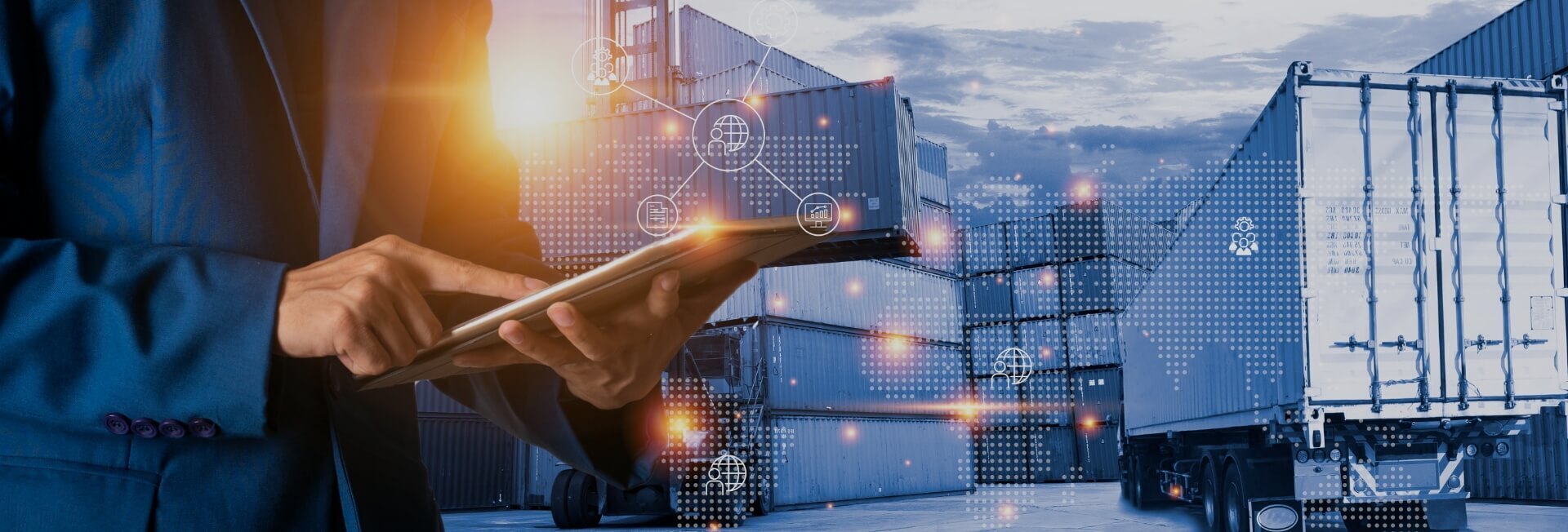
Challenges in scheduling maintenance for equipment with limited maintenance history
- Home
- Resources
- Fleet Operations and Optimization
- Challenges in scheduling maintenance for equipment with limited maintenance history
Overcoming Challenges in Scheduling Maintenance for Equipment with Limited Maintenance History
Effective maintenance scheduling is crucial for the smooth operation of any equipment or machinery. Regular maintenance ensures that the equipment is in optimal condition, minimizing the risk of breakdowns and costly repairs. However, scheduling maintenance becomes challenging when dealing with equipment that has limited maintenance history. In such cases, it can be difficult to determine the appropriate maintenance intervals and identify potential issues before they become major problems.
The Importance of Preventive Maintenance
Preventive maintenance is a proactive approach to equipment maintenance that aims to prevent breakdowns and extend the lifespan of the equipment. It involves performing regular inspections, lubrication, and repairs to identify and address potential issues before they escalate. Preventive maintenance is essential for maintaining the reliability, efficiency, and safety of equipment.
However, to effectively implement preventive maintenance, it is crucial to have a comprehensive maintenance schedule based on the equipment's maintenance history. With limited maintenance history, it becomes challenging to establish a reliable maintenance schedule and ensure that the equipment receives the necessary maintenance at the right intervals.
Challenges in Scheduling Maintenance with Limited Maintenance History
1. Lack of Data:
When equipment has limited maintenance history, there is a lack of data to analyze and identify patterns or trends. This makes it difficult to determine the appropriate maintenance intervals and the type of maintenance required. Without sufficient data, maintenance scheduling becomes a guessing game, which can lead to either unnecessary maintenance or missed maintenance opportunities.
2. Increased Risk of Breakdowns:
Without a reliable maintenance schedule, the risk of unexpected breakdowns and equipment failures increases. This can disrupt operations, lead to costly repairs, and result in downtime. Without historical maintenance data, it is challenging to predict and prevent potential issues before they escalate, increasing the likelihood of equipment failure.
3. Inefficient Resource Allocation:
Limited maintenance history makes it difficult to allocate resources effectively. Without data on the equipment's maintenance needs, it is challenging to determine the appropriate staffing levels, spare parts inventory, and maintenance budget. This can lead to either overstaffing and overspending or understaffing and insufficient resources, both of which can impact the efficiency and effectiveness of maintenance operations.
4. Inaccurate Performance Metrics:
Performance metrics play a crucial role in assessing the effectiveness of maintenance operations and identifying areas for improvement. However, with limited maintenance history, it becomes challenging to establish accurate performance metrics. Without baseline data, it is difficult to measure the impact of maintenance activities, track improvements, and identify areas that require attention.
Overcoming the Challenges
While scheduling maintenance for equipment with limited maintenance history can be challenging, there are strategies and solutions that can help overcome these challenges:
1. Implement Condition-Based Maintenance:
Condition-based maintenance (CBM) is a maintenance strategy that focuses on the actual condition of the equipment rather than predetermined maintenance intervals. CBM utilizes real-time data from sensors and monitoring systems to assess the equipment's health and trigger maintenance actions when necessary. By implementing CBM, organizations can overcome the challenges posed by limited maintenance history by basing maintenance decisions on the current condition of the equipment.
2. Utilize Predictive Analytics:
Predictive analytics uses historical data, statistical algorithms, and machine learning techniques to predict future events or behaviors. By analyzing historical maintenance data and equipment performance, organizations can identify patterns and trends that can help predict maintenance needs even with limited maintenance history. Predictive analytics can assist in determining the optimal maintenance intervals and identifying potential issues before they become critical problems.
3. Leverage Data from Similar Equipment:
If the equipment in question has limited maintenance history, organizations can leverage data from similar equipment or machinery within their fleet or industry. By analyzing the maintenance history of similar equipment, organizations can gain insights into the maintenance needs, intervals, and potential issues that may arise. This can provide a starting point for developing a maintenance schedule for the equipment with limited maintenance history.
4. Consult Industry Experts:
When dealing with equipment with limited maintenance history, it can be beneficial to consult industry experts or equipment manufacturers. They may have valuable insights and recommendations based on their experience and knowledge of similar equipment. Industry experts can provide guidance on maintenance intervals, potential issues to look out for, and best practices for maintaining equipment with limited maintenance history.
Conclusion
Scheduling maintenance for equipment with limited maintenance history presents unique challenges. However, by implementing strategies such as condition-based maintenance, utilizing predictive analytics, leveraging data from similar equipment, and consulting industry experts, organizations can overcome these challenges and establish effective maintenance schedules. With proactive and data-driven maintenance scheduling, organizations can ensure the reliability, efficiency, and longevity of their equipment, ultimately minimizing downtime and maximizing productivity.
Related Blogs
The benefits of implementing a preventive maintenance schedule for facility management
Read More