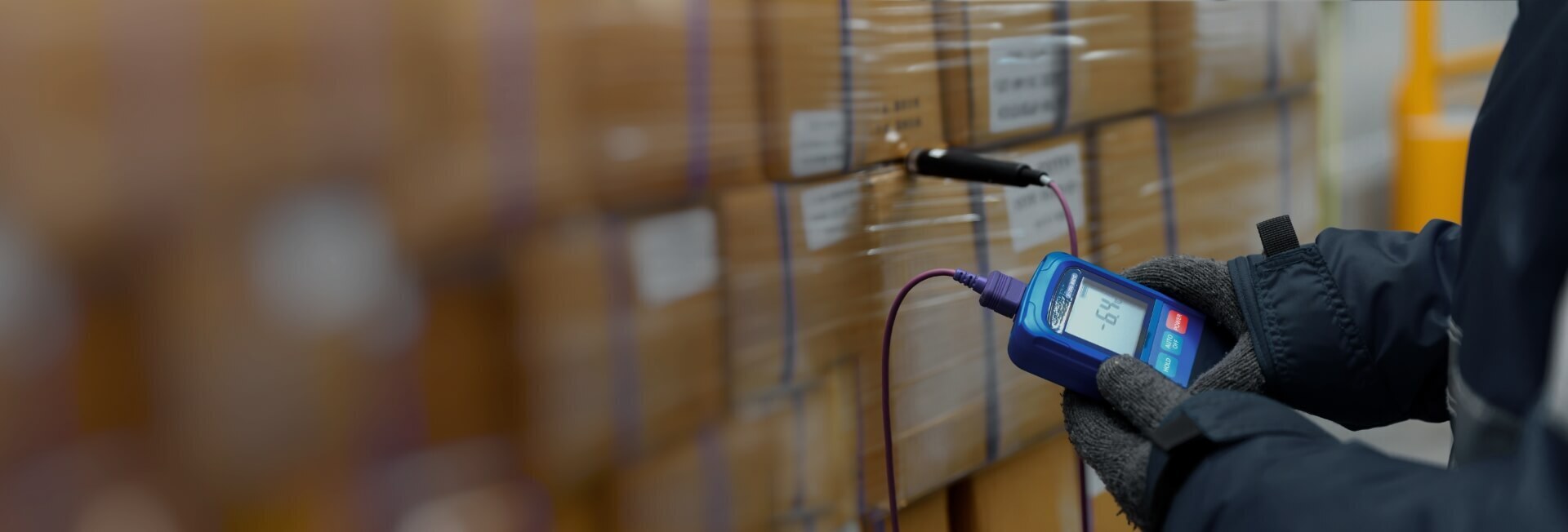
The role of energy audits in identifying areas for improvement in manufacturing facilities
- Home
- Resources
- Cooling Unit Manufacturing Insights
- The role of energy audits in identifying areas for improvement in manufacturing facilities
The Importance of Energy Audits in Manufacturing Facilities
Manufacturing facilities play a crucial role in the production and distribution of goods. However, they also consume a significant amount of energy, which can have a negative impact on the environment and the overall efficiency of the facility. To address this issue, many manufacturing facilities are turning to energy audits to identify areas for improvement and implement more sustainable practices. In this article, we will explore the role of energy audits in manufacturing facilities and the benefits they can provide.
What is an Energy Audit?
An energy audit is a systematic evaluation of a facility's energy use to identify areas where energy efficiency can be improved. It involves analyzing energy consumption patterns, evaluating equipment and systems, and recommending strategies to reduce energy consumption and costs. Energy audits are typically conducted by trained professionals who use specialized tools and techniques to gather data and assess the facility's energy performance.
The Benefits of Energy Audits in Manufacturing Facilities
Energy audits offer several benefits to manufacturing facilities, including:
1. Identification of Energy Efficiency Opportunities
One of the primary benefits of energy audits is the identification of energy efficiency opportunities. By conducting a thorough assessment of a facility's energy use, auditors can pinpoint areas where energy is being wasted or inefficiently used. This could include outdated equipment, inefficient processes, or system malfunctions. Once these opportunities are identified, facility managers can take steps to address them and improve overall energy efficiency.
2. Cost Savings
Implementing energy-efficient measures identified during an energy audit can result in significant cost savings for manufacturing facilities. By reducing energy consumption, facilities can lower their utility bills and operating costs. Additionally, energy-efficient equipment and systems often require less maintenance and have a longer lifespan, further reducing costs in the long run.
3. Environmental Benefits
Manufacturing facilities are known for their high energy consumption and greenhouse gas emissions. By implementing energy-efficient measures, facilities can significantly reduce their environmental impact. This includes reducing carbon dioxide emissions, air pollutants, and dependence on fossil fuels. Energy audits help manufacturing facilities identify areas for improvement and implement sustainable practices that contribute to a greener and more sustainable future.
4. Enhanced Reputation
Manufacturing facilities that prioritize energy efficiency and sustainability often enjoy an enhanced reputation among customers, investors, and the general public. Consumers are increasingly conscious of the environmental impact of the products they purchase, and companies that demonstrate a commitment to sustainability are more likely to attract and retain customers. Additionally, investors are increasingly interested in supporting companies that prioritize environmental responsibility, making energy audits a valuable tool for enhancing a facility's reputation and attracting investment.
The Energy Audit Process
The energy audit process typically involves the following steps:
1. Data Collection
The first step in an energy audit is gathering data about the facility's energy consumption. This includes collecting utility bills, evaluating equipment specifications, and assessing energy use patterns. This data provides a baseline for comparison and helps auditors identify areas for improvement.
2. Facility Assessment
Once the data is collected, auditors conduct a thorough assessment of the facility's equipment, systems, and processes. This involves inspecting equipment, evaluating maintenance practices, and identifying areas of energy waste. Auditors may also use specialized tools such as thermal imaging cameras to identify areas of heat loss or inefficiency.
3. Analysis and Recommendations
After the assessment, auditors analyze the data and identify potential energy efficiency measures. This may include upgrading equipment, improving insulation, optimizing processes, or implementing renewable energy technologies. Auditors then provide recommendations for implementing these measures and estimate the potential energy and cost savings.
4. Implementation and Monitoring
The final step in the energy audit process is implementing the recommended measures and monitoring their effectiveness. This may involve upgrading equipment, training staff on energy-efficient practices, or installing energy management systems. Ongoing monitoring allows facilities to track their energy consumption and identify further areas for improvement.
Conclusion
Energy audits play a crucial role in helping manufacturing facilities identify areas for improvement and implement more sustainable practices. By conducting a thorough assessment of a facility's energy use, auditors can identify energy efficiency opportunities, reduce costs, and minimize the environmental impact of manufacturing operations. Implementing the recommended measures not only benefits the facility but also enhances its reputation and attracts customers and investors. By prioritizing energy efficiency, manufacturing facilities can contribute to a greener and more sustainable future.
Related Blogs
The importance of education and awareness in promoting the adoption of green cooling technology
Read More