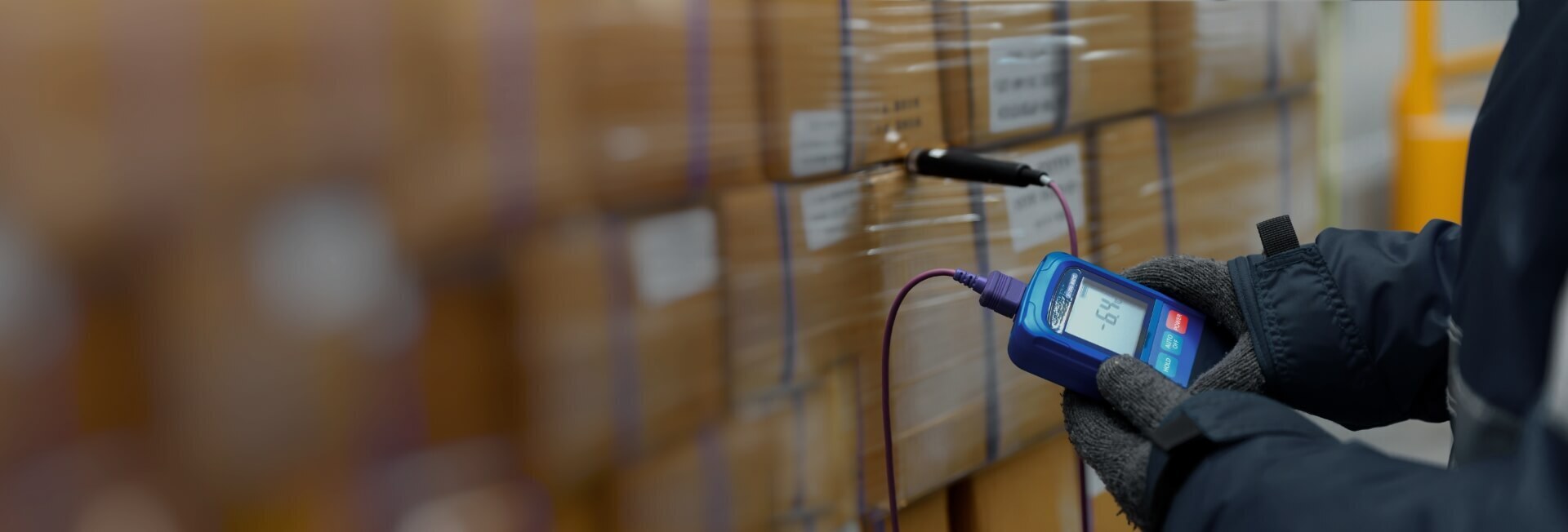
The role of value stream mapping in identifying waste and achieving streamlined manufacturing
- Home
- Resources
- Cooling Unit Manufacturing Insights
- The role of value stream mapping in identifying waste and achieving streamlined manufacturing
The Benefits of Value Stream Mapping in Streamlined Manufacturing
In today's competitive manufacturing landscape, companies are constantly seeking ways to optimize their supply chain, improve manufacturing efficiency, and reduce waste. One highly effective tool that has gained popularity is value stream mapping (VSM). VSM allows manufacturers to identify waste and inefficiencies in their processes, leading to more streamlined and sustainable operations.
What is Value Stream Mapping?
Value stream mapping is a lean manufacturing technique that visually represents the flow of materials, information, and processes involved in the production and distribution of goods or services. It provides a holistic view of the entire value stream, from the raw materials stage to the customer's hands. By identifying and eliminating non-value-added activities, VSM helps companies achieve greater efficiency and cost savings.
The Benefits of Value Stream Mapping
Value stream mapping offers several benefits to manufacturers, including:
1. Waste Identification
One of the main advantages of value stream mapping is its ability to identify various types of waste in manufacturing processes. Waste can be categorized into seven main types, including overproduction, waiting time, transportation, processing, inventory, motion, and defects. By visually mapping out the value stream, manufacturers can pinpoint areas of waste and take appropriate measures to eliminate or reduce them.
2. Streamlined Processes
Value stream mapping helps streamline manufacturing processes by identifying bottlenecks and areas of inefficiency. By analyzing the current state map and creating a future state map, manufacturers can identify opportunities for improvement, such as reducing cycle times, improving material flow, and optimizing resource allocation. This leads to smoother operations, shorter lead times, and increased productivity.
3. Improved Communication and Collaboration
Value stream mapping promotes better communication and collaboration among different departments and stakeholders involved in the value stream. By visually representing the entire process, VSM facilitates a common understanding of the current state and future objectives. This encourages cross-functional teams to work together towards a common goal, fostering a culture of continuous improvement and innovation.
4. Data-Driven Decision Making
Value stream mapping provides manufacturers with valuable data and insights that can drive informed decision making. By analyzing key performance indicators (KPIs) such as cycle time, lead time, and throughput, manufacturers can identify areas of improvement and prioritize resources accordingly. This data-driven approach helps manufacturers make strategic decisions that optimize efficiency and reduce waste.
How to Implement Value Stream Mapping
Implementing value stream mapping requires a systematic approach and active participation from all stakeholders. Here are the key steps involved:
1. Define the Scope
Begin by defining the boundaries of the value stream you want to map. Determine the starting and ending points, and identify the key processes and activities involved.
2. Create the Current State Map
Start by mapping out the current state of your value stream. This involves gathering data, observing processes, and interviewing employees. Use symbols and icons to represent different activities, flows, and inventory levels. This will give you a visual representation of the current state and help identify areas of waste and inefficiency.
3. Analyze and Identify Improvement Opportunities
Analyze the current state map and identify areas of waste and inefficiency. Look for bottlenecks, excessive inventory, long waiting times, and unnecessary processing steps. Brainstorm potential improvement opportunities and prioritize them based on their impact and feasibility.
4. Create the Future State Map
Based on the identified improvement opportunities, create a future state map that represents the ideal state of your value stream. This map should incorporate changes that eliminate or reduce waste, improve flow, and optimize resource allocation.
5. Develop an Implementation Plan
Once the future state map is created, develop an implementation plan that outlines the necessary steps, resources, and timeline for achieving the desired state. Assign responsibilities to individuals or teams and establish a process for monitoring progress and making adjustments as needed.
Conclusion
Value stream mapping is a powerful tool for identifying waste, streamlining processes, and achieving more efficient and sustainable manufacturing operations. By visually representing the flow of materials, information, and processes, manufacturers can pinpoint areas of waste and take appropriate measures to eliminate or reduce them. The benefits of value stream mapping include waste identification, streamlined processes, improved communication and collaboration, and data-driven decision making. By implementing value stream mapping and continually striving for improvement, manufacturers can optimize their supply chain, reduce costs, and stay ahead in today's competitive market.
Related Blogs
The importance of education and awareness in promoting the adoption of green cooling technology
Read More