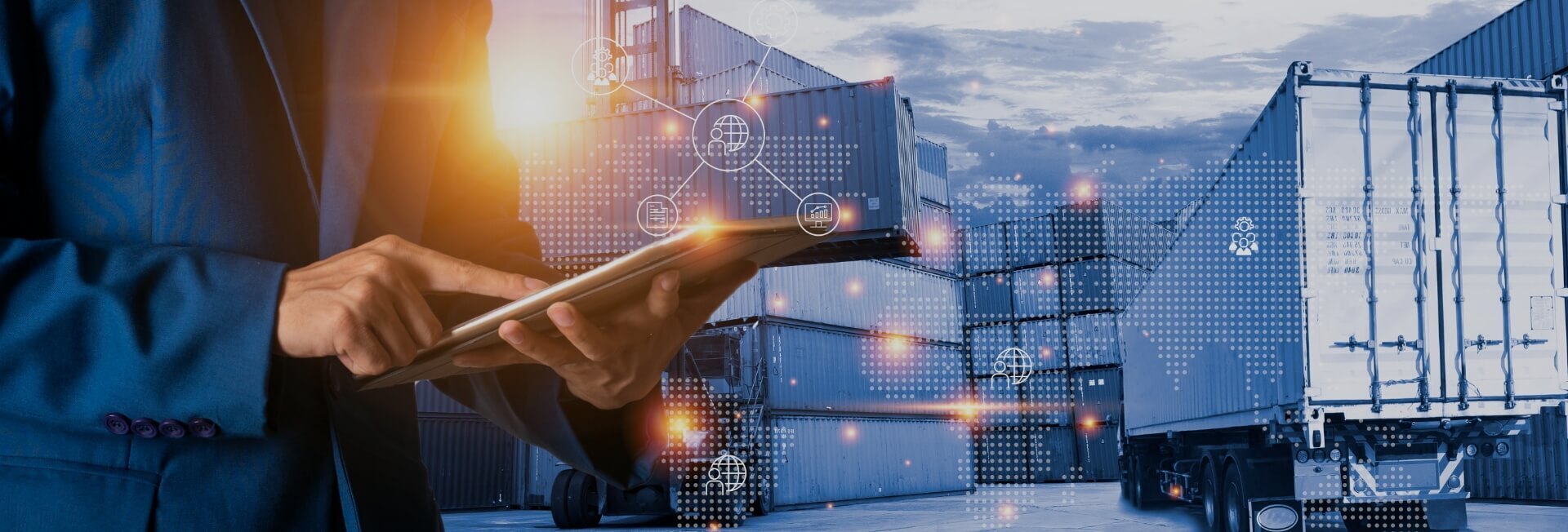
How maintenance automation is revolutionizing the manufacturing industry
- Home
- Resources
- Fleet Operations and Optimization
- How maintenance automation is revolutionizing the manufacturing industry
Introduction
The manufacturing industry has always been driven by efficiency and productivity. Over the years, advancements in technology have played a crucial role in optimizing processes and improving overall performance. One area where automation has made a significant impact is maintenance. By leveraging the power of data and technology, maintenance automation has revolutionized the way manufacturers manage their assets and ensure smooth operations.
The Importance of Maintenance in Manufacturing
Maintenance is a critical aspect of the manufacturing industry. It involves a series of activities aimed at ensuring that machinery, equipment, and other assets are in optimal condition to perform their intended functions. Effective maintenance practices help minimize downtime, reduce the risk of breakdowns, and extend the lifespan of assets. Preventive maintenance, in particular, focuses on identifying and addressing potential issues before they develop into major problems, saving both time and money in the long run.
The Challenges of Traditional Maintenance Approaches
Traditional maintenance approaches in the manufacturing industry often relied on manual processes and reactive strategies. This meant waiting for equipment to fail before taking action, resulting in unplanned downtime, costly repairs, and reduced productivity. Additionally, manual record-keeping made it difficult to track maintenance activities, leading to inefficient scheduling and missed inspections.
The Rise of Maintenance Automation
With the advent of advanced technologies, maintenance automation has emerged as a game-changer for the manufacturing industry. By leveraging data, analytics, and connectivity, manufacturers can now implement proactive maintenance strategies that optimize asset performance and minimize disruptions. Let's explore some of the key ways maintenance automation is revolutionizing the manufacturing industry:
1. Preventive Maintenance
Preventive maintenance is a cornerstone of maintenance automation. By using real-time data from sensors and IoT devices, manufacturers can monitor the health of their assets and detect any signs of potential failures. This proactive approach allows for timely maintenance interventions, preventing costly breakdowns and minimizing downtime. Preventive maintenance also helps optimize asset performance and extend their lifespan, resulting in significant cost savings in the long term.
2. Streamlined Maintenance Scheduling
Maintenance automation enables manufacturers to streamline their maintenance scheduling processes. With access to real-time data on asset conditions and performance, manufacturers can prioritize maintenance tasks based on urgency and criticality. This ensures that resources are allocated efficiently and that maintenance activities are carried out at optimal times, minimizing disruptions to production schedules.
3. Data-Driven Decision Making
Maintenance automation provides manufacturers with actionable insights derived from data analysis. By collecting and analyzing data on asset performance, maintenance activities, and historical trends, manufacturers can make informed decisions regarding maintenance strategies and resource allocation. This data-driven approach helps optimize maintenance processes, improve asset reliability, and reduce overall maintenance costs.
4. Improved Supply Chain Visibility and Optimization
Maintenance automation not only benefits the manufacturing process but also extends to the broader supply chain. By integrating maintenance data with supply chain systems, manufacturers can gain real-time visibility into the status and condition of their assets throughout the logistics process. This visibility allows for better planning, coordination, and optimization of supply chain activities, resulting in improved efficiency and reduced costs.
The Future of Maintenance Automation
As technology continues to evolve, maintenance automation in the manufacturing industry is expected to become even more sophisticated. Here are some trends and developments that can be expected in the future:
1. Predictive Maintenance
Predictive maintenance takes maintenance automation to the next level by leveraging advanced analytics and machine learning algorithms to predict asset failures with a high degree of accuracy. By analyzing historical data and real-time sensor data, manufacturers can identify patterns and anomalies that indicate potential failures. This allows for proactive interventions and further optimization of maintenance processes.
2. Robotics and Automation
The integration of robotics and automation technologies with maintenance processes can greatly enhance efficiency and productivity. Autonomous robots can perform routine maintenance tasks, such as inspections and simple repairs, without human intervention. This not only reduces the reliance on manual labor but also improves the accuracy and speed of maintenance activities.
3. Augmented Reality (AR) and Virtual Reality (VR)
AR and VR technologies have the potential to revolutionize maintenance training and troubleshooting. By overlaying digital information onto the physical world, technicians can access step-by-step instructions, visualizations, and real-time data while performing maintenance tasks. This improves efficiency, reduces errors, and enhances the overall effectiveness of maintenance activities.
Conclusion
Maintenance automation is transforming the manufacturing industry by optimizing asset performance, reducing downtime, and improving overall productivity. By leveraging data, analytics, and advanced technologies, manufacturers can implement proactive maintenance strategies that minimize disruptions and maximize efficiency. As the industry continues to embrace automation, we can expect further advancements that will revolutionize maintenance practices and drive the manufacturing industry towards a more efficient and sustainable future.
Related Blogs
The benefits of implementing a preventive maintenance schedule for facility management
Read More