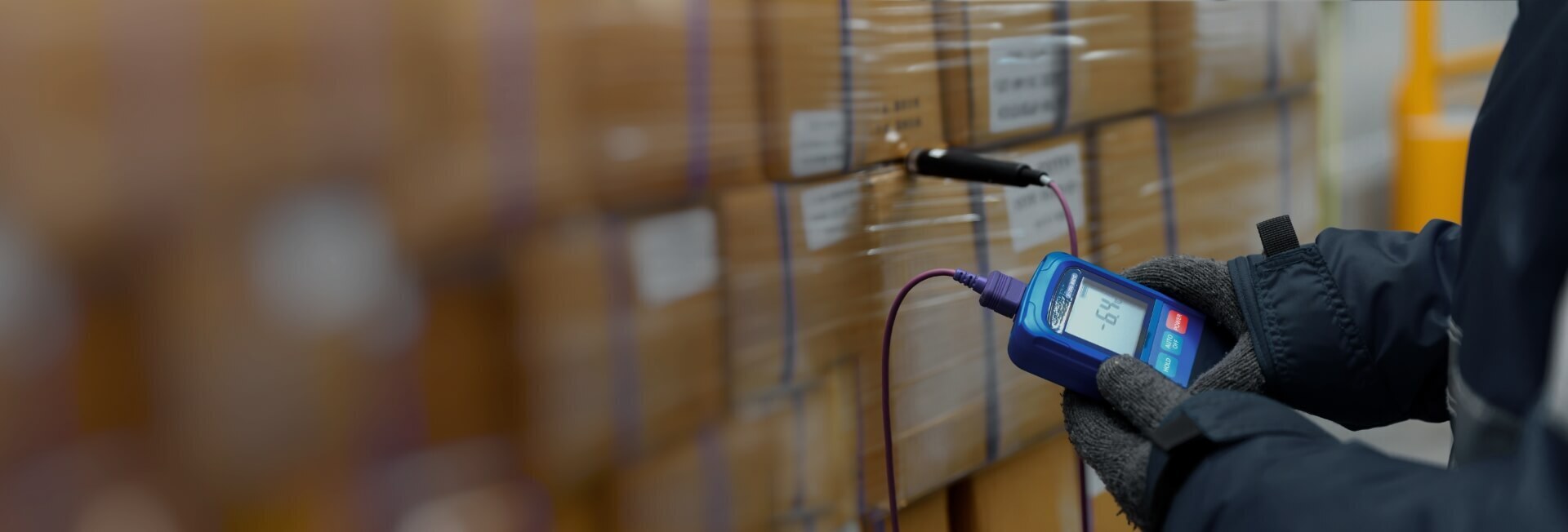
The role of total quality management in achieving streamlined manufacturing processes
- Home
- Resources
- Cooling Unit Manufacturing Insights
- The role of total quality management in achieving streamlined manufacturing processes
The Role of Total Quality Management in Achieving Streamlined Manufacturing Processes
In today's highly competitive manufacturing industry, businesses are constantly striving to improve efficiency, reduce waste, and optimize their supply chain. One approach that has gained significant traction in recent years is total quality management (TQM). TQM is a comprehensive management philosophy that focuses on continuous improvement, customer satisfaction, and waste reduction. By implementing TQM principles and practices, manufacturers can achieve streamlined processes, higher productivity, and ultimately, increased profitability.
What is Total Quality Management?
Total quality management is a holistic approach to managing an organization with the aim of continuously improving the quality of products, services, and processes. It is a customer-centric philosophy that emphasizes the importance of meeting or exceeding customer expectations. TQM is not a one-time program or initiative; it is an ongoing commitment to excellence and continuous improvement.
At its core, TQM is about involving every employee in the organization in the pursuit of quality. It encourages a culture of teamwork, open communication, and accountability. TQM principles can be applied to all aspects of a manufacturing business, from product design and development to production and distribution.
The Benefits of Total Quality Management in Manufacturing
Implementing total quality management in manufacturing can yield numerous benefits for businesses. Here are some of the key advantages:
1. Improved Efficiency and Productivity
TQM focuses on eliminating waste, optimizing processes, and improving efficiency. By streamlining production processes and reducing non-value-added activities, manufacturers can increase productivity and output. Through the use of lean manufacturing techniques, such as just-in-time (JIT) inventory management and continuous flow production, manufacturers can achieve significant improvements in efficiency.
2. Enhanced Customer Satisfaction
One of the primary objectives of TQM is to meet or exceed customer expectations. By consistently delivering high-quality products that meet customer requirements, manufacturers can build trust and loyalty with their customers. This can lead to increased customer satisfaction, repeat business, and positive word-of-mouth referrals.
3. Reduced Waste and Costs
Waste reduction is a central tenet of total quality management. By eliminating waste in all its forms, such as defects, overproduction, excess inventory, and unnecessary processing, manufacturers can lower costs and improve profitability. TQM techniques, such as value stream mapping and Kaizen events, can help identify and eliminate waste throughout the entire manufacturing process.
4. Continuous Improvement
TQM is a philosophy of continuous improvement. It encourages manufacturers to constantly look for ways to enhance their processes, products, and services. By fostering a culture of innovation and learning, organizations can stay ahead of the competition and adapt to changing market conditions. Continuous improvement is not limited to the manufacturing floor; it extends to all aspects of the business, including customer service, supplier relationships, and employee development.
Implementing Total Quality Management in Manufacturing
Successfully implementing total quality management in manufacturing requires a systematic approach and the commitment of top management. Here are some steps to consider:
1. Leadership Commitment
Top management must demonstrate a strong commitment to TQM and lead by example. They should set clear quality objectives, communicate them to the entire organization, and provide the necessary resources and support to achieve those objectives. Leadership commitment is critical to the success of any TQM initiative.
2. Employee Involvement
TQM cannot be successful without the active involvement and participation of every employee. Manufacturers should create a culture that encourages employee engagement, teamwork, and continuous improvement. Employees should be empowered to identify and solve problems, make suggestions for improvement, and contribute to the overall success of the organization.
3. Process Improvement
TQM emphasizes the importance of process improvement. Manufacturers should regularly review and analyze their processes to identify opportunities for improvement. Tools such as process mapping, root cause analysis, and statistical process control can help identify areas of inefficiency, defects, and waste. By systematically improving processes, manufacturers can achieve higher levels of quality and efficiency.
4. Supplier Partnerships
Suppliers play a critical role in the success of any manufacturing business. It is essential to establish strong partnerships with suppliers who share the same commitment to quality and continuous improvement. By working closely with suppliers, manufacturers can ensure the timely delivery of high-quality materials and components, reducing the risk of defects and delays in production.
Conclusion
Total quality management is a powerful approach to achieving streamlined manufacturing processes, improving efficiency, and reducing waste. By implementing TQM principles and practices, manufacturers can enhance customer satisfaction, increase productivity, and drive sustainable growth. TQM is not a quick fix; it requires a long-term commitment and the active involvement of every employee. However, the benefits of TQM far outweigh the challenges, making it a worthwhile investment for any manufacturing business.
Related Blogs
The importance of education and awareness in promoting the adoption of green cooling technology
Read More