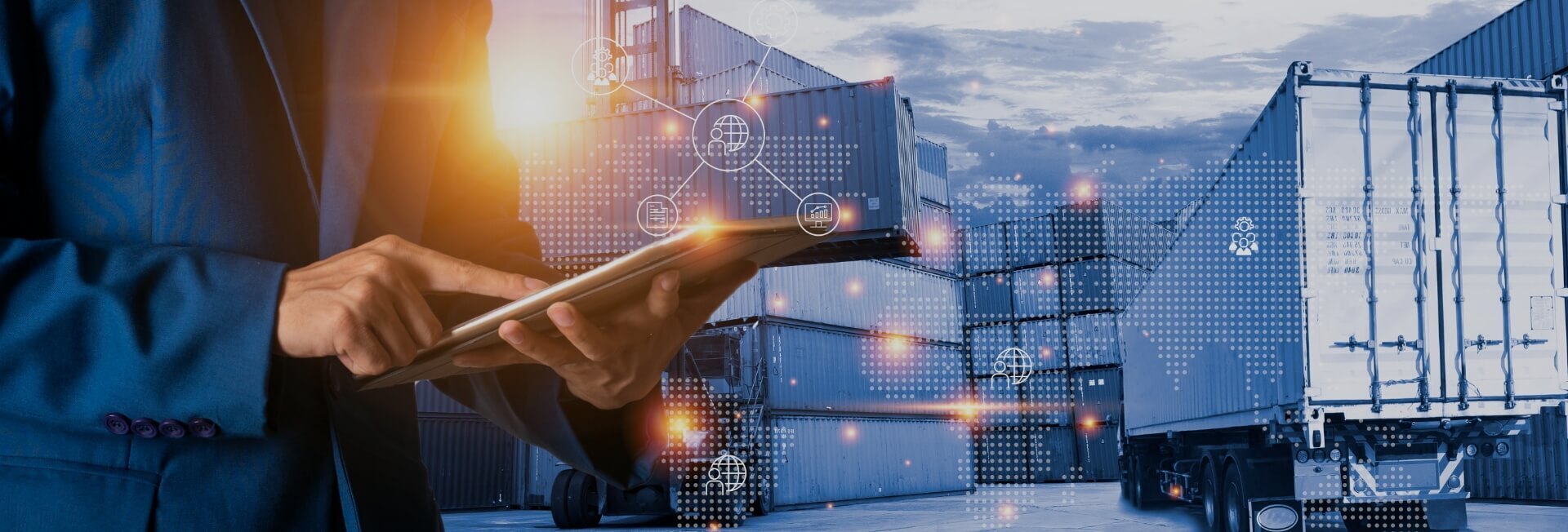
How preventive maintenance can reduce downtime in manufacturing facilities
- Home
- Resources
- Fleet Operations and Optimization
- How preventive maintenance can reduce downtime in manufacturing facilities
The Importance of Preventive Maintenance
Preventive maintenance is a crucial aspect of any manufacturing facility. By regularly inspecting and servicing equipment, companies can prevent unexpected breakdowns, reduce downtime, and optimize their operations. In this article, we will explore how preventive maintenance can effectively minimize downtime in manufacturing facilities and improve overall efficiency.
Reducing Unplanned Downtime
Unplanned downtime can be a major disruption to manufacturing operations. It leads to loss of productivity, missed deadlines, and increased costs. Implementing a preventive maintenance program helps identify potential issues before they become major problems. By regularly inspecting equipment and identifying any signs of wear and tear, companies can schedule maintenance activities to avoid breakdowns and minimize unplanned downtime.
One of the key benefits of preventive maintenance is the ability to address minor issues before they escalate. For example, a small oil leak in a machine can be easily fixed during a scheduled maintenance activity. However, if left unattended, the leak can worsen and lead to a complete breakdown of the machine, resulting in significant downtime. By addressing such issues proactively, companies can save time, money, and resources.
Increasing Equipment Reliability
Regular maintenance activities, such as cleaning, lubricating, and calibrating equipment, can significantly increase its reliability. When machines are properly maintained, they are less likely to experience unexpected failures. This not only reduces downtime but also improves the overall efficiency and productivity of the manufacturing facility.
