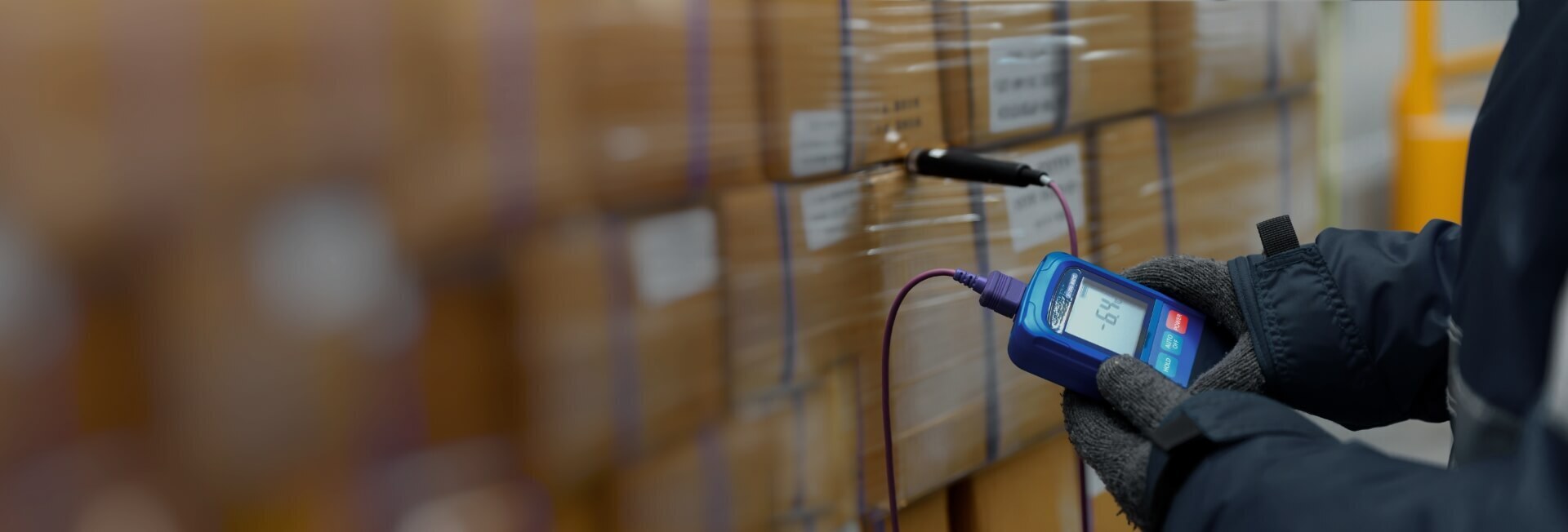
The role of predictive maintenance in optimizing energy efficiency in manufacturing equipment
- Home
- Resources
- Cooling Unit Manufacturing Insights
- The role of predictive maintenance in optimizing energy efficiency in manufacturing equipment
Predictive Maintenance: Optimizing Energy Efficiency in Manufacturing Equipment
Manufacturing industries are constantly seeking ways to improve their efficiency and reduce operational costs. One area that has gained significant attention in recent years is energy consumption. With rising energy costs and increasing environmental concerns, manufacturers are looking for ways to optimize their energy usage and reduce their carbon footprint.
The Importance of Energy-Efficiency in Manufacturing
Inefficient energy usage not only leads to higher operational costs but also contributes to environmental degradation. Manufacturing plants are known to be energy-intensive, consuming a significant amount of electricity and other resources. By adopting energy-efficient practices, manufacturers can not only reduce their operational costs but also contribute to a sustainable future.
The Role of Predictive Maintenance
Predictive maintenance plays a crucial role in optimizing energy efficiency in manufacturing equipment. Traditionally, maintenance activities in manufacturing plants were performed on a fixed schedule or based on the occurrence of breakdowns. This approach, known as reactive maintenance, often leads to unexpected downtime and higher energy consumption.
