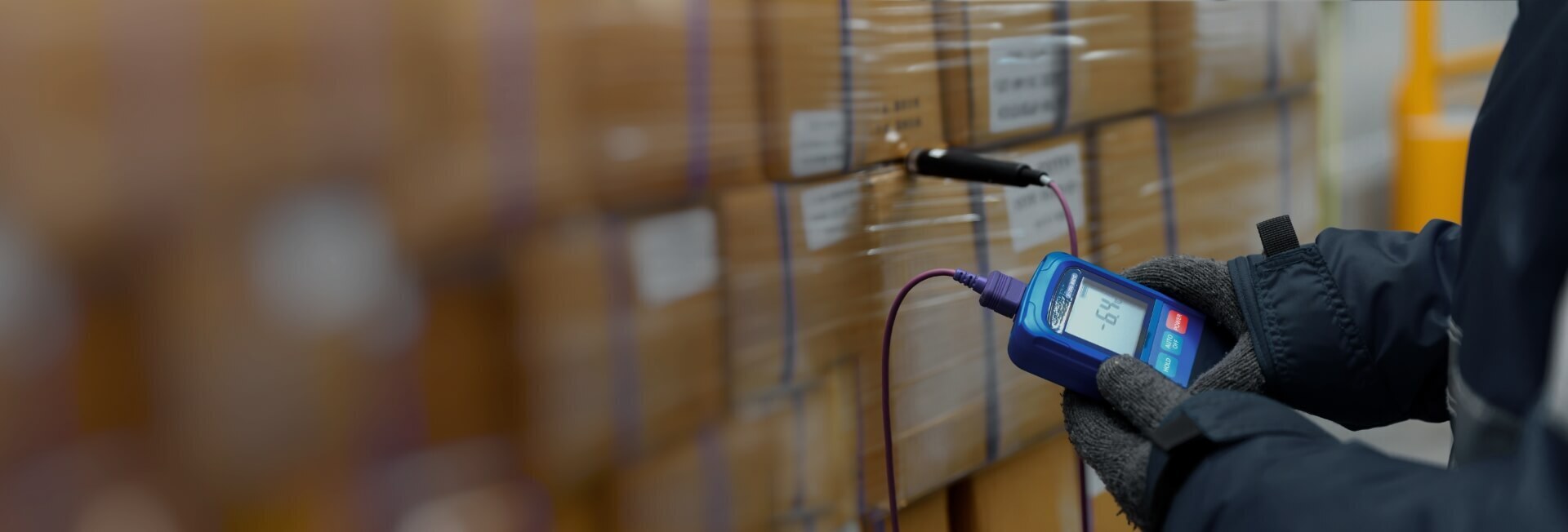
The role of cross-functional teams in driving manufacturing efficiency
- Home
- Resources
- Cooling Unit Manufacturing Insights
- The role of cross-functional teams in driving manufacturing efficiency
In today's competitive manufacturing landscape, cross-functional teams play a crucial role in driving efficiency and optimizing supply chain operations. The days of siloed departments working independently are long gone, as companies recognize the need for collaboration and communication across different functions to streamline processes and achieve sustainable growth.
What are Cross-Functional Teams?
Cross-functional teams are groups of individuals from different functional areas within an organization who come together to work on a specific project or goal. These teams are typically made up of members with diverse skill sets and expertise, including representatives from production, engineering, operations, supply chain, sales, and marketing.
The purpose of forming cross-functional teams is to leverage the collective knowledge and perspectives of individuals from different departments to solve complex problems and drive innovation. By bringing together experts from various functional areas, cross-functional teams can break down organizational silos and foster collaboration, leading to more effective decision-making and improved outcomes.
The Benefits of Cross-Functional Teams in Manufacturing
1. Enhanced Communication and Collaboration
One of the primary benefits of cross-functional teams in manufacturing is improved communication and collaboration. When individuals from different departments work together towards a common goal, it promotes open dialogue, knowledge sharing, and a better understanding of each other's perspectives. This leads to more effective problem-solving and decision-making, ultimately driving manufacturing efficiency.
