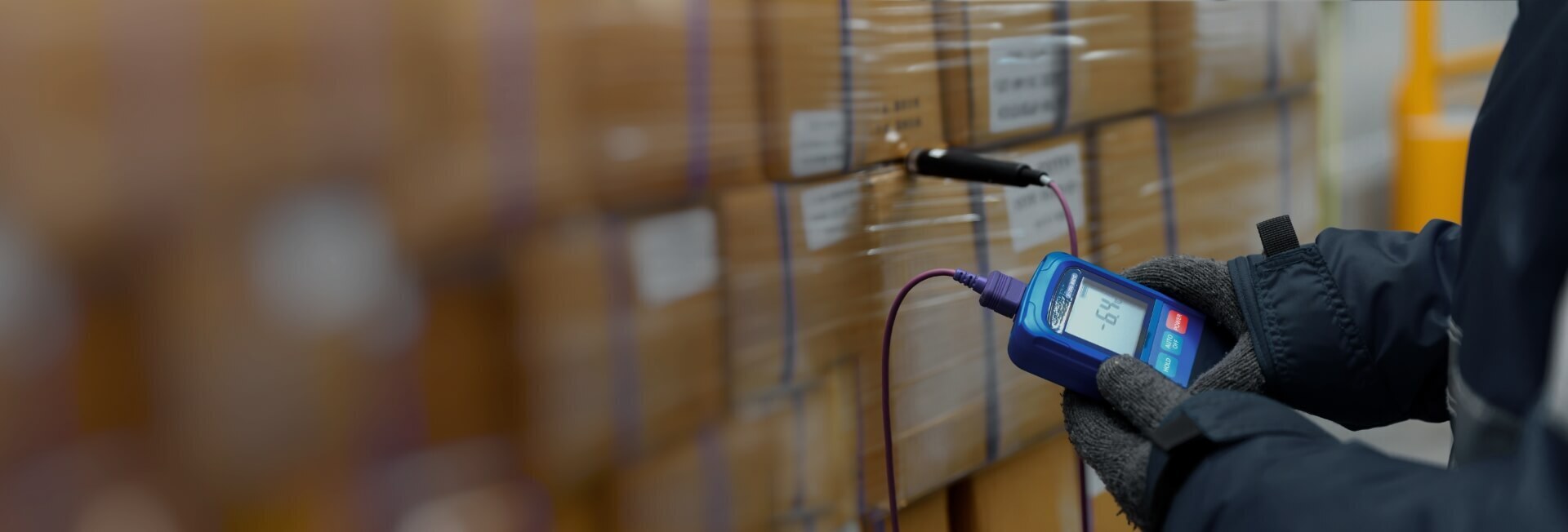
The role of value stream mapping in identifying and eliminating waste in manufacturing
- Home
- Resources
- Cooling Unit Manufacturing Insights
- The role of value stream mapping in identifying and eliminating waste in manufacturing
The Power of Value Stream Mapping in Manufacturing Efficiency
Manufacturing efficiency is a crucial aspect of any business that aims to be successful in today's competitive market. One way to achieve manufacturing efficiency is through the use of value stream mapping. This powerful tool allows businesses to identify and eliminate waste in their manufacturing processes, resulting in streamlined operations, cost savings, and improved overall performance.
What is Value Stream Mapping?
Value stream mapping is a lean manufacturing technique that visually represents the flow of materials, information, and activities involved in the production and distribution of a product. It provides a comprehensive view of the entire manufacturing process, from raw materials to finished goods, and helps identify areas of waste and inefficiency.
By mapping out the value stream, businesses can identify bottlenecks, unnecessary steps, and excessive inventory, among other waste factors. This allows them to make informed decisions and implement targeted improvements to increase efficiency and reduce costs.
The Benefits of Value Stream Mapping
Implementing value stream mapping in manufacturing offers numerous benefits for businesses:
1. Waste Identification and Elimination
Value stream mapping enables businesses to identify different types of waste, such as overproduction, waiting time, unnecessary transportation, defects, and excess inventory. By visualizing the entire value stream, businesses can pinpoint areas of waste and take appropriate actions to eliminate or reduce them.
For example, value stream mapping may reveal that a certain process is causing excess inventory due to overproduction. By addressing the root cause of this waste, such as adjusting production levels or improving coordination between departments, businesses can reduce inventory costs and improve overall efficiency.
2. Improved Process Flow
Value stream mapping helps businesses understand the flow of materials, information, and activities throughout the manufacturing process. By analyzing this flow, businesses can identify and eliminate bottlenecks, unnecessary handoffs, and other obstacles that hinder the smooth flow of production.
For example, value stream mapping may reveal that a particular process is causing delays and bottlenecks due to excessive handoffs between departments. By redesigning the process to minimize handoffs or improve coordination, businesses can improve process flow, reduce lead times, and increase overall productivity.
3. Enhanced Communication and Collaboration
Value stream mapping involves cross-functional collaboration and communication between different departments and stakeholders. This collaborative approach helps break down silos and fosters a culture of continuous improvement.
By involving employees from different areas of the value stream in the mapping process, businesses can gain valuable insights and perspectives. This not only helps identify areas of waste but also encourages employees to take ownership of the process and contribute to finding solutions.
4. Data-Driven Decision Making
Value stream mapping is a data-driven approach that relies on accurate and up-to-date information about the manufacturing process. By collecting and analyzing relevant data, businesses can make informed decisions and prioritize improvement initiatives based on the impact they will have on overall efficiency.
For example, data analysis may reveal that a specific machine is causing frequent breakdowns, resulting in production delays. By addressing the issue with preventive maintenance or investing in a more reliable machine, businesses can reduce downtime and improve overall productivity.
Conclusion
Value stream mapping is a powerful tool for identifying and eliminating waste in manufacturing processes. By visualizing the entire value stream, businesses can identify areas of waste and implement targeted improvements to increase efficiency and reduce costs.
Through waste identification and elimination, improved process flow, enhanced communication and collaboration, and data-driven decision making, businesses can achieve sustainable manufacturing efficiency and gain a competitive edge in the market.
Related Blogs
The importance of education and awareness in promoting the adoption of green cooling technology
Read More