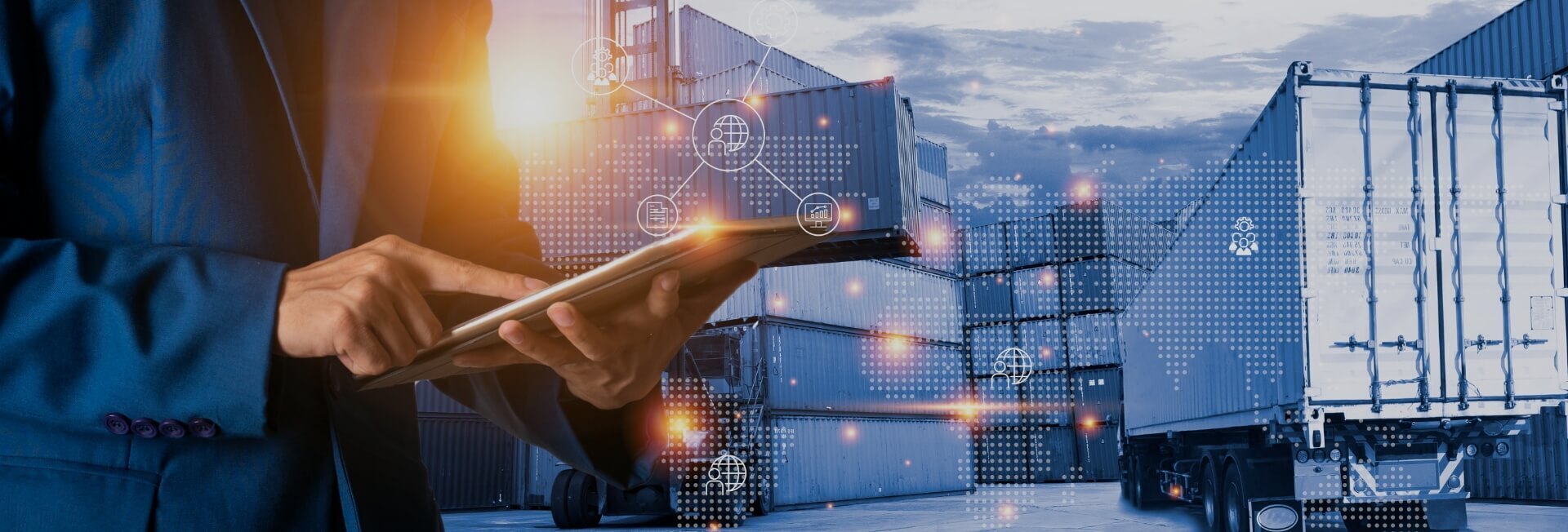
Challenges in scheduling maintenance for equipment with complex maintenance requirements
- Home
- Resources
- Fleet Operations and Optimization
- Challenges in scheduling maintenance for equipment with complex maintenance requirements
Introduction
Preventive maintenance is a crucial aspect of fleet management and logistics operations. It helps ensure that vehicles and equipment are in optimal condition, minimizing breakdowns and maximizing efficiency. However, scheduling maintenance for equipment with complex maintenance requirements can pose significant challenges for fleet managers. In this article, we will explore the complexities of scheduling maintenance for such equipment and discuss potential solutions.
The Importance of Preventive Maintenance
Before delving into the challenges, let's first understand the importance of preventive maintenance in fleet management. Preventive maintenance involves regularly inspecting, servicing, and repairing vehicles and equipment to prevent breakdowns and extend their lifespan. By proactively addressing maintenance needs, fleet managers can avoid costly repairs, reduce downtime, and ensure the safety of drivers and other road users.
Preventive maintenance also plays a vital role in optimizing supply chain operations. Well-maintained equipment is less likely to experience unexpected failures, ensuring smooth and uninterrupted logistics processes. It enables supply chain visibility and optimization, allowing businesses to make data-driven decisions and streamline their operations.
The Challenges of Complex Maintenance Requirements
Equipment with complex maintenance requirements presents unique challenges in scheduling preventive maintenance. These challenges stem from several factors, including:
1. Diverse Equipment Types
In many fleet operations, there is a wide variety of equipment types, each with its own specific maintenance needs. For example, a fleet may consist of trucks, trailers, forklifts, and other specialized equipment. Each type requires different maintenance tasks and intervals, making it difficult to create a standardized maintenance schedule.
2. Varying Maintenance Intervals
Even within the same equipment type, maintenance intervals can vary based on usage, environmental conditions, and other factors. For example, heavy-duty trucks that operate in harsh environments may require more frequent maintenance compared to those operating in mild conditions. Managing these varying maintenance intervals can be a logistical nightmare for fleet managers.
3. Parts Availability
Scheduling maintenance for equipment with complex maintenance requirements also involves ensuring the availability of the necessary parts and supplies. Some equipment may require specialized or hard-to-find parts, which can cause delays in the maintenance process. Fleet managers need to coordinate with suppliers and vendors to ensure timely availability of parts, adding another layer of complexity to the scheduling process.
4. Skill Requirements
Performing maintenance tasks on equipment with complex maintenance requirements often requires specialized skills and training. For example, servicing a refrigeration unit in a trailer may require technicians with expertise in HVAC systems. Fleet managers need to ensure that they have access to skilled technicians or outsource maintenance to qualified service providers, further complicating the scheduling process.
Solutions for Scheduling Maintenance
While scheduling maintenance for equipment with complex maintenance requirements can be challenging, there are several solutions that fleet managers can employ to streamline the process and improve efficiency:
1. Utilize Fleet Maintenance Software
Fleet maintenance software provides comprehensive fleet management solutions, including maintenance scheduling. These software solutions allow fleet managers to track maintenance tasks, set reminders for upcoming services, and automate the scheduling process. They also provide real-time fleet data and actionable insights, enabling data-driven decision-making and optimizing maintenance operations.
2. Implement Predictive Maintenance
Predictive maintenance leverages advanced technologies such as IoT sensors and machine learning algorithms to predict equipment failures before they occur. By analyzing real-time data from equipment, fleet managers can identify potential issues and schedule maintenance proactively. Implementing predictive maintenance can help minimize unexpected breakdowns, optimize maintenance schedules, and reduce overall maintenance costs.
3. Collaborate with Suppliers and Service Providers
Collaborating with suppliers and service providers is crucial for ensuring the availability of parts and skilled technicians. Fleet managers should establish strong relationships with vendors and communicate their maintenance requirements in advance. This collaboration can help minimize delays in parts procurement and ensure timely completion of maintenance tasks.
4. Standardize Maintenance Procedures
Standardizing maintenance procedures can simplify the scheduling process for equipment with complex maintenance requirements. By creating a set of standardized maintenance tasks and intervals for each equipment type, fleet managers can eliminate confusion and ensure consistency. This standardization also facilitates training and knowledge sharing among technicians, improving overall maintenance efficiency.
Conclusion
Scheduling maintenance for equipment with complex maintenance requirements is a challenging task for fleet managers. However, by leveraging fleet maintenance software, implementing predictive maintenance, collaborating with suppliers and service providers, and standardizing maintenance procedures, fleet managers can overcome these challenges and achieve efficient and effective maintenance scheduling. By ensuring optimal equipment performance, businesses can improve fleet efficiency, streamline logistics operations, and ultimately enhance their bottom line.
Related Blogs
The benefits of implementing a preventive maintenance schedule for facility management
Read More