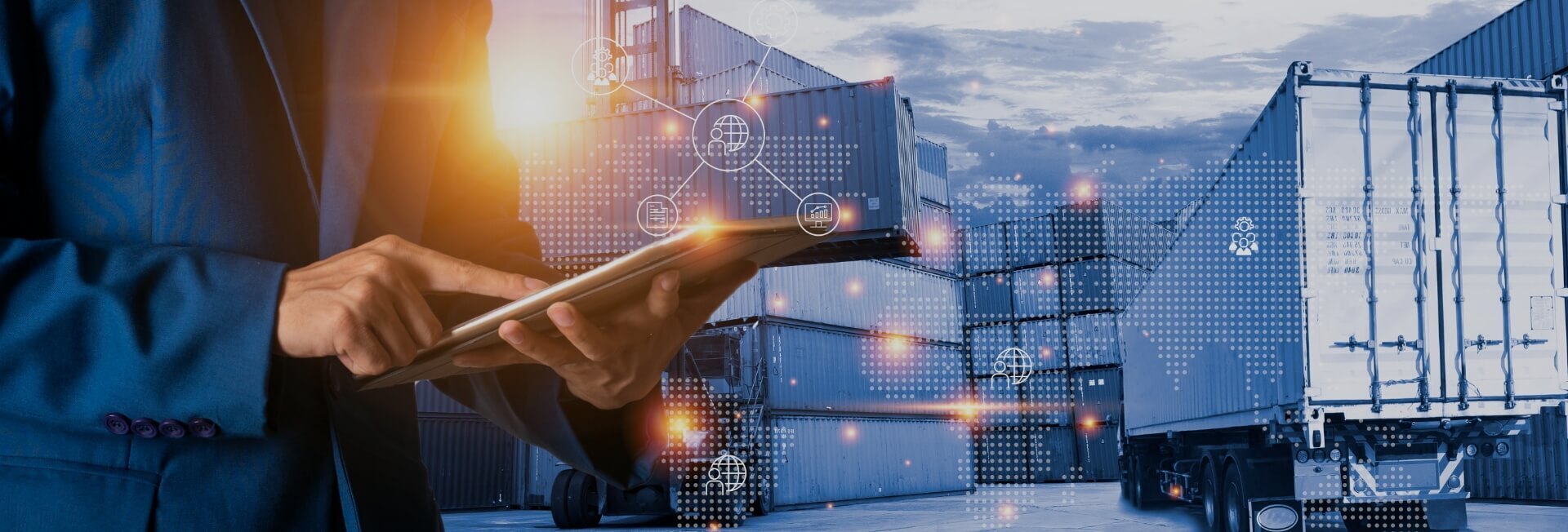
Challenges in scheduling maintenance for equipment with high variability in usage
- Home
- Resources
- Fleet Operations and Optimization
- Challenges in scheduling maintenance for equipment with high variability in usage
The Importance of Efficient Maintenance Scheduling for Equipment with High Usage Variability
Proper maintenance is crucial for the longevity and performance of equipment used in various industries. Whether it's a fleet of vehicles, production machinery, or specialized equipment, regular upkeep and repairs are necessary to ensure smooth operations and minimize downtime. However, scheduling maintenance for equipment with high variability in usage can present unique challenges that require careful planning and coordination.
Understanding the Challenges
Equipment with high variability in usage refers to assets that are utilized irregularly or have varying levels of demand. This could be due to seasonal fluctuations, project-based operations, or unexpected changes in workload. The challenges in scheduling maintenance for such equipment are as follows:
1. Unpredictable Workload
One of the main challenges in scheduling maintenance for equipment with high variability in usage is the unpredictable workload. Since the usage patterns are not consistent, it can be difficult to determine the optimal time for maintenance without disrupting operations. Performing maintenance during high-demand periods can lead to significant downtime and loss of productivity, while delaying maintenance during low-demand periods can result in increased risk of breakdowns and costly repairs.
2. Limited Availability of Resources
Another challenge is the limited availability of resources. In many cases, equipment with high usage variability requires specialized technicians or specific spare parts for maintenance and repairs. However, these resources may not be readily available or may need to be allocated to other critical tasks. This constraint can further complicate the scheduling process and affect the overall efficiency of maintenance operations.
