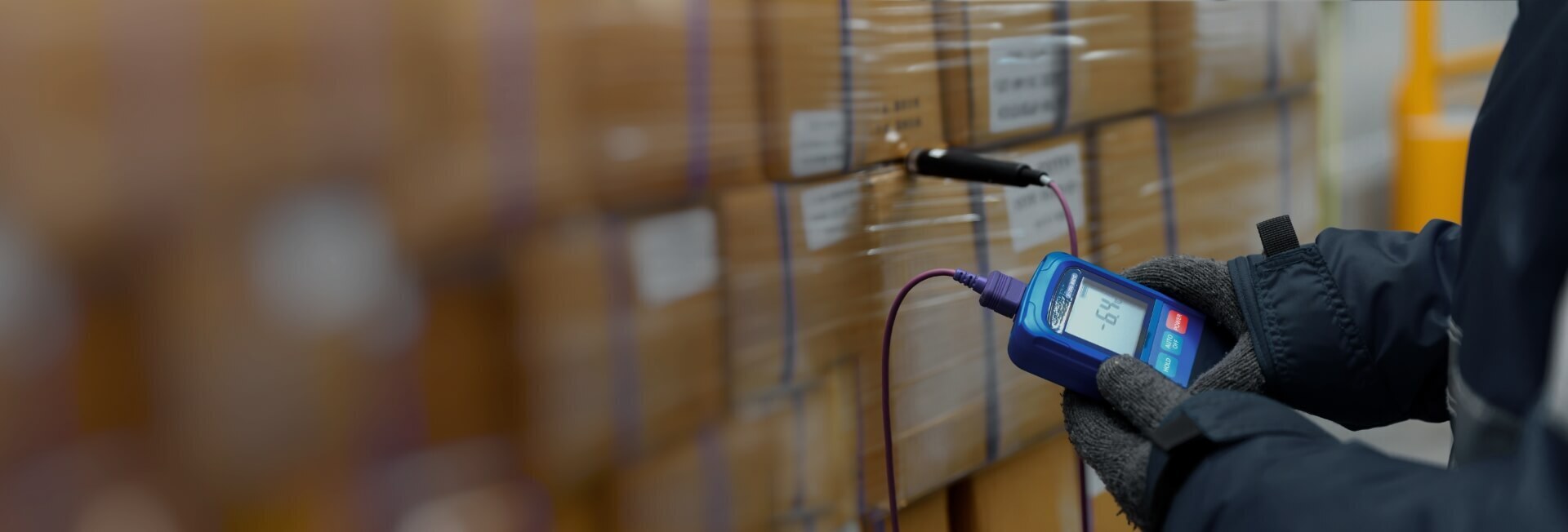
The role of lean manufacturing in improving efficiency
- Home
- Resources
- Cooling Unit Manufacturing Insights
- The role of lean manufacturing in improving efficiency
The Importance of Lean Manufacturing in Improving Efficiency
Efficiency is a critical factor in any manufacturing process. It directly impacts productivity, cost-effectiveness, and customer satisfaction. One approach that has gained significant traction in recent years is lean manufacturing. Lean manufacturing aims to eliminate waste, streamline processes, and optimize resource utilization to improve overall efficiency. This article will explore the role of lean manufacturing in improving efficiency and its various benefits for businesses.
Understanding Lean Manufacturing
Lean manufacturing, also known as lean production or simply lean, is a systematic approach to manufacturing that focuses on minimizing waste and maximizing value. It originated from the Toyota Production System (TPS) in the 1940s and has since been adopted by numerous industries worldwide.
At its core, lean manufacturing is about identifying and eliminating non-value-added activities or waste. These wastes can be categorized into seven types:
- Overproduction
- Waiting
- Transportation
- Overprocessing
- Inventory
- Motion
- Defects
By eliminating these wastes, lean manufacturing aims to create a more efficient and effective production system. It focuses on continuous improvement and employee empowerment, encouraging all members of the organization to contribute to the process optimization efforts.
The Benefits of Lean Manufacturing
Implementing lean manufacturing principles can yield numerous benefits for businesses. Let's explore some of the key advantages:
1. Increased Efficiency
Lean manufacturing helps identify and eliminate activities that do not add value to the production process. By reducing waste, companies can optimize their operations and achieve higher levels of efficiency. This leads to improved productivity and resource utilization, ultimately resulting in cost savings and higher profit margins.