By implementing a preventive maintenance program, companies can keep their equipment in optimal condition, ensuring that it operates at peak performance. This, in turn, leads to improved product quality, reduced waste, and increased customer satisfaction. Preventive maintenance is essential for companies looking to maintain a competitive edge in the manufacturing industry.
Enhancing Safety in the Workplace
Another important aspect of preventive maintenance is its role in enhancing safety in the workplace. Regular inspections and maintenance activities help identify and address any safety hazards present in the manufacturing facility. This includes issues such as faulty wiring, leaking pipes, or loose fittings.
By proactively addressing safety hazards, companies can ensure a safe working environment for their employees. This not only reduces the risk of accidents and injuries but also improves employee morale and productivity. Preventive maintenance plays a crucial role in creating a culture of safety within the manufacturing facility.
Improving Overall Equipment Efficiency
Preventive maintenance is not just about avoiding breakdowns and reducing downtime. It also plays a key role in improving overall equipment efficiency. Regular inspections and maintenance activities help identify any inefficiencies in the equipment or processes.
For example, a preventive maintenance program may identify a machine that is consuming excessive energy due to a malfunctioning component. By addressing this issue promptly, companies can significantly reduce their energy consumption and related costs. This not only improves the bottom line but also contributes to a more sustainable and environmentally friendly manufacturing facility.
Implementing a Preventive Maintenance Program
Implementing a preventive maintenance program requires careful planning and execution. Here are some key steps to consider:
1. Equipment Inventory and Documentation
The first step in implementing a preventive maintenance program is to create an inventory of all equipment present in the manufacturing facility. This includes machinery, tools, vehicles, and other assets. Each item should be documented with relevant information such as make, model, serial number, and maintenance history.
2. Maintenance Scheduling
Once the equipment inventory is complete, companies can develop a maintenance schedule based on manufacturer recommendations, industry best practices, and their own specific needs. This schedule should include regular inspections, cleaning, lubrication, calibration, and any other necessary maintenance activities.
3. Staff Training and Resources
To ensure the success of a preventive maintenance program, companies need to invest in staff training and provide the necessary resources. This includes training technicians on equipment maintenance procedures, providing them with the right tools and equipment, and establishing a system for tracking and documenting maintenance activities.
4. Data-Driven Decision-Making
Implementing a preventive maintenance program also requires the use of data-driven decision-making. By collecting and analyzing data on equipment performance, maintenance activities, and downtime, companies can identify patterns and trends. This allows them to make informed decisions regarding equipment replacement, process improvements, and resource allocation.
The Role of Technology in Preventive Maintenance
Technology plays a crucial role in enabling effective preventive maintenance in manufacturing facilities. Here are some key technologies that can be utilized:
1. Fleet Tracking and Management
Fleet tracking and management software allows companies to monitor the performance and maintenance needs of their vehicles in real-time. This helps optimize routes, schedule maintenance activities, and ensure efficient fleet operations. By leveraging fleet tracking technology, companies can reduce breakdowns, improve fuel efficiency, and minimize downtime.
2. Predictive Maintenance Solutions
Predictive maintenance solutions use advanced analytics and machine learning algorithms to predict equipment failures before they occur. By analyzing data from sensors and other sources, these solutions can identify early signs of equipment deterioration and recommend timely maintenance actions. This helps companies avoid unplanned downtime and optimize their maintenance schedules.
3. IoT and Sensor Technology
The Internet of Things (IoT) and sensor technology enable real-time monitoring of equipment performance and condition. Sensors can be installed on machines to collect data on parameters such as temperature, vibration, and energy consumption. This data can then be analyzed to detect anomalies and trigger maintenance alerts. By leveraging IoT and sensor technology, companies can proactively address equipment issues and prevent breakdowns.
Conclusion
Preventive maintenance is a critical aspect of managing manufacturing facilities. By implementing a comprehensive preventive maintenance program, companies can reduce unplanned downtime, increase equipment reliability, enhance workplace safety, improve overall efficiency, and achieve significant cost savings. Leveraging technology, such as fleet tracking, predictive maintenance solutions, and IoT, further enhances the effectiveness of preventive maintenance efforts. In today's competitive manufacturing landscape, implementing preventive maintenance is not just a choice, but a necessity for success.
Related Blogs
The benefits of implementing a preventive maintenance schedule for facility management
Read More