2. Holistic Approach to Problem-Solving
Cross-functional teams bring together individuals with diverse skill sets and expertise, allowing for a holistic approach to problem-solving. By considering different viewpoints and leveraging the collective knowledge of team members, cross-functional teams can identify and address complex manufacturing issues more effectively. This comprehensive approach helps to uncover hidden inefficiencies, streamline processes, and optimize supply chain operations.
3. Faster Decision-Making
With cross-functional teams, decision-making becomes faster and more efficient. Instead of waiting for inputs and approvals from multiple departments, team members can collaborate in real-time to make informed decisions. This agility in decision-making is crucial in a fast-paced manufacturing environment, where delays can result in lost opportunities and increased costs.
4. Improved Quality Control
Cross-functional teams play a vital role in ensuring quality control in manufacturing. By involving representatives from production, engineering, and quality assurance, these teams can identify potential issues early on and implement corrective measures. This proactive approach to quality control helps to minimize defects and ensure that products meet the highest standards of quality.
Case Study: The Role of Cross-Functional Teams in Cooling System Manufacturers
One industry where cross-functional teams are particularly crucial is cooling system manufacturing. Cooling technology is an integral part of various industries, including data centers, manufacturing facilities, and commercial buildings. Custom cooling solutions are required to maintain optimal temperatures and ensure the efficient operation of equipment and processes.
Cooling system manufacturers rely on cross-functional teams to design, develop, and produce innovative and energy-efficient cooling units. These teams typically include engineers, designers, production specialists, supply chain experts, and sales representatives, among others.
By leveraging the diverse expertise of cross-functional teams, cooling system manufacturers can develop precision cooling systems that are tailored to the specific needs of their customers. These systems not only provide efficient cooling but also contribute to sustainability efforts by reducing energy consumption and environmental impact.
For example, a cross-functional team at a cooling system manufacturer collaborated to develop an eco-friendly cooling unit for a data center. The team included engineers specializing in energy-efficient design, production specialists with expertise in sustainable manufacturing processes, and supply chain experts who sourced environmentally friendly materials.
By working together, this cross-functional team was able to design a cooling unit that minimized energy consumption while maintaining precise temperature control. The unit incorporated advanced cooling technologies and utilized sustainable materials, making it a green cooling solution that aligned with the customer's sustainability goals.
Key Success Factors for Cross-Functional Teams
While cross-functional teams have numerous benefits, their success relies on certain key factors:
1. Clear Goals and Objectives
For cross-functional teams to be effective, it is essential to establish clear goals and objectives from the outset. This ensures that all team members are aligned and working towards a common purpose. Clear goals also help to measure the success of the team and track progress throughout the project.
2. Effective Communication
Open and effective communication is critical for the success of cross-functional teams. Team members must be able to share information, ideas, and feedback freely. Regular team meetings, project updates, and clear channels of communication help to foster collaboration and ensure that everyone is on the same page.
3. Strong Leadership
Cross-functional teams require strong leadership to guide and facilitate the collaboration process. A leader who can effectively manage conflicts, delegate tasks, and motivate team members is essential for driving manufacturing efficiency. Strong leadership also helps to keep the team focused and accountable for their deliverables.
4. Trust and Respect
Building trust and mutual respect among team members is crucial for cross-functional teams. When individuals feel valued and respected for their contributions, they are more likely to collaborate effectively and share their expertise. Trust also promotes open and honest communication, enabling teams to address challenges and make decisions collectively.
Conclusion
In today's complex manufacturing landscape, cross-functional teams are instrumental in driving efficiency and optimizing supply chain operations. By leveraging the diverse expertise and perspectives of individuals from different functional areas, these teams foster collaboration, enhance problem-solving capabilities, and improve decision-making.
For cooling system manufacturers and other industries, cross-functional teams play a vital role in developing innovative and sustainable solutions. By working together, these teams can design precision cooling systems that not only meet customers' specific needs but also contribute to energy efficiency and environmental sustainability.
To stay competitive and achieve sustainable growth, manufacturing companies must recognize the importance of cross-functional teams and invest in creating a collaborative and inclusive culture. By breaking down silos and promoting collaboration, these companies can drive manufacturing efficiency and stay ahead in a rapidly evolving market.
Related Blogs
The importance of education and awareness in promoting the adoption of green cooling technology
Read More