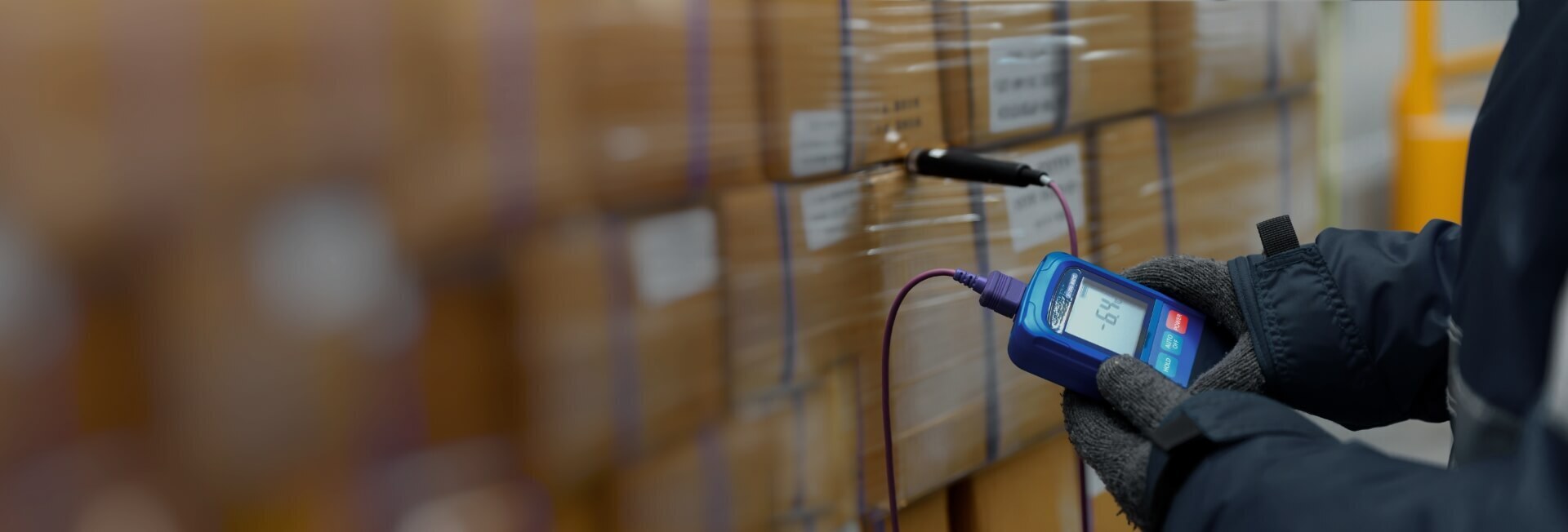
The role of process standardization in improving manufacturing efficiency
- Home
- Resources
- Cooling Unit Manufacturing Insights
- The role of process standardization in improving manufacturing efficiency
The Importance of Process Standardization in Manufacturing Efficiency
In today's highly competitive manufacturing landscape, efficiency is the key to success. Manufacturers constantly strive to optimize their operations, reduce costs, and improve productivity. One powerful tool that can significantly contribute to these goals is process standardization.
What is Process Standardization?
Process standardization refers to the establishment of consistent, repeatable procedures and practices across an organization. It involves documenting and streamlining processes to ensure that they are performed in a consistent manner, regardless of the location or personnel involved.
Standardization provides a framework for consistency and predictability, allowing manufacturers to achieve higher levels of efficiency, quality, and reliability. By defining best practices and implementing standardized processes, manufacturers can eliminate variations, reduce errors, and optimize resource utilization.
The Benefits of Process Standardization in Manufacturing Efficiency
Implementing process standardization can yield numerous benefits for manufacturers. Let's explore some of the key advantages:
1. Improved Quality Control
Standardizing manufacturing processes enables better control over product quality. By defining and implementing standardized procedures, manufacturers can minimize variations and deviations that may lead to defects or subpar quality. This ensures that each product meets the desired specifications, leading to increased customer satisfaction and loyalty.
2. Enhanced Productivity
Standardization eliminates unnecessary steps, rework, and duplication of efforts. It streamlines processes, reduces complexity, and enables employees to work more efficiently. With clearly defined procedures and guidelines, employees can complete their tasks with greater speed and accuracy. This leads to higher productivity levels and increased output.