On the other hand, predictive maintenance involves the use of advanced technologies and data analysis to predict equipment failures and take proactive measures to prevent them. By monitoring the performance of manufacturing equipment in real-time, manufacturers can identify potential issues before they escalate into major problems. This allows for timely repairs or replacements, reducing the risk of unplanned downtime and improving energy efficiency.
The Benefits of Predictive Maintenance in Optimizing Energy Efficiency
Predictive maintenance offers several benefits when it comes to optimizing energy efficiency in manufacturing equipment:
1. Reduced Downtime
Unplanned downtime can be costly for manufacturers, both in terms of lost production time and increased energy consumption. By implementing predictive maintenance strategies, manufacturers can identify and address equipment issues before they cause unexpected breakdowns. This helps minimize downtime and ensures that manufacturing processes run smoothly, leading to improved energy efficiency.
2. Improved Equipment Performance
Predictive maintenance allows manufacturers to monitor the performance of their equipment in real-time. By analyzing data and identifying patterns, manufacturers can detect any deviations from normal operating conditions. This enables them to take proactive measures to optimize equipment performance and energy efficiency. For example, if a cooling system is not operating at peak efficiency, predictive maintenance can alert manufacturers to take corrective actions, such as cleaning the coils or replacing faulty components.
3. Extended Equipment Lifespan
Regular maintenance and timely repairs can significantly extend the lifespan of manufacturing equipment. By using predictive maintenance techniques, manufacturers can identify and address potential issues before they cause irreversible damage. This not only reduces the need for costly equipment replacements but also ensures that the equipment operates at optimal energy efficiency throughout its lifespan.
4. Cost Savings
Predictive maintenance helps manufacturers save costs in multiple ways. By reducing downtime, manufacturers can avoid the financial losses associated with lost production time. Additionally, by optimizing equipment performance and energy efficiency, manufacturers can reduce their energy consumption and lower their utility bills. Over time, these cost savings can add up and have a significant impact on the overall profitability of the manufacturing plant.
Implementing Predictive Maintenance Strategies
Implementing predictive maintenance strategies requires a combination of advanced technologies and data analysis capabilities. Here are some key steps involved in the implementation process:
1. Data Collection
The first step in implementing predictive maintenance is to collect relevant data from the manufacturing equipment. This can be done using various sensors and monitoring devices that capture real-time performance data. The data collected may include information such as temperature, vibration levels, power consumption, and other relevant parameters.
2. Data Analysis
Once the data is collected, it needs to be analyzed to identify any potential issues or anomalies. Advanced analytics techniques, such as machine learning algorithms, can be used to analyze the data and detect patterns that indicate impending equipment failures. This analysis helps manufacturers predict maintenance needs and take proactive measures to optimize energy efficiency.
3. Integration with Maintenance Systems
The insights gained from data analysis need to be integrated with the existing maintenance systems of the manufacturing plant. This ensures that the maintenance team receives timely alerts and notifications regarding potential equipment issues. By integrating predictive maintenance with maintenance systems, manufacturers can streamline their maintenance processes and ensure that necessary actions are taken in a timely manner.
4. Continuous Monitoring and Improvement
Predictive maintenance is an ongoing process that requires continuous monitoring and improvement. Manufacturers need to regularly review the performance data, analyze trends, and make adjustments to their maintenance strategies as needed. By continuously monitoring and improving their predictive maintenance practices, manufacturers can maximize their energy efficiency and optimize the overall performance of their manufacturing equipment.
Conclusion
Predictive maintenance plays a vital role in optimizing energy efficiency in manufacturing equipment. By adopting proactive maintenance strategies and leveraging advanced technologies, manufacturers can reduce downtime, improve equipment performance, extend equipment lifespan, and achieve significant cost savings. With the increasing focus on sustainability and energy conservation, predictive maintenance is becoming an essential practice for manufacturers aiming to streamline their operations and reduce their environmental impact.
Related Blogs
The importance of education and awareness in promoting the adoption of green cooling technology
Read More