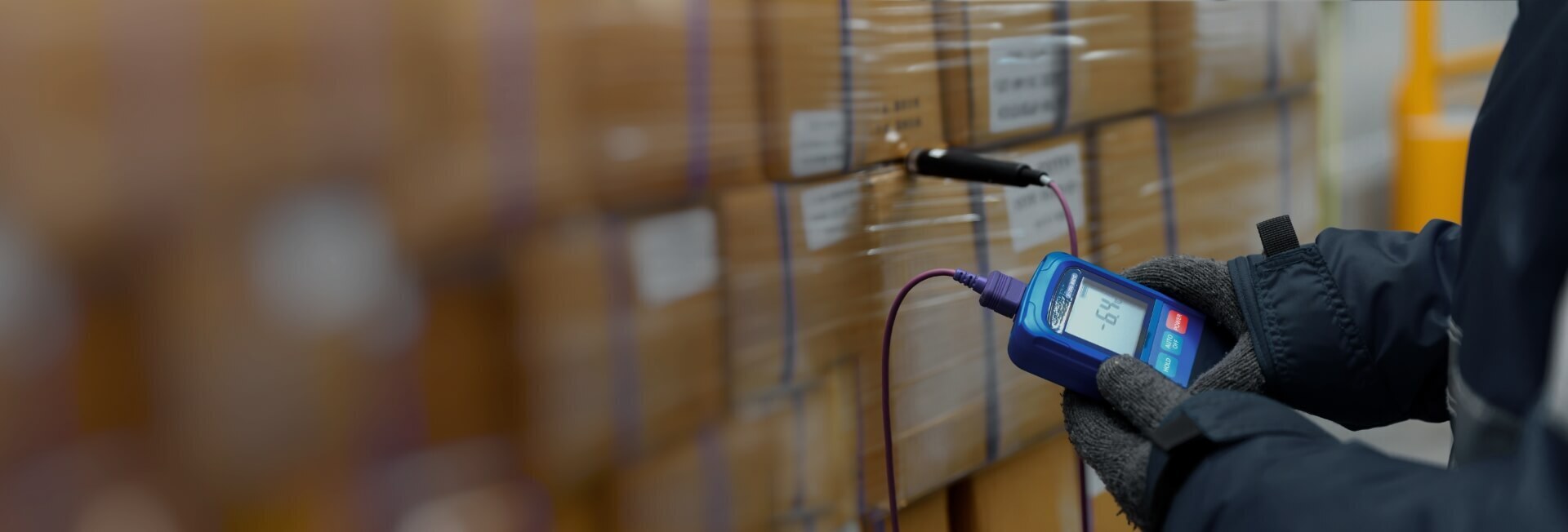
The role of total productive maintenance in achieving streamlined manufacturing processes
- Home
- Resources
- Cooling Unit Manufacturing Insights
- The role of total productive maintenance in achieving streamlined manufacturing processes
The Importance of Total Productive Maintenance in Streamlined Manufacturing
Streamlined manufacturing processes are crucial for organizations to maintain a competitive edge in today's fast-paced business environment. One of the key factors in achieving streamlined manufacturing is the implementation of total productive maintenance (TPM) practices. TPM focuses on maximizing equipment effectiveness, minimizing downtime, and ultimately improving overall operational efficiency. In this article, we will explore the role of TPM in achieving streamlined manufacturing processes and its impact on the overall success of an organization.
What is Total Productive Maintenance?
Total productive maintenance is a holistic approach to equipment maintenance that aims to achieve zero breakdowns, zero defects, and zero accidents. It involves the active participation of all employees, from the maintenance department to the production line, in the pursuit of continuous improvement. TPM emphasizes proactive maintenance rather than reactive repairs, with the goal of eliminating unplanned downtime and improving overall equipment effectiveness.
At its core, TPM focuses on three main goals:
1. Maximizing Equipment Effectiveness
The first goal of TPM is to maximize the effectiveness of equipment through proactive maintenance practices. This includes regular inspections, preventive maintenance, and prompt repairs. By identifying and addressing potential issues before they escalate into major problems, organizations can minimize unplanned downtime and improve the overall reliability of their equipment.
By implementing TPM practices, organizations can also ensure that equipment is operating at peak performance levels. This includes optimizing settings, calibrations, and alignments to maximize productivity and minimize energy consumption. By maximizing equipment effectiveness, organizations can achieve higher production outputs with fewer resources, leading to improved manufacturing efficiency.
2. Minimizing Downtime
Another key goal of TPM is to minimize downtime through effective maintenance practices. Downtime can have a significant impact on production schedules, customer satisfaction, and overall profitability. By implementing TPM practices, organizations can reduce unplanned downtime by identifying and addressing potential issues before they cause equipment failure.
TPM also emphasizes the importance of quick and efficient repairs when equipment does break down. By having well-trained maintenance personnel and a clear maintenance schedule in place, organizations can minimize the time required to fix equipment issues and get production back on track.
3. Improving Overall Operational Efficiency
The ultimate goal of TPM is to improve overall operational efficiency by optimizing equipment performance and minimizing waste. By focusing on preventive maintenance rather than reactive repairs, organizations can reduce the amount of time and resources spent on correcting equipment issues.
TPM also encourages the involvement of all employees in the maintenance process. This includes training operators to conduct routine inspections, identify early signs of equipment failure, and perform basic maintenance tasks. By empowering employees to take an active role in equipment maintenance, organizations can improve overall operational efficiency and create a culture of continuous improvement.
The Role of TPM in Streamlined Manufacturing
TPM plays a critical role in achieving streamlined manufacturing processes by ensuring that equipment is running at optimal levels and downtime is minimized. By implementing TPM practices, organizations can achieve the following benefits:
1. Increased Productivity
By maximizing equipment effectiveness and minimizing downtime, TPM helps organizations achieve higher production outputs with fewer resources. This leads to increased productivity and improved manufacturing efficiency. With TPM, organizations can optimize their manufacturing processes to meet customer demands more effectively and stay ahead of the competition.
2. Reduced Costs
TPM can also help organizations reduce costs by minimizing equipment failures, repairs, and unplanned downtime. By addressing potential issues before they cause major problems, organizations can avoid costly repairs and production delays. Additionally, TPM encourages the efficient use of resources, such as energy and materials, leading to cost savings and improved sustainability.
3. Improved Quality
TPM emphasizes the importance of preventive maintenance and continuous improvement, which can lead to improved product quality. By ensuring that equipment is operating at optimal levels, organizations can minimize defects and errors in the manufacturing process. This results in higher-quality products and increased customer satisfaction.
4. Engaged Workforce
TPM promotes a culture of employee engagement and empowerment. By involving all employees in the maintenance process, organizations can tap into their knowledge and expertise to identify potential issues and implement improvement initiatives. This not only improves overall operational efficiency but also boosts employee morale and satisfaction.
Conclusion
Total productive maintenance plays a crucial role in achieving streamlined manufacturing processes by maximizing equipment effectiveness, minimizing downtime, and improving overall operational efficiency. By implementing TPM practices, organizations can increase productivity, reduce costs, improve product quality, and engage their workforce. As manufacturing processes become increasingly complex and competitive, TPM is essential for organizations to stay ahead and maintain a sustainable advantage.
Related Blogs
The importance of education and awareness in promoting the adoption of green cooling technology
Read More