3. Reduced Costs
Standardization helps manufacturers identify and eliminate inefficiencies in their processes. By streamlining operations and removing redundant activities, manufacturers can reduce waste, lower production costs, and optimize resource utilization. This leads to significant cost savings and improved profitability.
4. Faster Time-to-Market
Efficient and standardized processes enable manufacturers to bring products to market faster. By eliminating bottlenecks and delays, manufacturers can accelerate the entire production cycle, from design to delivery. This not only allows manufacturers to respond quickly to market demands but also gives them a competitive edge by being the first to introduce new products or innovations.
Implementing Process Standardization
While the benefits of process standardization are clear, implementing it effectively requires careful planning and execution. Here are some key steps to consider:
1. Process Analysis
The first step in implementing process standardization is to conduct a thorough analysis of existing processes. Identify areas of variation, inefficiency, and potential improvements. This analysis will serve as a foundation for developing standardized procedures.
2. Define Best Practices
Once the analysis is complete, it's important to define best practices and standardize procedures. This involves documenting step-by-step instructions, specifying process parameters, and establishing quality control measures. It's crucial to involve key stakeholders and subject matter experts in this process to ensure comprehensive and accurate documentation.
3. Training and Communication
Implementing process standardization requires effective training and communication. Ensure that all employees are trained on the standardized procedures and understand their roles and responsibilities. Regular communication and feedback channels should be established to address any questions or concerns and to ensure ongoing compliance with the standardized processes.
4. Continuous Improvement
Process standardization is not a one-time effort. It requires continuous monitoring and improvement. Regularly review the standardized procedures and seek feedback from employees to identify areas for further optimization. Embrace a culture of continuous improvement to drive ongoing efficiency gains and ensure that the standardized processes remain relevant and effective.
Case Study: Process Standardization in Cooling System Manufacturing
Let's take a closer look at how process standardization can improve manufacturing efficiency in the context of cooling system manufacturers.
Cooling technology plays a crucial role in various industries, including data centers, manufacturing plants, and commercial establishments. Cooling system manufacturers face the challenge of meeting the increasing demand for energy-efficient and environmentally friendly cooling solutions.
By implementing process standardization, cooling system manufacturers can achieve significant improvements in efficiency and sustainability. Let's explore some specific benefits:
1. Enhanced Energy Efficiency
Standardizing manufacturing processes allows cooling system manufacturers to optimize energy consumption. By defining and implementing standardized procedures, manufacturers can identify energy-saving opportunities, such as using energy-efficient components, optimizing cooling system design, and implementing intelligent control systems. This not only reduces energy costs but also contributes to a greener and more sustainable manufacturing process.
2. Improved Product Quality
Process standardization ensures consistent product quality across different cooling system units. By following standardized procedures, manufacturers can minimize variations that may lead to performance issues or premature failures. This enhances the reliability and durability of the cooling units, leading to increased customer satisfaction and reduced warranty claims.
3. Streamlined Production and Distribution
Standardization in cooling system manufacturing enables streamlined production and distribution processes. By implementing standardized procedures, manufacturers can eliminate bottlenecks, reduce lead times, and optimize inventory levels. This allows for faster order fulfillment and improved customer responsiveness.
4. Sustainable Cooling Solutions
Process standardization promotes the adoption of sustainable practices in cooling system manufacturing. By implementing standardized procedures, manufacturers can ensure the proper disposal of hazardous materials, minimize waste generation, and maximize the use of recyclable components. This contributes to a more eco-friendly manufacturing process and aligns with the growing demand for sustainable cooling solutions.
Conclusion
Process standardization plays a critical role in improving manufacturing efficiency. By establishing consistent and repeatable procedures, manufacturers can enhance quality control, boost productivity, reduce costs, and accelerate time-to-market. In the context of cooling system manufacturing, process standardization enables energy-efficient operations, improved product quality, streamlined production, and sustainable practices.
Manufacturers should embrace process standardization as a strategic initiative to drive continuous improvement and remain competitive in today's dynamic manufacturing landscape.
Related Blogs
The importance of education and awareness in promoting the adoption of green cooling technology
Read More