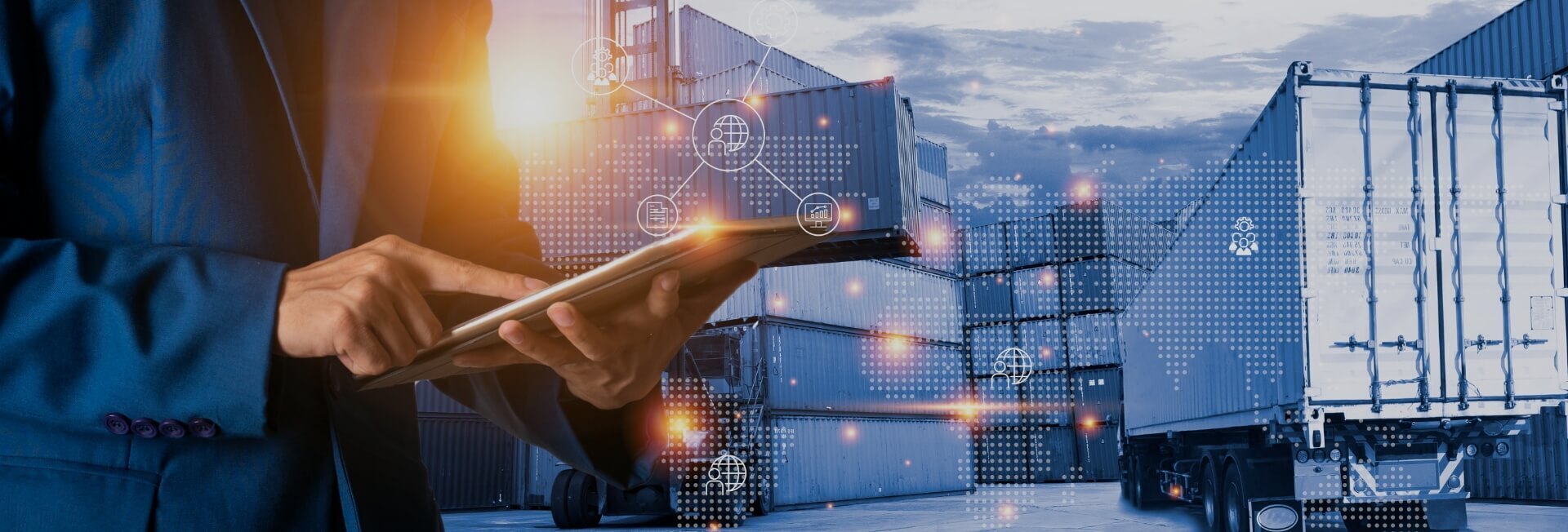
Challenges in scheduling maintenance for complex systems with multiple components
- Home
- Resources
- Fleet Operations and Optimization
- Challenges in scheduling maintenance for complex systems with multiple components
Challenges in Scheduling Maintenance for Complex Systems with Multiple Components
In today's fast-paced world, businesses rely heavily on complex systems to streamline their operations and achieve maximum efficiency. These systems often consist of multiple components that work together to deliver the desired outcome. However, ensuring the smooth functioning of these systems requires regular maintenance and repairs. Scheduling maintenance for such complex systems can be a daunting task, as it involves coordinating the availability of resources, managing logistics, and minimizing downtime. In this article, we will explore the challenges faced in scheduling maintenance for complex systems with multiple components and how to overcome them. We will also discuss the importance of preventive maintenance and the role of technology in streamlining maintenance scheduling.
The Importance of Preventive Maintenance
Preventive maintenance plays a crucial role in keeping complex systems operational and minimizing the risk of unexpected failures. It involves regularly inspecting, cleaning, and servicing the components to ensure their optimal performance. By identifying and addressing potential issues before they escalate, preventive maintenance helps in preventing costly breakdowns and reducing downtime. It also extends the lifespan of the components, resulting in long-term cost savings.
Fleet maintenance, for example, is a critical aspect of the logistics industry. Fleet operators need to ensure that their vehicles are in top condition to avoid breakdowns on the road. Regular maintenance checks, such as oil changes, tire rotations, and brake inspections, can significantly reduce the likelihood of mechanical failures. This, in turn, helps in maintaining a streamlined logistics process and ensures on-time delivery of goods.
The Complexity of Scheduling Maintenance for Multiple Components
When dealing with complex systems consisting of multiple components, scheduling maintenance becomes a complex task in itself. Each component may have its own maintenance requirements and schedules, making it challenging to coordinate and prioritize the maintenance activities. Additionally, the availability of resources, such as skilled technicians and spare parts, needs to be considered while scheduling maintenance. Failure to manage these factors effectively can lead to delays, increased costs, and operational disruptions.
