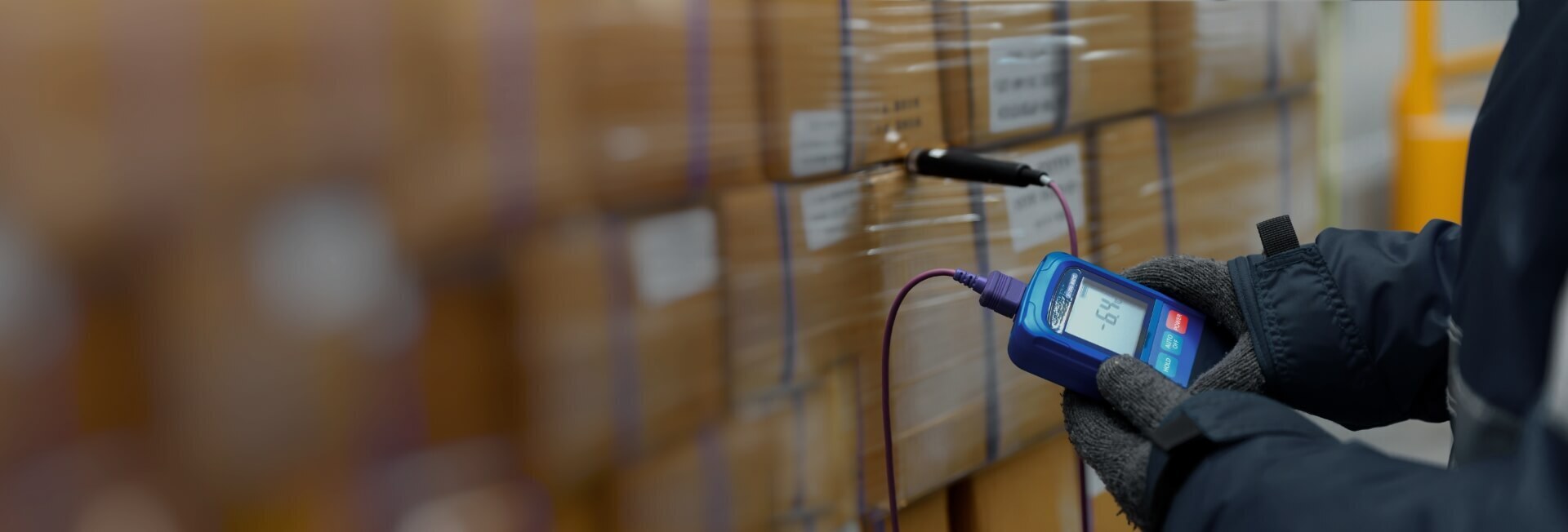
The role of predictive maintenance in achieving streamlined manufacturing
- Home
- Resources
- Cooling Unit Manufacturing Insights
- The role of predictive maintenance in achieving streamlined manufacturing
The Role of Predictive Maintenance in Achieving Streamlined Manufacturing
In today's fast-paced manufacturing industry, companies are constantly looking for ways to improve efficiency, reduce costs, and increase productivity. One of the key strategies being adopted by many manufacturers is predictive maintenance. This proactive approach to maintenance can help streamline manufacturing operations, minimize downtime, and optimize overall equipment effectiveness. In this article, we will explore the role of predictive maintenance in achieving streamlined manufacturing and the benefits it offers to businesses.
What is Predictive Maintenance?
Predictive maintenance is a method of maintenance that uses data analysis and machine learning algorithms to predict when equipment is likely to fail and take proactive measures to prevent such failures. It involves monitoring the condition of equipment in real-time, collecting data on various parameters such as temperature, vibration, and performance, and using this data to identify patterns and predict potential failures. By predicting maintenance needs in advance, manufacturers can schedule maintenance activities at the most opportune times, reducing unplanned downtime and improving overall equipment effectiveness.
The Benefits of Predictive Maintenance
Implementing predictive maintenance in manufacturing operations offers several significant benefits:
1. Increased Equipment Reliability and Availability
By continuously monitoring the condition of equipment and detecting potential issues in advance, predictive maintenance helps increase equipment reliability and availability. This means that manufacturers can avoid unexpected breakdowns and reduce downtime, ensuring that production schedules are met and customer orders are fulfilled on time.
