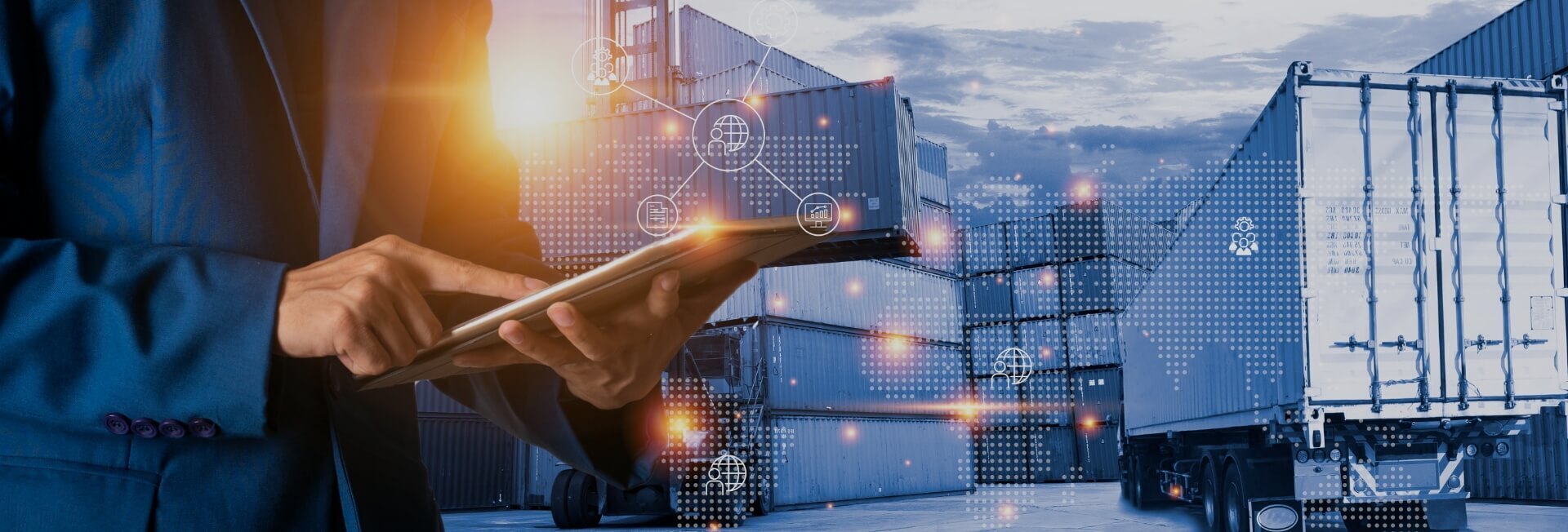
Challenges in scheduling maintenance for equipment with high maintenance costs
- Home
- Resources
- Fleet Operations and Optimization
- Challenges in scheduling maintenance for equipment with high maintenance costs
The Challenges of Scheduling Maintenance for Equipment with High Maintenance Costs
Equipment maintenance is an essential aspect of any business that relies on machinery, vehicles, or other equipment to operate. Regular maintenance helps prevent breakdowns, extends the life of the equipment, and ensures optimal performance. However, scheduling maintenance for equipment with high maintenance costs can be challenging. In this article, we will explore the difficulties faced in scheduling maintenance for such equipment and discuss potential solutions.
High Maintenance Costs and Preventive Maintenance
Equipment with high maintenance costs often requires frequent repairs and replacements, resulting in significant expenses for businesses. Preventive maintenance is a proactive approach to equipment maintenance that aims to identify and address potential issues before they lead to breakdowns or costly repairs. By following a preventive maintenance schedule, businesses can reduce the likelihood of unexpected downtime and minimize maintenance costs.
