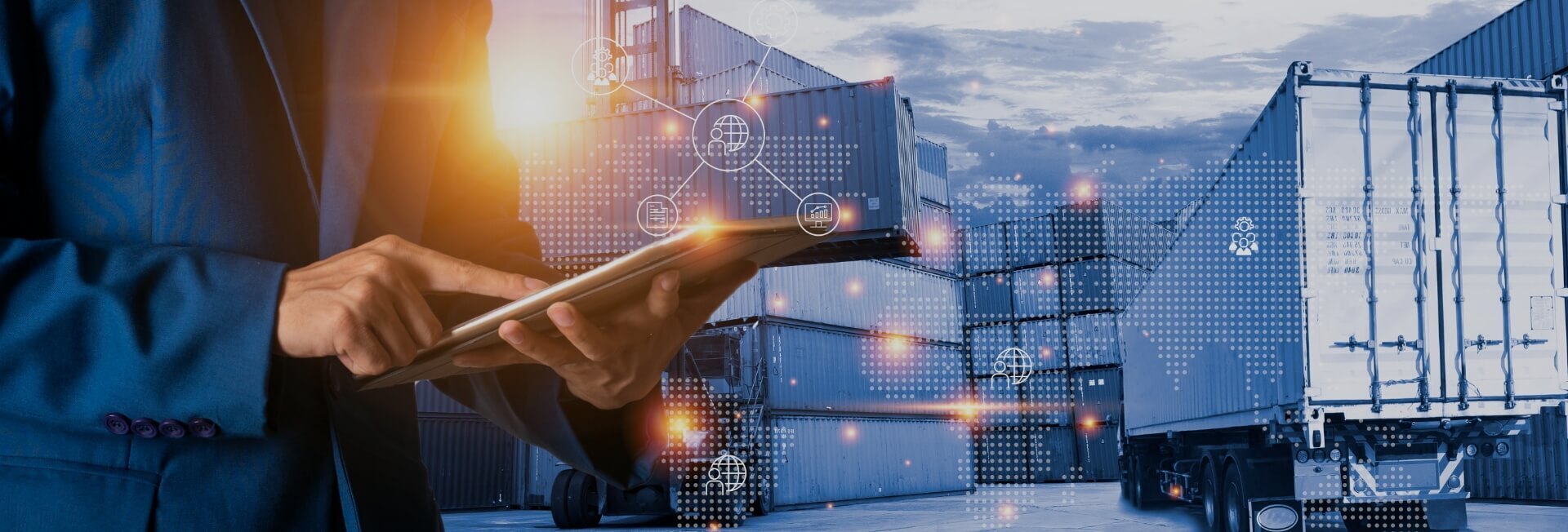
Strategies for managing maintenance schedules in a just-in-time production environment
- Home
- Resources
- Fleet Operations and Optimization
- Strategies for managing maintenance schedules in a just-in-time production environment
Introduction
Just-in-time production is a manufacturing strategy that aims to minimize inventory levels and maximize efficiency. In this approach, materials and components are delivered to the production line exactly when they are needed, reducing waste and costs. While just-in-time production offers numerous benefits, it also presents unique challenges when it comes to managing maintenance schedules. In this article, we will explore strategies for effectively managing maintenance in a just-in-time production environment to ensure smooth operations and prevent disruptions.
Preventive Maintenance
One of the key strategies for managing maintenance schedules in a just-in-time production environment is implementing a preventive maintenance program. Preventive maintenance involves conducting regular inspections, servicing, and repairs to prevent breakdowns and extend the lifespan of equipment. By regularly maintaining equipment, you can identify and address issues before they become major problems that could disrupt production.
Preventive maintenance can be scheduled based on usage, time, or a combination of both. For example, you can schedule maintenance tasks based on the number of hours a machine has been in operation or the number of units produced. By tracking maintenance activities and collecting data on equipment performance, you can identify trends and make data-driven decisions to optimize maintenance schedules and prevent unplanned downtime.
Fleet Maintenance
In a just-in-time production environment, it is crucial to have a well-maintained fleet of vehicles to ensure timely delivery of materials and components. Fleet maintenance involves regular inspections, repairs, and servicing of vehicles to keep them in optimal condition. By implementing a comprehensive fleet maintenance program, you can minimize the risk of breakdowns and delays in the supply chain.
One approach to fleet maintenance is to leverage fleet tracking technology. By equipping vehicles with GPS tracking devices, you can monitor their location, performance, and maintenance needs in real-time. This allows you to proactively schedule maintenance tasks based on actual usage and mileage, rather than relying on fixed schedules. With real-time fleet data and supply chain visibility, you can make data-driven decisions to optimize maintenance schedules and ensure efficient logistics operations.
Logistics Automation
Automation plays a crucial role in managing maintenance schedules in a just-in-time production environment. Through the use of advanced technologies and software, you can streamline logistics operations and optimize maintenance tasks. Logistics automation enables real-time monitoring of equipment and vehicles, allowing you to detect potential issues and schedule maintenance activities accordingly.
With automated systems, you can track the performance and maintenance needs of equipment and vehicles, generate maintenance schedules, and assign tasks to technicians. This eliminates the need for manual tracking and scheduling, reducing the risk of human error and ensuring that maintenance is carried out in a timely manner. By leveraging automation, you can achieve greater efficiency and accuracy in managing maintenance schedules, leading to improved fleet maintenance efficiency and overall logistics optimization.
Actionable Insights for Maintenance Scheduling
To effectively manage maintenance schedules in a just-in-time production environment, it is essential to leverage actionable insights derived from data analysis. By collecting and analyzing data on equipment performance, maintenance history, and production schedules, you can identify patterns and trends that can inform maintenance scheduling decisions.
For example, by analyzing historical maintenance data, you may discover that certain equipment requires more frequent maintenance during specific production periods. Armed with this knowledge, you can adjust maintenance schedules to allocate more resources and time for preventive maintenance during these periods to prevent production disruptions. By using data-driven insights, you can optimize maintenance schedules and allocate resources more effectively, leading to improved fleet maintenance efficiency and reduced downtime.
Conclusion
In a just-in-time production environment, managing maintenance schedules is crucial to ensure smooth operations and prevent disruptions in the supply chain. By implementing preventive maintenance programs, leveraging fleet maintenance strategies, embracing logistics automation, and utilizing actionable insights, you can optimize maintenance schedules and improve fleet maintenance efficiency. With comprehensive fleet management and real-time decision-making, you can achieve streamlined logistics, minimize downtime, and maximize the benefits of just-in-time production.
Related Blogs
The benefits of implementing a preventive maintenance schedule for facility management
Read More