2. Improved Efficiency and Productivity
Predictive maintenance allows manufacturers to optimize maintenance schedules and perform maintenance activities during planned downtime, minimizing the impact on production. This leads to improved efficiency and productivity as equipment is kept in optimal condition, reducing the likelihood of failures and maximizing uptime.
3. Cost Savings
By preventing unexpected breakdowns and reducing unplanned downtime, predictive maintenance helps manufacturers save on repair costs, replacement parts, and emergency maintenance. It also allows for better planning and allocation of maintenance resources, optimizing the use of manpower and reducing overall maintenance costs.
4. Enhanced Safety
Predictive maintenance helps identify potential safety hazards in equipment and allows for timely repairs or replacements before accidents occur. This helps create a safer working environment for employees and reduces the risk of injuries or accidents caused by equipment failures.
5. Data-Driven Decision Making
With predictive maintenance, manufacturers have access to real-time data and insights on the condition and performance of their equipment. This data can be used to make informed decisions about maintenance activities, equipment upgrades, and resource allocation, leading to more effective and efficient manufacturing operations.
Implementing Predictive Maintenance in Manufacturing
Implementing predictive maintenance in manufacturing requires a combination of technology, data analysis capabilities, and a proactive maintenance strategy. Here are some key steps involved in implementing predictive maintenance:
1. Data Collection and Monitoring
The first step in implementing predictive maintenance is to collect data on various parameters that can provide insights into the condition and performance of equipment. This can be done through sensors, IoT devices, or other data collection methods. The data collected should be monitored in real-time to identify any deviations or anomalies that may indicate potential failures.
2. Data Analysis and Predictive Modeling
Once the data is collected, it needs to be analyzed using advanced analytics and machine learning algorithms to identify patterns and predict potential failures. Predictive models can be developed based on historical data and used to forecast when equipment is likely to fail. These models can be continuously refined and updated as more data becomes available.
3. Alerting and Decision Making
When potential failures are predicted, alerts can be sent to maintenance teams or relevant personnel, notifying them of the impending maintenance needs. Based on these alerts, decisions can be made regarding the timing and type of maintenance activities required. This proactive approach allows for better planning and resource allocation.
4. Continuous Improvement
Predictive maintenance is an iterative process that requires continuous improvement and refinement. As more data is collected and analyzed, the predictive models can be improved, and the accuracy of predictions can be enhanced. Regular reviews and assessments should be conducted to identify areas for improvement and implement necessary changes.
The Future of Predictive Maintenance
As technology continues to advance, the future of predictive maintenance in manufacturing looks promising. Here are some trends that are likely to shape the future of predictive maintenance:
1. Artificial Intelligence and Machine Learning
Artificial intelligence and machine learning algorithms are becoming increasingly sophisticated and capable of analyzing large volumes of data in real-time. These technologies will play a crucial role in improving the accuracy and effectiveness of predictive maintenance models, enabling manufacturers to make more informed decisions and optimize maintenance activities.
2. Internet of Things (IoT)
The proliferation of IoT devices and sensors will enable manufacturers to collect more data on equipment performance and condition. This data can be used to further enhance predictive maintenance capabilities and provide manufacturers with real-time insights into the health of their equipment.
3. Predictive Analytics
Predictive analytics tools and platforms will continue to evolve, making it easier for manufacturers to collect, analyze, and interpret data for predictive maintenance purposes. These tools will provide more advanced visualization capabilities and predictive modeling techniques, allowing manufacturers to gain deeper insights into their equipment and make more accurate predictions.
Conclusion
Predictive maintenance is a powerful strategy that can help manufacturers achieve streamlined manufacturing operations, reduce downtime, and optimize overall equipment effectiveness. By implementing predictive maintenance, manufacturers can increase equipment reliability, improve efficiency and productivity, save costs, enhance safety, and make data-driven decisions. As technology continues to advance, the future of predictive maintenance looks even more promising, with artificial intelligence, machine learning, IoT, and predictive analytics playing key roles in further enhancing the capabilities and effectiveness of predictive maintenance in manufacturing.
Related Blogs
The importance of education and awareness in promoting the adoption of green cooling technology
Read More