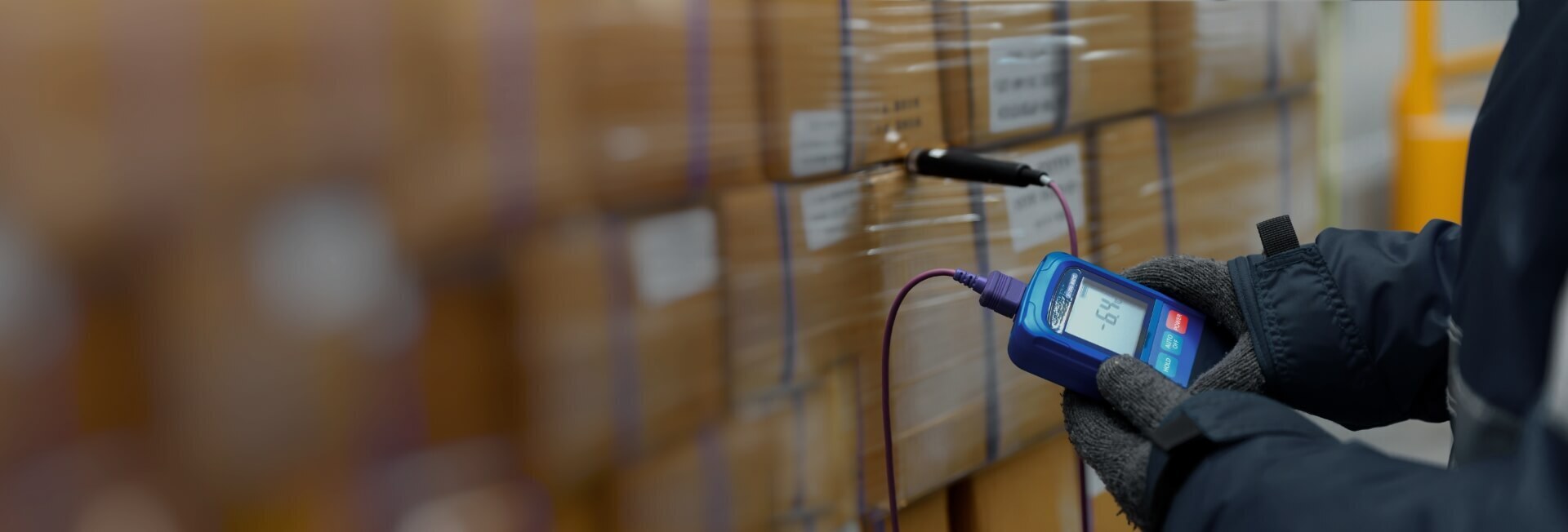
The role of quality control circles in achieving streamlined manufacturing processes
- Home
- Resources
- Cooling Unit Manufacturing Insights
- The role of quality control circles in achieving streamlined manufacturing processes
The Role of Quality Control Circles in Achieving Streamlined Manufacturing Processes
In today's competitive business environment, manufacturing companies are constantly seeking ways to optimize their supply chain, improve manufacturing efficiency, and reduce costs. One of the key strategies they employ is the implementation of quality control circles. These circles, also known as QC circles or quality circles, are small groups of employees who come together to identify and solve problems related to production and distribution. In this article, we will explore the role of quality control circles in achieving streamlined manufacturing processes and how they contribute to the overall success of a company.
What are Quality Control Circles?
Quality control circles are a concept that originated in Japan in the 1960s and have since been adopted by companies worldwide. These circles consist of a group of employees from different departments or areas of expertise who meet regularly to discuss and analyze problems related to their work. The main objective of quality control circles is to improve the quality of products or services, enhance productivity, and promote employee involvement and empowerment.
The Benefits of Quality Control Circles
Implementing quality control circles in a manufacturing company can have numerous benefits, including:
1. Problem-solving: Quality control circles provide a platform for employees to identify and solve problems related to their work. By working together in a supportive environment, employees can brainstorm ideas, analyze root causes, and develop effective solutions. This collaborative problem-solving approach can lead to innovative ideas and improvements in manufacturing processes.
