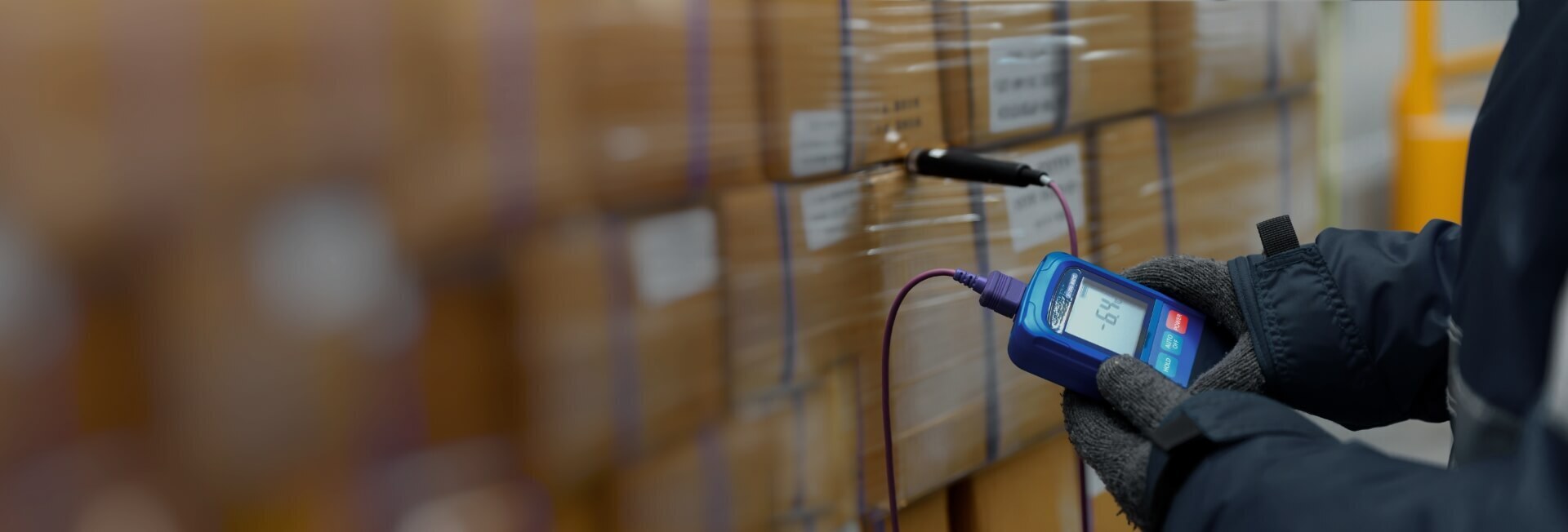
The role of continuous improvement culture in driving manufacturing efficiency
- Home
- Resources
- Cooling Unit Manufacturing Insights
- The role of continuous improvement culture in driving manufacturing efficiency
The Role of Continuous Improvement Culture in Driving Manufacturing Efficiency
In today's highly competitive manufacturing landscape, companies are constantly seeking ways to improve their operations, increase efficiency, and reduce costs. One of the key strategies that successful companies employ is the establishment of a continuous improvement culture.
What is Continuous Improvement Culture?
Continuous improvement culture refers to an organizational mindset and approach that embraces the constant pursuit of better ways to do things. It involves the systematic identification and elimination of waste, inefficiencies, and bottlenecks in all aspects of the manufacturing process. By fostering a culture of continuous improvement, companies can drive manufacturing efficiency and achieve sustainable growth.
The Benefits of Continuous Improvement Culture in Manufacturing
Implementing a continuous improvement culture in manufacturing can yield numerous benefits for companies. Let's explore some of the key advantages:
1. Increased Efficiency and Productivity
By continuously analyzing and optimizing the manufacturing process, companies can identify and eliminate inefficiencies that hinder productivity. This can involve streamlining workflows, reducing downtime, improving equipment maintenance practices, and implementing automation technologies. As a result, companies can achieve higher production output with the same or fewer resources, leading to improved efficiency and productivity.