2. Enhanced Quality
Lean manufacturing emphasizes the importance of quality control throughout the production process. By focusing on defect prevention rather than detection, businesses can significantly reduce the number of defective products. This results in higher customer satisfaction, fewer returns, and improved brand reputation.
3. Reduced Lead Times
Lean manufacturing aims to minimize lead times by eliminating non-value-added activities. By streamlining processes and reducing waste, companies can respond more quickly to customer demands and market changes. This agility is crucial in today's fast-paced business environment.
4. Improved Customer Satisfaction
Lean manufacturing aligns the production process with customer requirements. By eliminating waste and focusing on value-added activities, businesses can deliver products that meet customer expectations in terms of quality, cost, and delivery. This leads to higher customer satisfaction and loyalty.
Implementing Lean Manufacturing
Implementing lean manufacturing requires a systematic approach and commitment from all levels of the organization. Here are some key steps to consider:
1. Identify Areas of Waste
The first step in implementing lean manufacturing is identifying areas of waste in the production process. This can be done through value stream mapping, which involves analyzing each step in the production process and identifying non-value-added activities.
2. Set Clear Objectives
Once the areas of waste are identified, it is essential to set clear objectives for improvement. These objectives should be specific, measurable, achievable, relevant, and time-bound (SMART). By setting clear goals, businesses can track their progress and ensure continuous improvement.
3. Involve Employees
Employee involvement is crucial in lean manufacturing. Employees at all levels should be encouraged to contribute their ideas and suggestions for process improvement. By empowering employees and providing them with the necessary training and resources, businesses can create a culture of continuous improvement.
4. Implement Lean Tools and Techniques
There are various lean tools and techniques that can be used to improve efficiency, such as:
- Kanban system: A visual signaling system for inventory management
- 5S methodology: A system for organizing the workplace and improving efficiency
- Single-minute exchange of die (SMED): A technique for reducing setup and changeover time
- Poka-yoke: Mistake-proofing devices or mechanisms
- Just-in-time (JIT) production: A system for producing and delivering products in the exact quantity and at the exact time they are needed
Case Study: Lean Manufacturing in the Cooling System Industry
One industry that has successfully implemented lean manufacturing principles is the cooling system manufacturing industry. Cooling systems are essential for various applications, including data centers, commercial buildings, and industrial facilities. The demand for energy-efficient and environmentally friendly cooling solutions has been on the rise due to increasing environmental concerns and regulatory requirements.
Cooling system manufacturers have embraced lean manufacturing to optimize their production and distribution processes. By reducing waste and improving efficiency, they have been able to meet the growing demand for custom cooling solutions while minimizing their environmental impact.
1. Supply Chain Optimization
Lean manufacturing has enabled cooling system manufacturers to optimize their supply chains. By implementing just-in-time production and delivery systems, they can minimize inventory levels and reduce lead times. This not only improves efficiency but also reduces costs associated with inventory management and storage.
2. Energy Efficiency in Manufacturing
Lean manufacturing emphasizes energy efficiency throughout the production process. Cooling system manufacturers have incorporated energy-saving technologies into their production lines, such as advanced cooling technology and precision cooling systems. These technologies help reduce energy consumption and promote sustainability.
3. Sustainable Cooling Solutions
Environmental sustainability is a top priority for cooling system manufacturers. Lean manufacturing has enabled the development of environmentally friendly cooling units that use eco-friendly refrigerants and materials. These units are designed to minimize the environmental impact while providing efficient cooling solutions.
4. Streamlined Manufacturing
Lean manufacturing has streamlined the manufacturing processes of cooling system manufacturers. By eliminating waste, reducing setup times, and optimizing workflows, they have been able to increase production efficiency and meet customer demands more effectively.
Conclusion
Lean manufacturing plays a crucial role in improving efficiency and driving business success. By eliminating waste, streamlining processes, and optimizing resource utilization, companies can achieve higher levels of productivity, cost-effectiveness, and customer satisfaction. The implementation of lean manufacturing principles is a continuous journey that requires commitment and involvement from all levels of the organization. As seen in the cooling system manufacturing industry, lean manufacturing can bring significant benefits and help businesses stay competitive in today's rapidly changing business landscape.
Related Blogs
The importance of education and awareness in promoting the adoption of green cooling technology
Read More