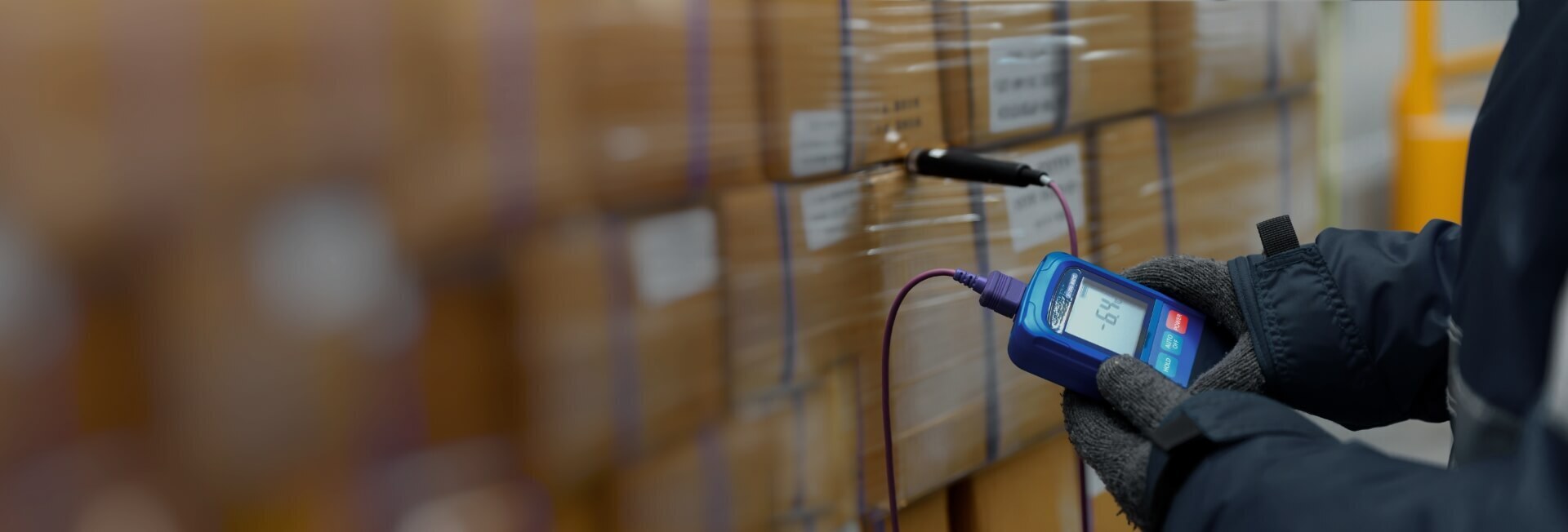
The role of lean manufacturing principles in driving energy efficiency
- Home
- Resources
- Cooling Unit Manufacturing Insights
- The role of lean manufacturing principles in driving energy efficiency
The Benefits of Lean Manufacturing for Energy Efficiency
Lean manufacturing principles have become increasingly important in today's industrial landscape. By eliminating waste and optimizing processes, lean manufacturing not only improves overall manufacturing efficiency but also plays a crucial role in driving energy efficiency. From reducing energy consumption to implementing sustainable cooling solutions, lean manufacturing can significantly contribute to creating a more environmentally friendly and sustainable manufacturing industry.
Supply Chain Optimization
One of the key aspects of lean manufacturing is supply chain optimization. By streamlining the supply chain, companies can reduce lead times, improve inventory management, and minimize waste. This optimization also extends to energy consumption. By analyzing and optimizing the energy usage throughout the supply chain, companies can identify areas of high energy consumption and implement energy-saving measures.
For example, by optimizing transportation routes and consolidating shipments, companies can reduce fuel consumption and greenhouse gas emissions. Additionally, by working closely with suppliers and implementing energy-efficient practices, manufacturers can ensure that the components and materials they receive are produced in an environmentally friendly manner.
Cooling Technology
Cooling technology plays a crucial role in many manufacturing processes, especially in industries such as food and beverage, pharmaceuticals, and electronics. Traditional cooling systems can be energy-intensive and contribute to a significant portion of a facility's overall energy consumption. However, by leveraging lean manufacturing principles, companies can adopt more energy-efficient cooling technologies.
Custom cooling solutions, such as precision cooling systems, can be designed to meet specific cooling requirements while minimizing energy consumption. These systems use advanced technologies such as variable speed compressors, intelligent controls, and heat recovery to optimize energy efficiency. By implementing these energy-efficient cooling systems, manufacturers can reduce their carbon footprint and lower energy costs.
Production and Distribution
Lean manufacturing focuses on eliminating waste and optimizing processes throughout the production and distribution cycle. By reducing waste, companies can minimize energy consumption and improve energy efficiency. This can be achieved through various lean manufacturing techniques such as just-in-time production, continuous improvement, and value stream mapping.
Just-in-time production, for example, aims to minimize inventory levels and reduce the energy required for storage and handling. By producing only what is needed, manufacturers can avoid excessive energy consumption associated with excess production and storage. Continuous improvement practices also play a significant role in energy efficiency by identifying and eliminating energy-wasting processes.
Commercial Cooling Units
Commercial cooling units are commonly used in various industries, including retail, hospitality, and healthcare. These units are responsible for maintaining optimal indoor temperatures and ensuring the comfort of employees and customers. However, traditional commercial cooling units can be energy-intensive and contribute to high energy bills.
By adopting lean manufacturing principles, companies can explore more energy-efficient alternatives for commercial cooling. For example, energy-efficient HVAC systems and smart thermostats can help regulate temperatures more effectively and minimize energy waste. Additionally, by implementing proper insulation and preventive maintenance practices, companies can further improve the energy efficiency of their commercial cooling units.
Sustainable Cooling Solutions
Lean manufacturing also encourages the adoption of sustainable cooling solutions, which not only reduce energy consumption but also minimize the environmental impact. Sustainable cooling solutions focus on utilizing renewable energy sources, optimizing cooling processes, and reducing refrigerant leakage.
For instance, companies can integrate solar-powered cooling systems into their manufacturing facilities. These systems harness the power of the sun to generate electricity for cooling purposes, reducing reliance on conventional energy sources. Additionally, by implementing advanced insulation techniques and optimizing airflow, manufacturers can reduce the load on cooling systems and improve energy efficiency.
Green Cooling Technology
Green cooling technology refers to the use of environmentally friendly cooling units that minimize energy consumption and reduce greenhouse gas emissions. These units often incorporate advanced technologies such as variable speed compressors, intelligent controls, and natural refrigerants.
By embracing lean manufacturing principles, companies can prioritize the adoption of green cooling technology. This includes replacing outdated cooling units with more energy-efficient alternatives and implementing proper maintenance practices to ensure optimal performance. Green cooling technology not only improves energy efficiency but also aligns with the company's sustainability goals and reduces its environmental footprint.
Conclusion
In conclusion, lean manufacturing principles play a vital role in driving energy efficiency in the manufacturing industry. By optimizing supply chains, adopting energy-efficient cooling technology, and implementing sustainable cooling solutions, companies can significantly reduce energy consumption and contribute to a more sustainable future. The adoption of lean manufacturing practices not only improves overall manufacturing efficiency but also aligns with the growing demand for environmentally friendly and energy-efficient solutions.
Related Blogs
The importance of education and awareness in promoting the adoption of green cooling technology
Read More