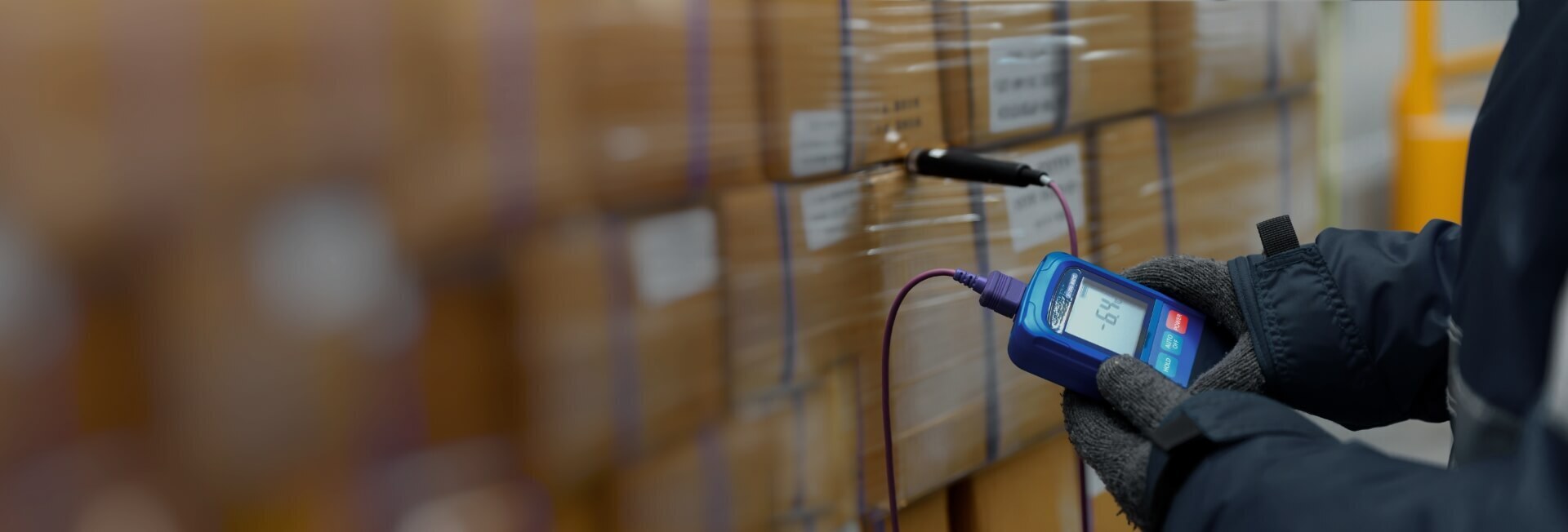
The role of error-proofing techniques in achieving streamlined manufacturing
- Home
- Resources
- Cooling Unit Manufacturing Insights
- The role of error-proofing techniques in achieving streamlined manufacturing
Manufacturing efficiency is crucial in today's competitive market. With supply chain optimization and streamlined processes becoming the norm, manufacturers are constantly looking for ways to enhance their operations. One key aspect of achieving streamlined manufacturing is the implementation of error-proofing techniques. These techniques not only help prevent errors and defects, but also improve overall efficiency and productivity. In this article, we will explore the role of error-proofing techniques in achieving streamlined manufacturing and the benefits they bring to the table.
The Need for Streamlined Manufacturing
Streamlined manufacturing refers to the process of optimizing production and distribution to eliminate waste, reduce costs, and improve overall efficiency. In today's fast-paced market, customers demand high-quality products delivered in a timely manner. To meet these demands, manufacturers need to ensure their operations are running smoothly and efficiently.
A streamlined manufacturing process allows for faster production cycles, reduced lead times, and improved customer satisfaction. It also helps manufacturers stay competitive by enabling them to deliver products at a lower cost, giving them an edge in the market. However, achieving streamlined manufacturing is not an easy task. It requires careful planning, efficient processes, and the right tools and techniques.
Error-Proofing Techniques: An Overview
Error-proofing techniques, also known as poka-yoke, are methods used to prevent errors and defects from occurring in the manufacturing process. These techniques aim to identify and eliminate potential sources of errors, minimizing the chances of mistakes and improving overall productivity and quality.
There are several error-proofing techniques that can be implemented in manufacturing, depending on the specific needs of the process. Some common techniques include:
1. Foolproof Design
Foolproof design involves creating products and processes in a way that makes it impossible or difficult for errors to occur. This can be achieved through the use of physical or visual cues, such as color-coding, shape differentiation, or sensors. By designing products and processes with foolproof features, manufacturers can reduce the likelihood of errors and improve overall efficiency.
2. Checklists and Standard Operating Procedures
Checklists and standard operating procedures (SOPs) are essential tools in error-proofing. By providing clear instructions and guidelines, manufacturers can ensure that each step of the manufacturing process is performed correctly. Checklists and SOPs also help in training new employees, reducing the chances of errors due to lack of knowledge or experience.
3. Error Detection and Feedback Systems
Error detection and feedback systems are critical in identifying and correcting errors in real-time. These systems can include sensors, cameras, or automated inspection tools that detect deviations from the desired specifications. By providing immediate feedback, manufacturers can quickly address errors and prevent them from escalating into larger issues.
4. Quality Control Measures
Implementing robust quality control measures is another important aspect of error-proofing. Quality control measures can include regular inspections, testing, and sampling to ensure that products meet the required standards. By catching and addressing defects early on, manufacturers can prevent further errors and improve overall product quality.
The Benefits of Error-Proofing Techniques
The implementation of error-proofing techniques in manufacturing brings several benefits to the table:
1. Improved Quality
By preventing errors and defects from occurring, error-proofing techniques significantly improve product quality. This, in turn, leads to higher customer satisfaction and increased brand reputation. Customers are more likely to trust and recommend products that consistently meet their expectations, enhancing the manufacturer's competitiveness in the market.
2. Increased Efficiency
Error-proofing techniques streamline the manufacturing process by eliminating wasted time and resources. By preventing errors, manufacturers can avoid rework, scrap, and downtime, resulting in increased productivity and efficiency. This allows manufacturers to produce more in less time, meet customer demands, and reduce costs.
3. Cost Savings
Implementing error-proofing techniques can lead to significant cost savings for manufacturers. By preventing errors and defects, manufacturers can avoid the costs associated with rework, scrap, warranty claims, and customer returns. Additionally, error-proofing techniques help optimize processes, reduce lead times, and minimize inventory, further reducing costs.
4. Enhanced Safety
Error-proofing techniques not only improve product quality and efficiency but also enhance workplace safety. By eliminating potential hazards and errors, manufacturers create a safer working environment for their employees. This reduces the risk of accidents, injuries, and costly legal liabilities.
5. Continuous Improvement
Implementing error-proofing techniques encourages a culture of continuous improvement within the manufacturing organization. By constantly analyzing processes, identifying potential errors, and implementing preventive measures, manufacturers can continuously enhance their operations. This leads to a cycle of continuous improvement, resulting in even greater efficiency and productivity over time.
Conclusion
Error-proofing techniques play a vital role in achieving streamlined manufacturing. By preventing errors and defects, these techniques improve product quality, increase efficiency, and reduce costs. They also contribute to workplace safety and foster a culture of continuous improvement. Manufacturers looking to enhance their operations and stay competitive in the market should consider implementing error-proofing techniques as part of their overall manufacturing strategy.
Related Blogs
The importance of education and awareness in promoting the adoption of green cooling technology
Read More