3. Balancing Preventive and Reactive Maintenance
Efficient maintenance scheduling involves striking a balance between preventive and reactive maintenance. Preventive maintenance aims to proactively address potential issues before they escalate, while reactive maintenance focuses on addressing immediate breakdowns or malfunctions. With equipment that has high variability in usage, it becomes essential to determine the right proportion of preventive and reactive maintenance to minimize downtime and maximize equipment availability.
4. Limited Visibility and Data
High variability in equipment usage often leads to limited visibility and data regarding its condition and performance. Without real-time insights into equipment usage, maintenance history, and potential issues, it becomes challenging to make informed decisions about scheduling maintenance. This lack of data-driven insights can result in inefficient maintenance practices and increased risk of unexpected failures.
Addressing the Challenges
While scheduling maintenance for equipment with high variability in usage may pose challenges, there are several strategies and technologies that can help overcome these obstacles:
1. Implementing Predictive Maintenance
Predictive maintenance utilizes advanced technologies such as IoT sensors and data analytics to monitor equipment in real-time and predict potential failures or maintenance needs. By collecting and analyzing data on usage patterns, performance metrics, and other relevant factors, organizations can proactively schedule maintenance based on actual equipment condition rather than a fixed calendar-based approach. This approach optimizes maintenance efforts and reduces the risk of unexpected breakdowns.
2. Leveraging Fleet Tracking and Supply Chain Visibility
For industries that rely on fleets of vehicles or equipment, implementing fleet tracking and supply chain visibility solutions can provide valuable insights into usage patterns, location, and operational efficiency. By having real-time visibility into the fleet, organizations can identify opportunities for optimizing maintenance scheduling based on actual utilization and demand. This ensures that maintenance activities are aligned with the operational needs of the business.
3. Embracing Maintenance Automation
Automation plays a crucial role in streamlining maintenance scheduling for equipment with high variability in usage. By automating routine tasks such as data collection, analysis, and work order generation, organizations can free up valuable resources and ensure consistent and efficient maintenance practices. Additionally, automation enables real-time decision-making by providing actionable insights into equipment condition and maintenance requirements.
4. Adopting Data-Driven Fleet Management Solutions
Data-driven fleet management solutions offer comprehensive visibility and control over fleet operations, including maintenance scheduling. These solutions leverage real-time fleet data, historical performance metrics, and predictive analytics to optimize maintenance activities. By integrating maintenance schedules with other operational parameters such as driver availability, route planning, and fuel efficiency, organizations can achieve higher fleet maintenance efficiency and minimize downtime.
The Benefits of Efficient Maintenance Scheduling
Efficient maintenance scheduling for equipment with high variability in usage brings several benefits to organizations:
1. Reduced Downtime and Production Losses
By scheduling maintenance during low-demand periods and proactively addressing potential issues, organizations can minimize unplanned downtime and production losses. This ensures smooth operations and uninterrupted supply chain workflows.
2. Cost Savings
Efficient maintenance scheduling helps organizations optimize resource allocation and reduce unnecessary repairs or replacements. By avoiding breakdowns and addressing maintenance needs at the right time, organizations can save on costly emergency repairs and extend the lifespan of their equipment.
3. Improved Equipment Performance and Reliability
Regular maintenance, when scheduled efficiently, improves equipment performance and reliability. By addressing minor issues before they escalate, organizations can ensure that their equipment operates at optimal levels and delivers consistent results.
4. Enhanced Safety and Compliance
Proper maintenance scheduling ensures that equipment meets safety standards and regulatory requirements. Regular inspections, repairs, and replacements contribute to a safer working environment and reduce the risk of accidents or non-compliance penalties.
Conclusion
Scheduling maintenance for equipment with high variability in usage may present unique challenges, but with the right strategies and technologies, organizations can overcome these obstacles and achieve efficient maintenance practices. By leveraging predictive maintenance, fleet tracking, supply chain visibility, automation, and data-driven fleet management solutions, organizations can optimize maintenance schedules, reduce downtime, and maximize equipment performance. Efficient maintenance scheduling not only improves the reliability and lifespan of equipment but also contributes to overall operational efficiency and profitability.
Related Blogs
The benefits of implementing a preventive maintenance schedule for facility management
Read More