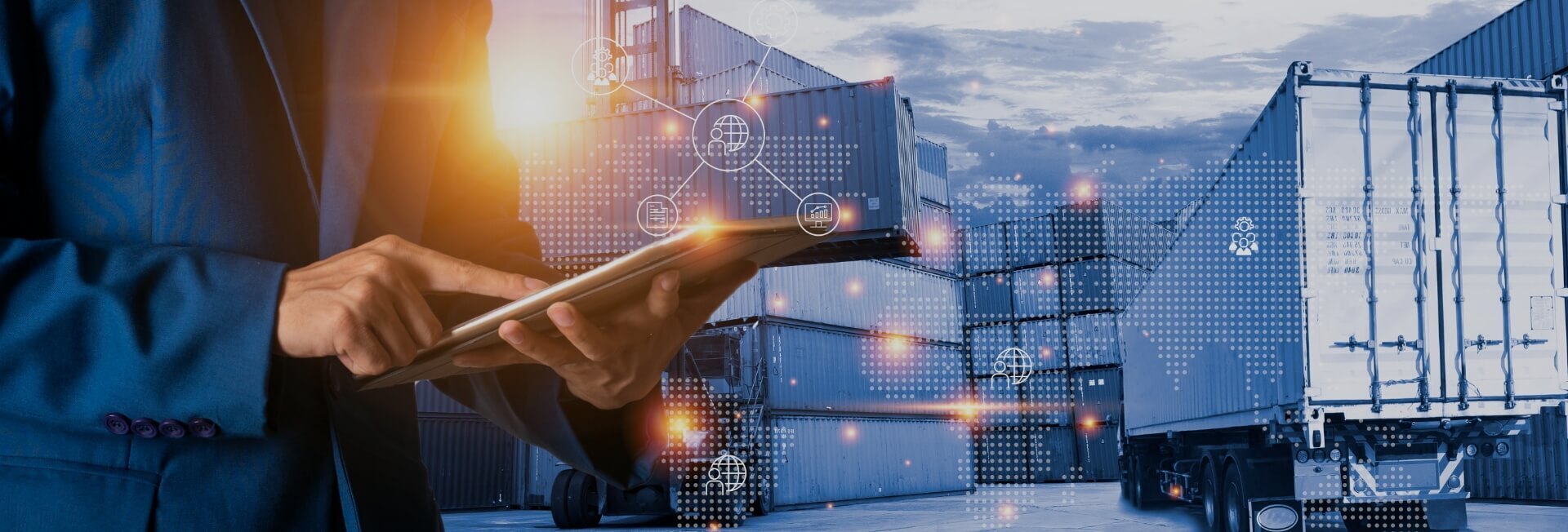
Strategies for optimizing maintenance schedules in a lean manufacturing environment
- Home
- Resources
- Fleet Operations and Optimization
- Strategies for optimizing maintenance schedules in a lean manufacturing environment
Strategies for Optimizing Maintenance Schedules in a Lean Manufacturing Environment
In a lean manufacturing environment, efficiency and productivity are key. One area that can greatly impact efficiency is maintenance scheduling. Proper maintenance of equipment and vehicles is crucial to prevent breakdowns, reduce downtime, and ensure the smooth operation of the supply chain. By optimizing maintenance schedules, companies can improve fleet maintenance, streamline logistics, and achieve cost savings. In this article, we will explore strategies for optimizing maintenance schedules in a lean manufacturing environment.
Preventive Maintenance
Preventive maintenance is a proactive approach to maintenance that involves regularly inspecting and servicing equipment to prevent breakdowns and ensure optimal performance. By implementing a preventive maintenance program, companies can reduce the risk of unexpected equipment failures and the associated costs of repairs and downtime.
One key aspect of preventive maintenance is establishing a regular maintenance schedule. This schedule should be based on manufacturer recommendations, industry best practices, and the specific needs of the equipment or vehicles being maintained. By adhering to a regular maintenance schedule, companies can identify and address potential issues before they become major problems.
Fleet Tracking and Supply Chain Visibility
Fleet tracking and supply chain visibility are essential tools for optimizing maintenance schedules in a lean manufacturing environment. By leveraging technology such as GPS tracking and real-time data analytics, companies can gain insights into the performance and condition of their fleet vehicles.
With fleet tracking, companies can monitor vehicle location, speed, and usage patterns. This information can help identify opportunities for optimizing routes, reducing fuel consumption, and improving overall fleet efficiency. Additionally, real-time data analytics can provide actionable insights into maintenance needs, allowing companies to proactively schedule maintenance based on actual usage and condition.
Streamlined Logistics and Maintenance Scheduling
In a lean manufacturing environment, streamlined logistics are essential for optimizing maintenance schedules. By implementing efficient logistics processes, companies can reduce transit times, minimize inventory holding costs, and improve overall supply chain performance.
One way to streamline logistics is through the use of automation. By automating key processes such as order fulfillment, inventory management, and transportation planning, companies can eliminate manual errors, reduce lead times, and improve overall efficiency. Automation also allows for real-time decision-making, enabling companies to adjust maintenance schedules based on changing demand or operational conditions.
Data-Driven Fleet Management
Data-driven fleet management is another strategy for optimizing maintenance schedules in a lean manufacturing environment. By collecting and analyzing real-time fleet data, companies can make informed decisions about maintenance needs, vehicle repairs, and overall fleet optimization.
Comprehensive fleet management software can provide companies with a centralized platform for tracking and managing fleet performance. By integrating data from various sources such as GPS tracking, vehicle diagnostics, and maintenance records, companies can gain a holistic view of their fleet's condition and performance. This data can then be used to prioritize maintenance tasks, schedule repairs, and optimize maintenance schedules based on actual usage and condition.
Conclusion
Optimizing maintenance schedules in a lean manufacturing environment is crucial for improving fleet maintenance, streamlining logistics, and achieving cost savings. By implementing preventive maintenance programs, leveraging fleet tracking and supply chain visibility tools, streamlining logistics processes, and embracing data-driven fleet management, companies can ensure the smooth operation of their supply chain and minimize downtime.
By taking a proactive approach to maintenance and utilizing technology and data, companies can optimize maintenance schedules and make informed decisions that drive efficiency and productivity. The benefits of optimized maintenance schedules are far-reaching, from reducing the risk of breakdowns and downtime to improving overall fleet performance and customer satisfaction.
In conclusion, optimizing maintenance schedules in a lean manufacturing environment is a continuous process that requires careful planning, regular monitoring, and the use of technology and data. By implementing the strategies discussed in this article, companies can achieve efficient logistics, improve fleet maintenance efficiency, and optimize their supply chain for success.
Related Blogs
The benefits of implementing a preventive maintenance schedule for facility management
Read More