Another challenge in scheduling maintenance for complex systems is the interdependency of components. A failure in one component may impact the performance of other components, requiring simultaneous maintenance. Coordinating the maintenance activities of interconnected components can be time-consuming and requires careful planning to minimize downtime. For example, in a manufacturing plant, if a critical machine breaks down, the entire production line may come to a halt, resulting in significant losses. Scheduling maintenance in such scenarios becomes crucial to ensure that all components are up and running as per their respective schedules.
Overcoming Maintenance Scheduling Challenges
While scheduling maintenance for complex systems with multiple components may seem challenging, there are several strategies that can help overcome these challenges:
1. Comprehensive Maintenance Planning:
Developing a comprehensive maintenance plan is essential to ensure that all components are adequately maintained. The plan should include a detailed schedule of maintenance activities for each component, taking into account their specific requirements and interdependencies. By having a clear roadmap of maintenance activities, businesses can prioritize tasks, allocate resources effectively, and minimize downtime.
2. Leveraging Technology:
Technology plays a crucial role in streamlining maintenance scheduling for complex systems. Fleet management software, for example, enables fleet operators to track the performance of their vehicles in real-time, monitor maintenance schedules, and receive automated alerts for upcoming service requirements. This helps in proactive planning and ensures that maintenance activities are carried out as per schedule.
Supply chain visibility solutions also play a vital role in maintenance scheduling. By providing real-time data on the performance of components and identifying potential issues, these solutions enable businesses to take proactive measures and prevent unexpected failures. They also help in optimizing supply chain operations by ensuring that maintenance activities do not disrupt the overall logistics process.
3. Collaborative Approach:
Maintenance scheduling for complex systems requires collaboration between different stakeholders, including maintenance teams, operations teams, and logistics teams. By involving all relevant parties in the planning process, businesses can ensure that maintenance activities are aligned with operational requirements and minimize disruptions. Regular communication and coordination are key to successful maintenance scheduling.
4. Data-Driven Decision Making:
Data is a valuable asset when it comes to maintenance scheduling. By leveraging real-time fleet data, businesses can gain actionable insights into the performance of components and make informed decisions regarding maintenance scheduling. Data-driven fleet management solutions help in identifying patterns, predicting failures, and optimizing maintenance schedules based on actual usage and performance data.
The Role of Technology in Streamlining Maintenance Scheduling
Technology plays a crucial role in streamlining maintenance scheduling for complex systems. Let's explore some of the key ways in which technology can help:
1. Automation:
Automation of maintenance scheduling tasks reduces the chances of human errors and ensures that maintenance activities are carried out as per schedule. Automated systems can generate maintenance schedules, send reminders for upcoming service requirements, and track the progress of maintenance activities. This not only saves time but also improves the overall efficiency of the maintenance process.
2. Predictive Maintenance:
Predictive maintenance uses advanced analytics and machine learning algorithms to predict potential failures before they occur. By analyzing real-time data from sensors and other sources, predictive maintenance systems can identify patterns and anomalies that indicate a potential issue. This enables businesses to take proactive measures and schedule maintenance activities accordingly, minimizing the risk of unexpected failures.
3. Remote Monitoring:
Remote monitoring solutions allow businesses to monitor the performance of components in real-time, even from a remote location. This eliminates the need for on-site inspections and enables proactive maintenance planning. Remote monitoring systems can provide real-time alerts for potential issues, allowing businesses to take immediate action and prevent downtime.
4. Integration with ERP Systems:
Integrating maintenance scheduling systems with enterprise resource planning (ERP) systems enables seamless coordination between maintenance activities and other business processes. For example, if a maintenance activity requires a specific spare part, the integration with the ERP system can automatically generate a purchase order and ensure timely availability of the part. This streamlines the overall maintenance process and minimizes delays.
Conclusion
Scheduling maintenance for complex systems with multiple components is a challenging task that requires careful planning, coordination, and the right technology tools. By adopting preventive maintenance practices, businesses can minimize the risk of unexpected failures and reduce downtime. Leveraging technology, such as fleet management software and supply chain visibility solutions, helps in streamlining maintenance scheduling and ensures efficient operations. Collaborative approaches and data-driven decision-making further enhance the effectiveness of maintenance scheduling. With the right strategies and tools in place, businesses can overcome the challenges and ensure the smooth functioning of their complex systems.
Related Blogs
The benefits of implementing a preventive maintenance schedule for facility management
Read More