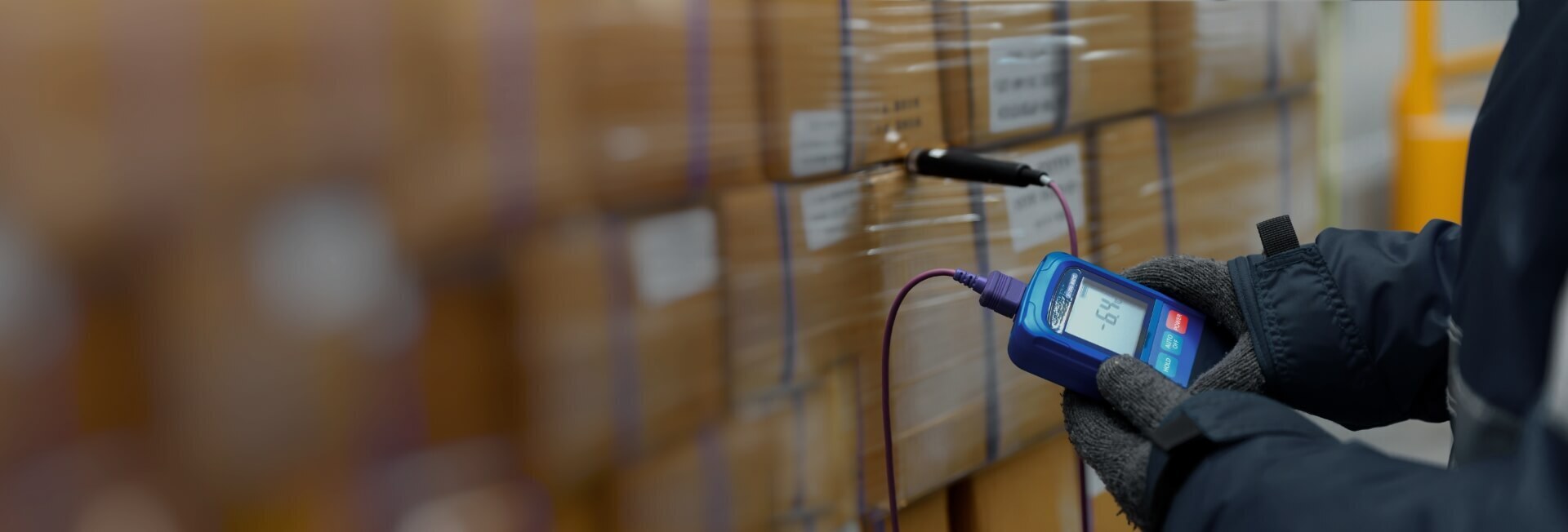
The role of performance metrics in measuring and improving manufacturing efficiency
- Home
- Resources
- Cooling Unit Manufacturing Insights
- The role of performance metrics in measuring and improving manufacturing efficiency
The Role of Performance Metrics in Measuring and Improving Manufacturing Efficiency
In today's competitive manufacturing landscape, it is essential for companies to continuously strive for better efficiency in order to stay ahead. One of the key tools in achieving this goal is the use of performance metrics. Performance metrics are quantifiable measures that can be used to evaluate the success or failure of a process or system. In the context of manufacturing, performance metrics are used to measure and improve efficiency, streamline operations, optimize supply chain, reduce energy consumption, and enhance sustainability. In this article, we will explore the importance of performance metrics in manufacturing efficiency and how they can help businesses achieve their goals.
