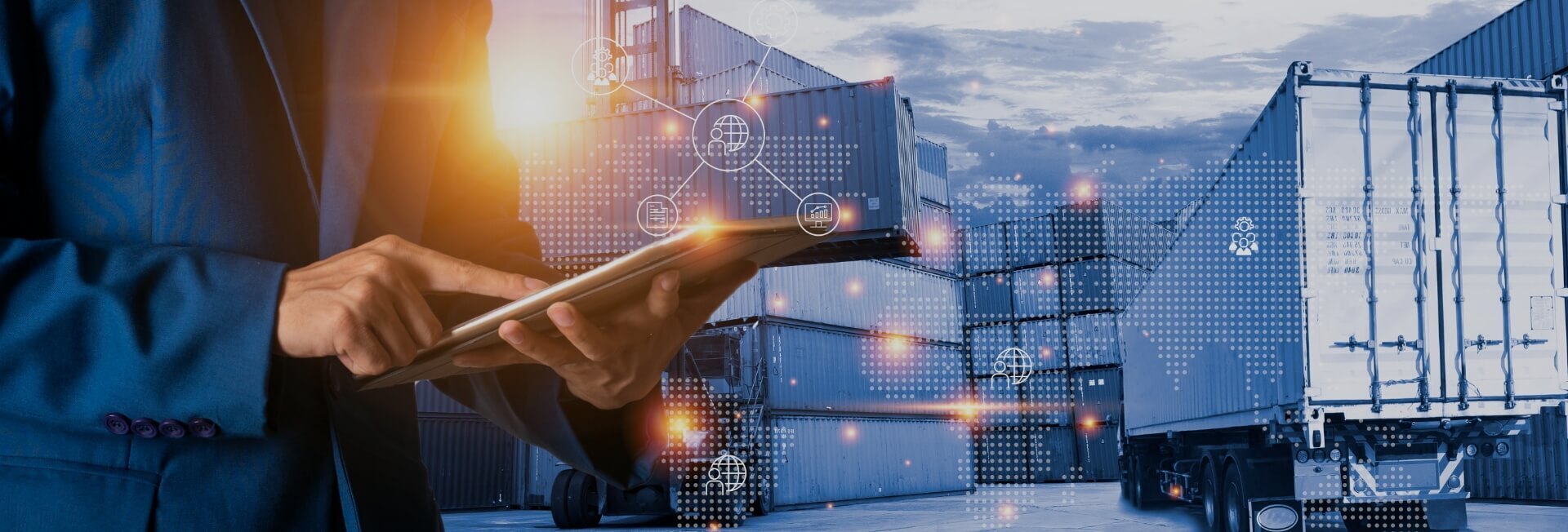
Challenges in scheduling maintenance for equipment with limited accessibility
- Home
- Resources
- Fleet Operations and Optimization
- Challenges in scheduling maintenance for equipment with limited accessibility
Introduction
When it comes to ensuring the smooth operation of equipment, scheduled maintenance plays a crucial role. Regular maintenance not only extends the lifespan of machinery but also helps prevent costly breakdowns and repairs. However, scheduling maintenance for equipment with limited accessibility can present unique challenges that require careful planning and innovative solutions. In this article, we will discuss the challenges faced in scheduling maintenance for equipment with limited accessibility and explore potential solutions to overcome these difficulties.
The Importance of Preventive Maintenance
Preventive maintenance is an essential aspect of fleet management and equipment maintenance. By regularly inspecting and servicing equipment, businesses can identify potential issues before they become major problems. This proactive approach helps minimize downtime, reduce repair costs, and ensure the safety of operators and workers.
Fleet maintenance involves managing a range of vehicles and equipment, from trucks and trailers to forklifts and cranes. Each piece of machinery requires regular maintenance to ensure optimal performance. However, scheduling maintenance for equipment with limited accessibility can be challenging due to various factors.
Challenges in Scheduling Maintenance for Equipment with Limited Accessibility
Scheduling maintenance for equipment with limited accessibility poses several challenges that can impact fleet maintenance efficiency and overall productivity. Let's explore some of the key challenges:
1. Limited Access Points
Equipment with limited accessibility often has restricted entry points, making it difficult for maintenance personnel to reach critical components. This can result in longer maintenance times and increased labor costs. Technicians may need to use specialized tools or even disassemble parts of the equipment to gain access, further complicating the process.