2. Cost Savings and Waste Reduction
Continuous improvement culture focuses on identifying and eliminating waste in all forms, including time, materials, and resources. By minimizing waste, companies can reduce costs associated with excess inventory, rework, scrap, and inefficient processes. This not only leads to immediate cost savings but also helps in creating a more sustainable and environmentally friendly manufacturing operation.
3. Quality Improvement
Continuous improvement culture emphasizes the importance of quality throughout the manufacturing process. By implementing quality control measures and fostering a culture of accountability, companies can detect and address quality issues at an early stage, reducing the risk of defects and customer complaints. Improved quality not only enhances customer satisfaction but also reduces rework and warranty costs.
4. Employee Engagement and Empowerment
A continuous improvement culture encourages employees at all levels to actively participate in identifying and implementing process improvements. This not only fosters a sense of ownership and empowerment but also taps into the collective knowledge and expertise of the workforce. Engaged employees are more likely to contribute innovative ideas, take ownership of their work, and strive for excellence, leading to a more efficient and productive manufacturing operation.
Examples of Continuous Improvement Techniques in Manufacturing
There are several continuous improvement techniques that companies can implement to drive manufacturing efficiency. Let's take a look at some examples:
1. Lean Manufacturing
Lean manufacturing is a systematic approach to identifying and eliminating waste in the manufacturing process. It focuses on creating value for the customer while minimizing non-value-added activities. Lean principles, such as just-in-time production, standardized work, and continuous flow, help optimize workflows, reduce inventory, and improve overall efficiency.
2. Six Sigma
Six Sigma is a data-driven approach to process improvement that aims to reduce defects and variation. It utilizes statistical analysis and measurement tools to identify and eliminate the root causes of problems. By implementing Six Sigma methodologies, companies can improve process stability, reduce defects, and enhance overall quality.
3. Total Productive Maintenance (TPM)
Total Productive Maintenance (TPM) is a holistic approach to equipment maintenance that aims to maximize machine availability, performance, and quality. By involving all employees in the maintenance process and implementing proactive maintenance practices, companies can minimize equipment breakdowns, reduce downtime, and improve overall equipment effectiveness.
4. Kaizen
Kaizen, which means "continuous improvement" in Japanese, is a philosophy that encourages small, incremental improvements on a daily basis. It involves empowering employees to identify and implement improvements in their own work areas. By fostering a culture of kaizen, companies can drive continuous improvement at all levels of the organization and create a more efficient and agile manufacturing operation.
Conclusion
A continuous improvement culture is a powerful driver of manufacturing efficiency. By embracing the principles of continuous improvement, companies can increase efficiency, reduce costs, improve quality, and engage employees in the pursuit of excellence. The implementation of continuous improvement techniques, such as lean manufacturing, Six Sigma, TPM, and kaizen, can further enhance manufacturing efficiency and drive sustainable growth.
Manufacturing companies that prioritize continuous improvement culture are well-positioned to optimize their supply chain, streamline production and distribution, and deliver high-quality products to their customers. By investing in energy-efficient and environmentally friendly cooling technology, such as commercial cooling units, industrial cooling units, and precision cooling systems, companies can further enhance their manufacturing efficiency while reducing their environmental footprint.
When selecting cooling system manufacturers, it is important to choose those that offer custom cooling solutions tailored to the specific needs and requirements of the manufacturing facility. Sustainable cooling solutions, including eco-friendly cooling units and green cooling technology, can help companies achieve their energy-efficiency and sustainability goals.
In conclusion, continuous improvement culture plays a crucial role in driving manufacturing efficiency. By fostering a culture of continuous improvement, companies can achieve higher efficiency, reduce costs, improve quality, and engage employees in the pursuit of excellence. The implementation of continuous improvement techniques, such as lean manufacturing, Six Sigma, TPM, and kaizen, can further enhance manufacturing efficiency and drive sustainable growth. By investing in energy-efficient and environmentally friendly cooling technology, companies can optimize their manufacturing operations and contribute to a more sustainable future.
Related Blogs
The importance of education and awareness in promoting the adoption of green cooling technology
Read More