The Importance of Fleet Maintenance
Fleet maintenance is particularly crucial for businesses that rely on a fleet of vehicles to transport goods or provide services. Regular maintenance and repairs are necessary to keep the fleet in optimal condition, ensure driver safety, and minimize operational disruptions. Fleet tracking and supply chain visibility tools can provide actionable insights and help streamline logistics, allowing businesses to optimize their fleet maintenance schedules.
Challenges in Scheduling Maintenance for Equipment with High Maintenance Costs
Scheduling maintenance for equipment with high maintenance costs presents several challenges for businesses:
1. Limited Resources and Budget Constraints
Businesses with limited resources and budget constraints may struggle to allocate sufficient funds for equipment maintenance. High maintenance costs can quickly deplete the available budget, leaving little room for preventive maintenance activities. As a result, businesses may resort to reactive maintenance, addressing issues only when they arise, which can lead to more significant breakdowns and higher repair costs in the long run.
2. Balancing Maintenance and Operations
Scheduling maintenance for equipment with high maintenance costs requires striking a balance between maintenance activities and ongoing operations. Downtime for maintenance can disrupt production or service delivery, leading to potential revenue losses. Finding the right time and duration for maintenance without significantly impacting operations can be a complex task.
3. Limited Availability of Spare Parts
Some equipment with high maintenance costs may require specialized or uncommon spare parts for repairs. The limited availability of such parts can cause delays in maintenance activities, prolonging equipment downtime. Businesses may need to explore alternative suppliers or consider stocking spare parts in advance to address this challenge.
4. Complex Maintenance Schedules
Equipment with high maintenance costs often has complex maintenance requirements. The maintenance schedule may involve multiple tasks, such as inspections, lubrication, calibration, and component replacements. Coordinating and managing these tasks can be time-consuming and require specialized knowledge. Without a streamlined maintenance scheduling process, businesses may struggle to ensure all necessary maintenance activities are performed on time.
Potential Solutions and Strategies
While scheduling maintenance for equipment with high maintenance costs can be challenging, there are several potential solutions and strategies that businesses can adopt:
1. Prioritize Preventive Maintenance
Despite budget constraints, businesses should prioritize preventive maintenance to minimize unexpected breakdowns and costly repairs. By investing in regular inspections, lubrication, and other preventive measures, businesses can identify and address potential issues before they escalate. This approach can help reduce overall maintenance costs and extend the lifespan of the equipment.
2. Implement Fleet Maintenance Software
For businesses with a fleet of vehicles, implementing fleet maintenance software can streamline maintenance scheduling and improve fleet maintenance efficiency. These software solutions provide real-time fleet data, comprehensive fleet management capabilities, and automated maintenance scheduling. By leveraging technology, businesses can optimize their maintenance schedules, track vehicle repairs, and ensure timely maintenance tasks.
3. Outsource Maintenance Services
Outsourcing maintenance services can be a viable option for businesses with limited resources or specialized equipment. Third-party maintenance providers can offer expertise, access to spare parts, and streamlined maintenance processes. Outsourcing maintenance activities allows businesses to focus on their core operations while ensuring their equipment receives regular maintenance and repairs.
4. Invest in Predictive Maintenance Technologies
Predictive maintenance technologies use data-driven analytics and machine learning algorithms to predict equipment failures and recommend maintenance actions. By monitoring equipment performance and analyzing data in real-time, businesses can identify patterns and trends that indicate potential issues. This proactive approach to maintenance can help reduce downtime, optimize maintenance schedules, and minimize maintenance costs.
Conclusion
Scheduling maintenance for equipment with high maintenance costs can be challenging, but it is essential for businesses to ensure optimal equipment performance and minimize maintenance expenses. By prioritizing preventive maintenance, leveraging technology, outsourcing maintenance services when necessary, and investing in predictive maintenance technologies, businesses can overcome these challenges and optimize their maintenance schedules. Effective maintenance scheduling ultimately leads to improved equipment reliability, reduced downtime, and increased operational efficiency.
Related Blogs
The benefits of implementing a preventive maintenance schedule for facility management
Read More