Measuring Manufacturing Efficiency with Performance Metrics
Manufacturing efficiency can be defined as the ability to produce goods with minimum waste, cost, and time, while maximizing productivity and quality. Performance metrics provide a systematic way to measure and monitor various aspects of manufacturing efficiency. By tracking and analyzing these metrics, businesses can identify inefficiencies, bottlenecks, and areas for improvement. Let's take a look at some key performance metrics that are commonly used in the manufacturing industry:
1. Overall Equipment Efficiency (OEE)
Overall Equipment Efficiency (OEE) is a widely used performance metric that measures the effectiveness of manufacturing equipment. It takes into account three factors: availability, performance, and quality. Availability measures the percentage of time that the equipment is available for production. Performance measures the actual production rate compared to the ideal rate. Quality measures the percentage of good quality products produced. By calculating the OEE, businesses can identify equipment downtime, performance losses, and quality defects, and take necessary actions to improve efficiency.
2. Cycle Time
Cycle time is the total time it takes to complete a manufacturing process, from start to finish. It includes all the individual steps involved, such as setup time, processing time, and downtime. By measuring cycle time, businesses can identify bottlenecks and inefficiencies in their processes. Reducing cycle time can lead to increased productivity, faster time to market, and improved customer satisfaction.
3. First Pass Yield (FPY)
First Pass Yield (FPY) is a measure of the percentage of products that pass the quality check in the first attempt, without the need for rework or repair. A high FPY indicates good process control and high-quality standards. By monitoring FPY, businesses can identify quality issues, root causes of defects, and areas for improvement. Improving FPY can reduce waste, rework, and scrap, resulting in cost savings and improved efficiency.
4. Lead Time
Lead time is the total time it takes for a customer order to be fulfilled, from the time it is placed to the time it is delivered. It includes order processing time, manufacturing time, and transportation time. By measuring lead time, businesses can identify opportunities to reduce wait times, eliminate delays, and improve customer satisfaction. Shorter lead times can also help businesses respond faster to changing market demands and reduce inventory holding costs.
Improving Manufacturing Efficiency with Performance Metrics
Now that we understand the importance of performance metrics in measuring manufacturing efficiency, let's explore how they can be used to drive improvements:
1. Identifying and Addressing Bottlenecks
Performance metrics can help identify bottlenecks in the manufacturing process, such as equipment downtime, excessive setup time, or quality issues. By analyzing these metrics, businesses can pinpoint the root causes of inefficiencies and take corrective actions. For example, if a particular machine is consistently causing downtime, it may be necessary to invest in preventive maintenance or upgrade the equipment to improve reliability.
2. Optimizing Supply Chain
Performance metrics can also be used to optimize the supply chain, from raw material procurement to final product delivery. By tracking metrics such as supplier lead time, transportation costs, and on-time delivery performance, businesses can identify opportunities to streamline processes and reduce costs. For example, if a particular supplier consistently delays deliveries, it may be necessary to explore alternative suppliers or negotiate better terms.
3. Reducing Energy Consumption
Energy-efficiency is a key focus area for many manufacturing businesses, both from a cost-saving and sustainability perspective. Performance metrics can help monitor energy consumption at various stages of the manufacturing process, such as electricity usage by equipment, heating and cooling systems, and lighting. By analyzing these metrics, businesses can identify energy-intensive processes, implement energy-saving measures, and track the impact of these measures over time.
4. Enhancing Sustainability
Performance metrics can also play a crucial role in enhancing sustainability in the manufacturing industry. By tracking metrics related to waste generation, water usage, and greenhouse gas emissions, businesses can identify areas for improvement and set targets for reducing their environmental impact. For example, if a manufacturing facility generates a significant amount of waste, it may be necessary to implement recycling programs or explore alternative materials that generate less waste.
Conclusion
Performance metrics are powerful tools that can help businesses measure, monitor, and improve manufacturing efficiency. By tracking and analyzing metrics such as OEE, cycle time, FPY, and lead time, businesses can identify bottlenecks, optimize supply chain, reduce energy consumption, and enhance sustainability. The use of performance metrics not only helps businesses stay competitive in today's fast-paced manufacturing landscape but also contributes to a more efficient, sustainable, and environmentally friendly industry.
Related Blogs
The importance of education and awareness in promoting the adoption of green cooling technology
Read More