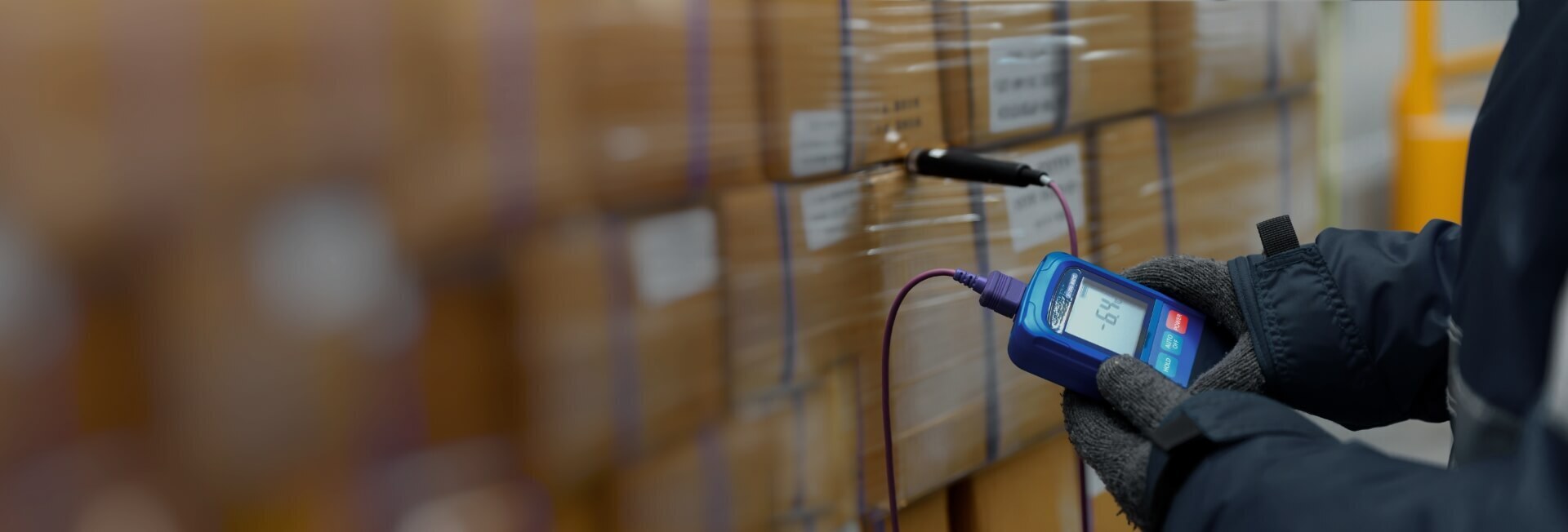
The role of process mapping in identifying bottlenecks and achieving streamlined manufacturing
- Home
- Resources
- Cooling Unit Manufacturing Insights
- The role of process mapping in identifying bottlenecks and achieving streamlined manufacturing
In today's competitive business landscape, manufacturing companies face numerous challenges in order to stay ahead. One of the key challenges is achieving streamlined manufacturing to improve efficiency, reduce costs, and increase productivity. To achieve this, manufacturers need to identify bottlenecks in their production processes and find ways to eliminate them. This is where process mapping comes into play.
What is Process Mapping?
Process mapping is a technique used to visually represent the steps involved in a particular process. It allows manufacturers to identify inefficiencies, bottlenecks, and areas for improvement. By mapping out the entire production process, manufacturers can gain a clear understanding of how each step contributes to the overall workflow.
The Benefits of Process Mapping in Manufacturing
Process mapping offers several key benefits for manufacturers looking to achieve streamlined operations:
1. Identifying Bottlenecks
One of the main advantages of process mapping is its ability to identify bottlenecks in the production process. Bottlenecks are areas where the flow of work is slowed down or disrupted, causing delays and inefficiencies. By mapping out each step of the process, manufacturers can easily identify these bottlenecks and take appropriate measures to eliminate them.
2. Improving Efficiency
Process mapping allows manufacturers to analyze each step of the production process in detail. This analysis helps identify areas where efficiency can be improved. By streamlining the workflow and eliminating unnecessary steps, manufacturers can significantly improve overall efficiency.
3. Reducing Costs
Inefficient processes often lead to increased costs. Process mapping helps identify areas where costs can be reduced by eliminating waste, reducing downtime, and optimizing resource allocation. By optimizing the production process, manufacturers can achieve cost savings without compromising on quality.
4. Enhancing Quality Control
Process mapping also plays a crucial role in enhancing quality control in manufacturing. By clearly defining each step of the process, manufacturers can implement quality checks at various stages to ensure that products meet the required standards. This helps reduce defects and rework, resulting in higher-quality products.
Process Mapping Techniques
There are several techniques that can be used to create process maps, including:
1. Flowcharts
Flowcharts are one of the most commonly used process mapping techniques. They use standard symbols and arrows to represent each step of the process and the flow of work. Flowcharts provide a visual representation of the entire process, making it easier to identify bottlenecks and areas for improvement.
2. Value Stream Mapping
Value stream mapping is a technique that focuses on mapping the flow of materials and information from the supplier to the customer. It helps identify waste and inefficiencies in the entire value stream, including production, distribution, and customer service. Value stream mapping provides a holistic view of the entire process, allowing manufacturers to identify opportunities for improvement.
3. Swimlane Diagrams
Swimlane diagrams are a type of flowchart that visually separates different departments or individuals involved in the process. This helps identify handoffs and delays between departments, making it easier to pinpoint bottlenecks and areas for improvement. Swimlane diagrams are particularly useful in complex manufacturing processes involving multiple stakeholders.
Implementing Process Mapping in Manufacturing
Implementing process mapping in manufacturing requires careful planning and execution. Here are some steps to follow:
1. Identify the Process to Map
The first step is to identify the specific process that needs to be mapped. It could be the entire production process or a specific sub-process. Clearly defining the scope of the process mapping exercise is crucial to ensure accuracy and effectiveness.
2. Gather Information
Collect all the relevant information about the process, including input materials, equipment used, and the sequence of steps involved. It's important to involve all stakeholders who are directly involved in the process to ensure comprehensive and accurate information gathering.
3. Create the Process Map
Using the chosen process mapping technique, create a visual representation of the process. Clearly label each step and include relevant details such as time taken, resources used, and any dependencies or handoffs between steps.
4. Analyze and Identify Areas for Improvement
Once the process map is created, analyze it to identify inefficiencies, bottlenecks, and areas for improvement. Look for steps that can be eliminated, combined, or automated to improve efficiency. Consider feedback from stakeholders and brainstorm ideas to optimize the process.
5. Implement Changes
Based on the analysis, implement the necessary changes to streamline the process. This may involve reorganizing the workflow, investing in new technology, or training employees on new processes. Regularly monitor and evaluate the impact of the changes to ensure their effectiveness.
Conclusion
Process mapping is a powerful tool that can help manufacturers identify bottlenecks, improve efficiency, reduce costs, and enhance quality control. By visually representing the production process, manufacturers can gain valuable insights and make informed decisions to achieve streamlined manufacturing. The implementation of process mapping techniques, such as flowcharts, value stream mapping, and swimlane diagrams, can significantly contribute to the success of manufacturing operations. Embracing process mapping as a continuous improvement practice can lead to sustainable and eco-friendly manufacturing processes that optimize resources and reduce waste.