2. Employee Engagement: Quality control circles promote employee involvement and engagement. When employees are given the opportunity to contribute to the decision-making process and have a say in how things are done, they feel valued and motivated. This increased engagement can result in higher job satisfaction, improved morale, and increased productivity.
3. Continuous Improvement: Quality control circles foster a culture of continuous improvement within the organization. By regularly evaluating and analyzing processes, employees can identify areas for improvement and implement changes to increase efficiency and reduce waste. This focus on continuous improvement is essential for staying competitive in today's fast-paced business environment.
4. Knowledge Sharing: Quality control circles provide a platform for employees to share their knowledge and expertise. By bringing together employees from different departments or areas of expertise, quality control circles encourage cross-functional collaboration and knowledge transfer. This sharing of knowledge can lead to a better understanding of the overall manufacturing process and help identify opportunities for improvement.
Implementing Quality Control Circles
Implementing quality control circles requires careful planning and consideration. Here are some steps to follow:
1. Training and Education: Before implementing quality control circles, it is essential to provide training and education to employees. This training should include an introduction to quality control circle concepts, problem-solving techniques, and effective communication skills. By equipping employees with the necessary knowledge and skills, they will be better prepared to actively participate in quality control circles.
2. Formation of Circles: Once employees have received the necessary training, quality control circles can be formed. These circles should consist of a diverse group of employees who have a stake in the manufacturing process. It is important to ensure that the circle members represent different departments or areas of expertise to encourage cross-functional collaboration.
3. Setting Objectives: Each quality control circle should have clear objectives and goals. These objectives should be aligned with the overall goals of the company and focus on improving specific aspects of the manufacturing process. By setting clear objectives, quality control circles can stay focused and measure their progress towards achieving their goals.
4. Regular Meetings: Quality control circles should meet regularly to discuss and analyze problems, generate ideas, and develop solutions. These meetings should be structured and facilitated to ensure productive discussions and effective problem-solving. It is important to establish a supportive and inclusive environment where all members feel comfortable sharing their ideas and opinions.
Success Stories: Examples of Quality Control Circles in Action
Many manufacturing companies have successfully implemented quality control circles and achieved significant improvements in their manufacturing processes. Here are some examples:
1. Commercial Cooling Units: A leading manufacturer of commercial cooling units implemented quality control circles to improve the energy-efficiency of their products. The quality control circles identified areas where energy was being wasted and developed innovative solutions to reduce energy consumption. As a result, the company was able to produce more energy-efficient cooling units, reducing their environmental impact and saving on energy costs.
2. Precision Cooling Systems: A manufacturer of precision cooling systems implemented quality control circles to streamline their manufacturing processes and reduce lead times. The quality control circles analyzed the various steps involved in the production process and identified areas where bottlenecks were occurring. By implementing changes such as reorganizing workstations and improving communication between departments, the company was able to reduce lead times by 30% and improve overall efficiency.
3. Custom Cooling Solutions: A manufacturer of custom cooling solutions implemented quality control circles to address customer complaints and improve product quality. The quality control circles analyzed customer feedback and identified common issues. They then worked together to develop solutions and implemented changes to address these issues. As a result, the company saw a significant reduction in customer complaints and an improvement in customer satisfaction.
Conclusion
Quality control circles play a crucial role in achieving streamlined manufacturing processes and improving efficiency in the production and distribution of goods. By providing a platform for employees to identify and solve problems, promoting employee engagement, fostering a culture of continuous improvement, and facilitating knowledge sharing, quality control circles contribute to the overall success of a company. Implementing quality control circles requires careful planning, training, and the establishment of clear objectives, but the benefits are well worth the effort. By embracing quality control circles, manufacturing companies can optimize their supply chain, improve manufacturing efficiency, and stay competitive in today's rapidly changing business landscape.
Related Blogs
The importance of education and awareness in promoting the adoption of green cooling technology
Read More