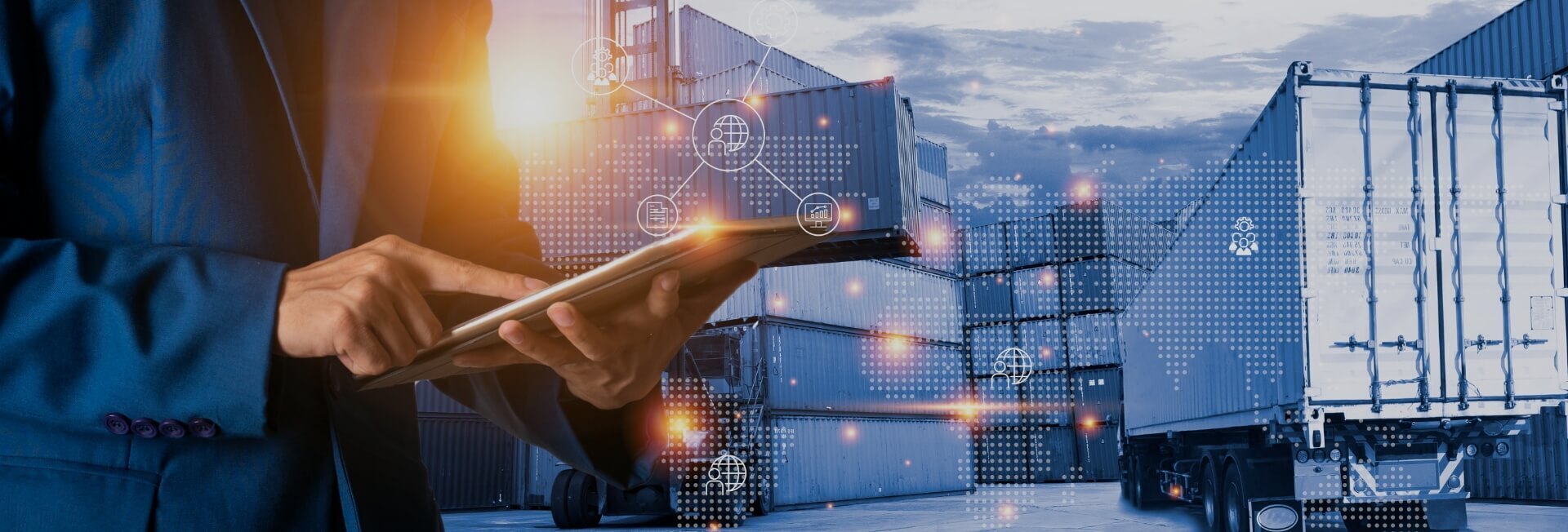
Strategies for managing maintenance schedules in a multi-site organization
- Home
- Resources
- Fleet Operations and Optimization
- Strategies for managing maintenance schedules in a multi-site organization
Strategies for Managing Maintenance Schedules in a Multi-Site Organization
In a multi-site organization, managing maintenance schedules can be a complex task. With multiple locations, vehicles, and equipment to track and maintain, it's essential to have a well-structured and efficient system in place. By implementing the right strategies, organizations can optimize fleet maintenance, streamline logistics, and improve overall efficiency. In this article, we will explore some effective strategies for managing maintenance schedules in a multi-site organization.
1. Implement Preventive Maintenance
Preventive maintenance is a proactive approach to maintenance that involves regular inspections, servicing, and repairs to prevent breakdowns and extend the lifespan of vehicles and equipment. By implementing a preventive maintenance program, organizations can reduce the risk of unexpected breakdowns, minimize downtime, and improve fleet efficiency.
One key aspect of preventive maintenance is establishing a comprehensive maintenance schedule. This schedule should outline the frequency of inspections, servicing, and repairs for each vehicle and equipment in the fleet. It should take into account factors such as mileage, usage, and manufacturer recommendations. By adhering to a well-planned maintenance schedule, organizations can ensure that all necessary maintenance tasks are completed in a timely manner.
2. Utilize Fleet Tracking and Supply Chain Visibility
Fleet tracking and supply chain visibility technologies play a crucial role in managing maintenance schedules in a multi-site organization. By utilizing these technologies, organizations can gain real-time insights into the location, condition, and performance of their vehicles and equipment. This information can be used to optimize maintenance schedules, identify potential issues before they become major problems, and make data-driven decisions.
With fleet tracking technologies, organizations can track the movement of their vehicles and equipment, monitor fuel consumption, and receive alerts for maintenance tasks. This enables them to plan maintenance schedules more effectively, ensuring that vehicles and equipment are serviced at the right time and in the right location.
Supply chain visibility technologies provide organizations with end-to-end visibility into their supply chain, including all the touchpoints involved in the movement of goods. By integrating fleet tracking and supply chain visibility technologies, organizations can gain comprehensive insights into their logistics operations, identify bottlenecks, and optimize maintenance schedules accordingly.
3. Leverage Actionable Insights for Streamlined Logistics
One of the key benefits of utilizing fleet tracking and supply chain visibility technologies is the availability of actionable insights. These insights can be used to streamline logistics operations and improve overall efficiency.
By analyzing data collected from fleet tracking and supply chain visibility technologies, organizations can identify areas of improvement in their logistics processes. For example, they may discover that certain routes are more fuel-efficient or that certain vehicles require more frequent maintenance. With this information, organizations can make informed decisions to optimize logistics operations and maintenance schedules.
4. Automate Maintenance Scheduling and Repairs
Manual maintenance scheduling and repairs can be time-consuming and prone to errors. To improve efficiency and accuracy, organizations should consider automating these processes.
There are various fleet maintenance management software solutions available that can automate maintenance scheduling, generate work orders, and track repairs. These software solutions can integrate with fleet tracking technologies to gather real-time data on vehicle performance, mileage, and usage. This data can then be used to automatically schedule maintenance tasks and repairs based on predefined criteria.
By automating maintenance scheduling and repairs, organizations can reduce administrative workload, minimize human errors, and ensure that all necessary maintenance tasks are completed in a timely manner. This can significantly improve fleet maintenance efficiency and reduce downtime.
Conclusion
Managing maintenance schedules in a multi-site organization is a complex task. However, by implementing the right strategies, organizations can optimize fleet maintenance, streamline logistics, and improve overall efficiency. By implementing preventive maintenance, utilizing fleet tracking and supply chain visibility technologies, leveraging actionable insights, and automating maintenance scheduling and repairs, organizations can ensure that their vehicles and equipment are well-maintained and ready to perform at their best.
Related Blogs
The benefits of implementing a preventive maintenance schedule for facility management
Read More