To overcome this challenge, businesses can invest in innovative maintenance solutions such as remote monitoring and diagnostic tools. These technologies allow maintenance teams to assess the condition of equipment and identify potential issues without physically accessing the restricted areas. By leveraging real-time fleet data and actionable insights, businesses can streamline maintenance operations and reduce downtime.
2. Complex Equipment Layouts
Some equipment, such as large machinery or industrial plants, may have complex layouts with multiple interconnected components. This complexity can make maintenance scheduling more challenging, as technicians need to coordinate their efforts and ensure that all necessary tasks are completed.
One solution to address this challenge is to implement a comprehensive fleet management system that offers maintenance scheduling features. These systems enable businesses to create detailed maintenance plans, assign tasks to technicians, and track progress in real-time. By utilizing such tools, businesses can ensure that all necessary maintenance tasks are performed efficiently and effectively.
3. Specialized Knowledge and Skills
Maintaining equipment with limited accessibility often requires specialized knowledge and skills. Technicians need to be trained on the specific requirements of each piece of machinery and understand the potential risks associated with maintenance tasks.
To overcome this challenge, businesses can invest in training programs and certifications for their maintenance personnel. By ensuring that technicians have the necessary knowledge and skills, businesses can minimize the risk of errors or accidents during maintenance activities. Additionally, businesses can consider partnering with external maintenance service providers who specialize in maintaining equipment with limited accessibility.
4. Safety Considerations
Safety is a top priority when it comes to maintenance activities, especially for equipment with limited accessibility. Technicians may need to work in confined spaces or at heights, increasing the risk of accidents or injuries.
Businesses can address this challenge by implementing strict safety protocols and providing appropriate personal protective equipment (PPE) to maintenance personnel. Regular safety training and audits can help ensure that technicians are aware of the potential risks and take necessary precautions while performing maintenance tasks.
Potential Solutions
While scheduling maintenance for equipment with limited accessibility can be challenging, there are several potential solutions that businesses can explore:
1. Utilize Maintenance Automation
Advancements in technology have made maintenance automation a viable option for businesses. By leveraging IoT (Internet of Things) devices and sensors, businesses can collect real-time data on equipment performance and condition. This data can be used to automate maintenance scheduling, triggering maintenance tasks based on predefined criteria such as usage hours or performance thresholds.
Automation not only eliminates the need for manual scheduling but also ensures that maintenance tasks are performed at the optimal time to prevent breakdowns and minimize downtime.
2. Implement Predictive Maintenance
Predictive maintenance takes maintenance automation a step further by using advanced analytics and machine learning algorithms to predict equipment failures before they occur. By analyzing historical data and identifying patterns, businesses can anticipate maintenance needs and take proactive measures to prevent breakdowns.
Predictive maintenance can help optimize maintenance schedules by prioritizing tasks based on the likelihood of failure. This approach not only improves fleet maintenance efficiency but also reduces costs associated with reactive repairs.
3. Leverage Remote Monitoring and Diagnostics
Remote monitoring and diagnostic tools allow businesses to monitor equipment performance and condition in real-time, even for equipment with limited accessibility. By installing sensors and connecting equipment to a centralized monitoring system, businesses can receive instant alerts and notifications regarding potential issues.
Remote diagnostics enable maintenance teams to assess the condition of equipment without physically accessing restricted areas. This not only enhances safety but also improves maintenance efficiency by reducing the time required to identify and address issues.
Conclusion
Scheduling maintenance for equipment with limited accessibility presents unique challenges that require careful planning and innovative solutions. By utilizing technologies such as remote monitoring, maintenance automation, and predictive maintenance, businesses can overcome these challenges and ensure the smooth operation of their equipment.
Investing in comprehensive fleet management solutions and providing specialized training to maintenance personnel can further enhance fleet maintenance efficiency and reduce downtime. By adopting a proactive approach to maintenance scheduling, businesses can optimize their operations, minimize costs, and improve overall productivity.
Related Blogs
The benefits of implementing a preventive maintenance schedule for facility management
Read More