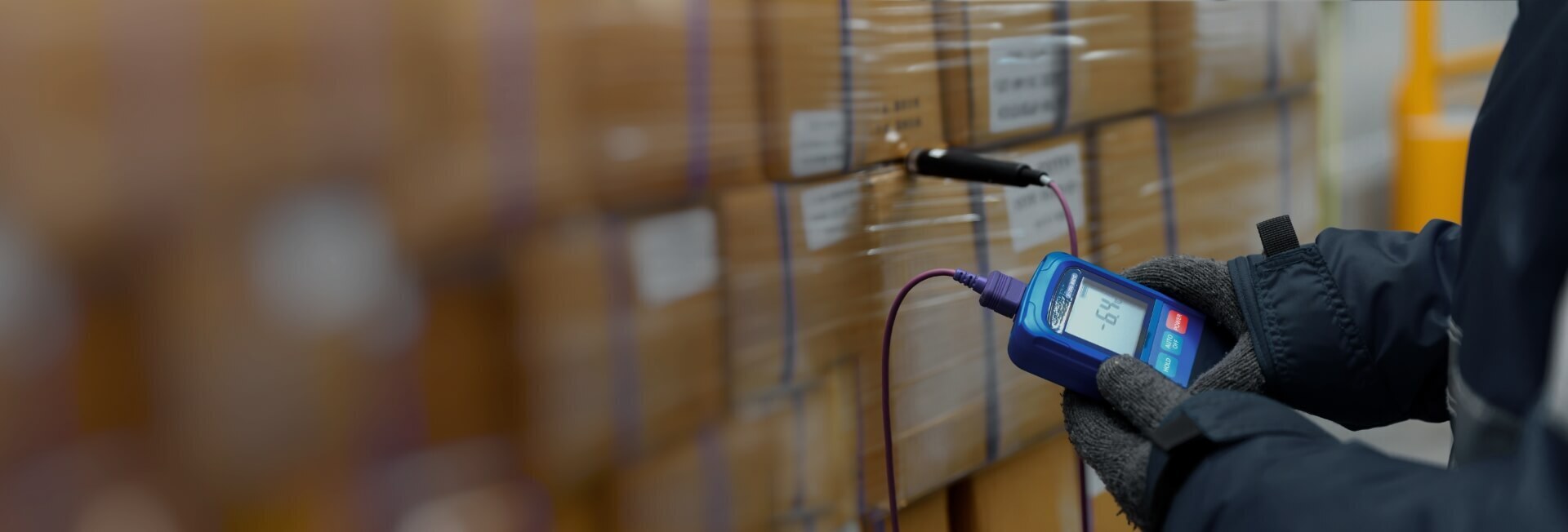
The role of value stream analysis in achieving streamlined manufacturing processes
- Home
- Resources
- Cooling Unit Manufacturing Insights
- The role of value stream analysis in achieving streamlined manufacturing processes
The Role of Value Stream Analysis in Achieving Streamlined Manufacturing Processes
In today's competitive manufacturing landscape, efficiency and effectiveness are crucial for success. Manufacturers are constantly looking for ways to optimize their supply chain, improve manufacturing processes, and reduce waste. One powerful tool that has emerged in recent years is value stream analysis.
What is Value Stream Analysis?
Value stream analysis, also known as value stream mapping, is a lean manufacturing technique that visualizes the flow of materials and information required to produce a product or service. It identifies and eliminates waste in the production process to improve efficiency and reduce costs.
Value stream analysis involves creating a visual representation of the entire value stream, from raw materials to the customer. It maps out each step in the process, including any delays or bottlenecks, and identifies areas for improvement.
Benefits of Value Stream Analysis
Value stream analysis offers several benefits for manufacturers looking to streamline their processes:
1. Increased Efficiency
By mapping out the entire value stream, manufacturers can identify areas of waste and inefficiency. This allows them to streamline their processes and eliminate unnecessary steps or delays. By reducing waste and improving flow, manufacturers can increase their overall efficiency and productivity.
2. Reduced Lead Times
Value stream analysis helps manufacturers identify bottlenecks and delays in their production process. By eliminating these bottlenecks and improving flow, manufacturers can reduce lead times and deliver products to customers more quickly.
3. Cost Savings
By eliminating waste and improving efficiency, manufacturers can reduce costs associated with production and distribution. This can lead to significant cost savings and improved profitability.
4. Improved Quality
Value stream analysis allows manufacturers to identify areas where quality issues may arise. By addressing these issues early on, manufacturers can improve the overall quality of their products and reduce the likelihood of defects or customer complaints.
Implementing Value Stream Analysis
Implementing value stream analysis involves several steps:
1. Identify the Value Stream
The first step in value stream analysis is identifying the value stream for a particular product or service. This involves mapping out the entire process, from raw materials to the customer. It's important to include all steps in the process, including any delays or bottlenecks.
2. Analyze the Current State
Once the value stream has been identified, the next step is to analyze the current state. This involves mapping out the current flow of materials and information and identifying any areas of waste or inefficiency. It's important to gather data and metrics to support the analysis.
3. Design the Future State
After analyzing the current state, the next step is to design the future state. This involves creating a vision for the ideal value stream, with improved flow and reduced waste. It's important to involve all stakeholders in the design process to ensure buy-in and collaboration.
4. Implement and Continuously Improve
The final step in value stream analysis is to implement the changes identified in the future state. This may involve process redesign, investment in new technology or equipment, or changes to the organizational structure. Once the changes have been implemented, it's important to continuously monitor and improve the value stream to ensure ongoing efficiency and effectiveness.
Value Stream Analysis in Manufacturing Cooling Systems
Value stream analysis can be particularly valuable in the manufacturing of cooling systems. Cooling technology is essential for a wide range of industries, from data centers to food processing. Streamlining the production and distribution of cooling units can lead to significant cost savings and improved customer satisfaction.
Commercial cooling units are complex products that require precise manufacturing processes. By applying value stream analysis, cooling system manufacturers can identify areas of waste and inefficiency in their production process. This can include delays in sourcing components, bottlenecks in assembly, or excessive inventory levels.
Custom cooling solutions are also becoming increasingly popular, as industries have unique cooling requirements. Value stream analysis can help manufacturers identify ways to streamline the production of custom cooling solutions, reducing lead times and improving customer satisfaction.
In addition to improving efficiency and reducing waste, value stream analysis in the manufacturing of cooling systems can also contribute to energy efficiency and sustainability. Precision cooling systems that are designed to be environmentally friendly and energy-efficient are in high demand. By streamlining the manufacturing process, manufacturers can reduce their environmental impact and meet the growing demand for sustainable cooling solutions.
Conclusion
Value stream analysis is a powerful tool for manufacturers looking to streamline their processes and achieve greater efficiency. By mapping out the entire value stream and identifying areas of waste and inefficiency, manufacturers can make targeted improvements that lead to cost savings, reduced lead times, improved quality, and sustainability. In the manufacturing of cooling systems, value stream analysis can be particularly valuable, as it can lead to energy-efficient and environmentally friendly cooling solutions. Implementing value stream analysis requires a commitment to continuous improvement and collaboration among all stakeholders. By embracing this lean technique, manufacturers can achieve streamlined manufacturing processes and gain a competitive edge in the market.
Related Blogs
The importance of education and awareness in promoting the adoption of green cooling technology
Read More