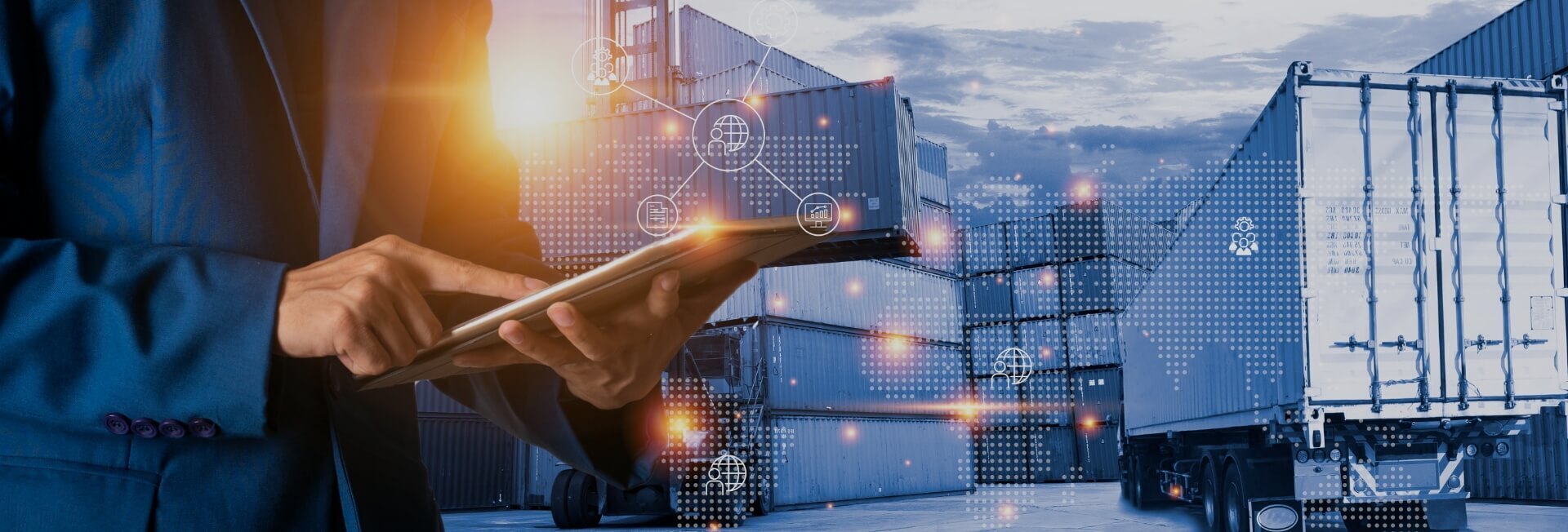
Challenges in scheduling maintenance for equipment with limited availability
- Home
- Resources
- Fleet Operations and Optimization
- Challenges in scheduling maintenance for equipment with limited availability
Introduction
Scheduling maintenance for equipment with limited availability presents a unique set of challenges for businesses in various industries. Whether it's heavy machinery used in construction, specialized tools required for manufacturing, or vehicles used for transportation, ensuring that these critical assets are properly maintained is essential for their longevity and optimal performance.
However, scheduling maintenance for equipment with limited availability can be a complex task. Factors such as equipment utilization, operational demands, and limited downtime windows can make it difficult to find the right time to conduct maintenance activities. In this article, we will explore some of the challenges faced in scheduling maintenance for equipment with limited availability and discuss strategies to overcome them.
Challenges in Scheduling Maintenance
1. Limited Downtime Windows:
One of the primary challenges in scheduling maintenance for equipment with limited availability is the limited downtime windows. In industries where equipment is constantly in use, finding a time when the equipment can be taken out of service for maintenance becomes a logistical puzzle. Any unplanned downtime can disrupt operations, leading to delays, decreased productivity, and potential financial losses.
2. Operational Demands:
Another challenge is the operational demands placed on the equipment. Businesses rely on these assets to meet their production targets or service commitments. Taking the equipment out of service for maintenance can impact the overall productivity and operational efficiency. Balancing the need for maintenance with the need for uninterrupted operations is a delicate task.
3. Limited Availability of Spare Parts:
Maintenance activities often require the replacement of worn-out parts or components. However, the limited availability of spare parts can pose a challenge. Some equipment may have unique or specialized parts that are not readily available in the market. This can result in delays in conducting scheduled maintenance or even lead to extended downtime if a critical part is not available.
4. Cost Considerations:
Scheduling maintenance for equipment with limited availability also involves cost considerations. Conducting maintenance activities can be expensive, especially if it requires specialized skills or equipment. Businesses need to balance the cost of maintenance with the potential risks of equipment failure or breakdown. This requires careful financial planning and budget allocation.
Strategies to Overcome Challenges
1. Implement Preventive Maintenance:
Preventive maintenance involves regularly scheduled maintenance activities to prevent equipment failure or breakdown. By implementing a preventive maintenance program, businesses can reduce the likelihood of unscheduled downtime and costly repairs. Regular inspections, lubrication, and replacement of worn-out parts can help extend the lifespan of the equipment and improve its overall performance.
2. Utilize Fleet Tracking and Management Systems:
In industries that rely heavily on vehicles, such as logistics and transportation, fleet tracking and management systems can be invaluable in scheduling maintenance for equipment with limited availability. These systems provide real-time data on the location, condition, and performance of the vehicles, allowing businesses to identify the best time for maintenance based on factors such as vehicle utilization, mileage, and engine hours.
3. Leverage Supply Chain Visibility and Optimization:
Supply chain visibility and optimization solutions can help businesses streamline their logistics operations and improve maintenance scheduling for equipment with limited availability. By gaining real-time insights into their supply chain, businesses can identify potential bottlenecks or inefficiencies that may affect the availability of equipment for maintenance. This allows them to proactively address any issues and optimize their supply chain to ensure timely maintenance.
4. Embrace Maintenance Automation:
Maintenance automation can significantly improve the scheduling of maintenance for equipment with limited availability. Automated systems can track the usage and performance of the equipment, predict maintenance needs, and generate work orders automatically. This eliminates the need for manual tracking and scheduling, saving time and reducing the risk of human error.
Conclusion
Scheduling maintenance for equipment with limited availability is a challenging task that requires careful planning and coordination. By implementing preventive maintenance practices, utilizing fleet tracking and management systems, leveraging supply chain visibility and optimization solutions, and embracing maintenance automation, businesses can overcome these challenges and ensure that their critical assets are properly maintained. This not only extends the lifespan of the equipment but also improves operational efficiency and reduces the risk of costly breakdowns or failures.
Related Blogs
The benefits of implementing a preventive maintenance schedule for facility management
Read More