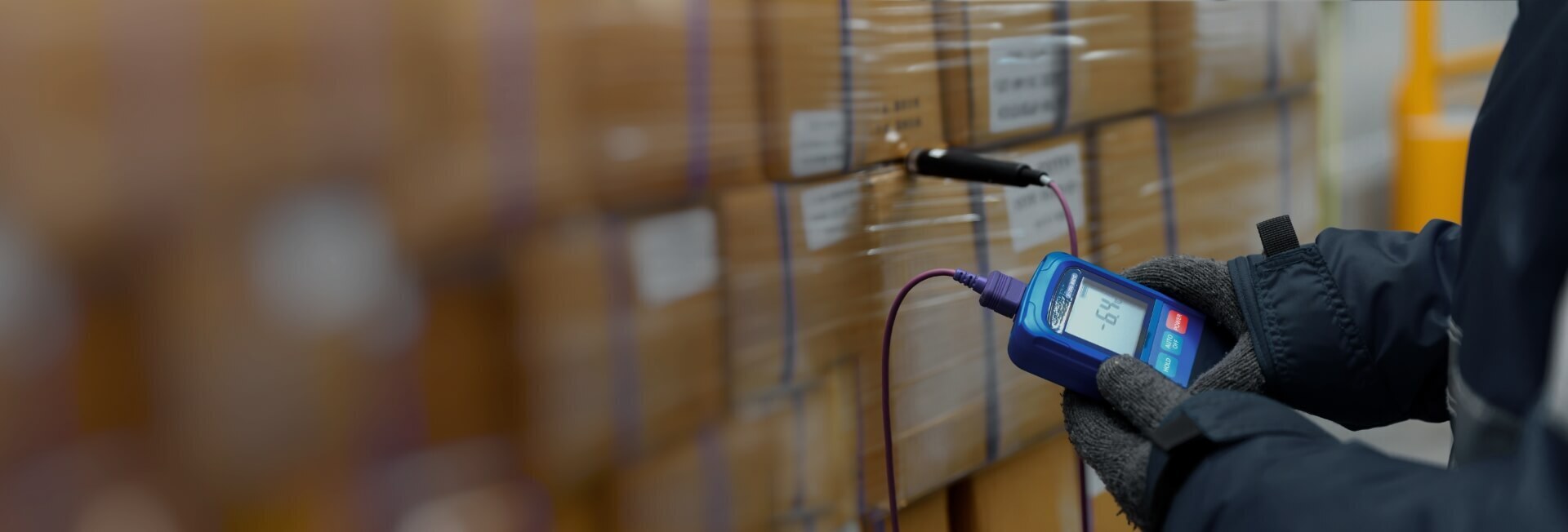
The role of continuous flow production in improving manufacturing efficiency
- Home
- Resources
- Cooling Unit Manufacturing Insights
- The role of continuous flow production in improving manufacturing efficiency
The Benefits of Continuous Flow Production in Manufacturing Efficiency
In today's competitive business landscape, manufacturing efficiency is crucial for companies to stay ahead and meet customer demands. One method that has proven to be highly effective in improving manufacturing efficiency is continuous flow production. By implementing this production method, companies can streamline their manufacturing processes, reduce waste, increase productivity, and ultimately enhance their overall competitiveness in the market.
What is Continuous Flow Production?
Continuous flow production, also known as continuous manufacturing or mass production, is a manufacturing method that focuses on producing goods in a continuous and uninterrupted manner. Unlike batch production, where goods are produced in separate batches, continuous flow production involves a continuous flow of materials and components through the production line.
Continuous flow production relies on a highly efficient and automated production line that is designed to minimize downtime and maximize output. It is commonly used in industries such as automotive manufacturing, electronics production, and food processing, where high volumes of products need to be produced quickly and consistently.
The Advantages of Continuous Flow Production
Implementing continuous flow production offers several advantages for companies looking to improve their manufacturing efficiency:
1. Increased Productivity
Continuous flow production allows for a higher level of productivity compared to other production methods. With a continuous flow of materials and components, there is minimal downtime between production cycles, resulting in a higher output of finished goods. This increased productivity can help companies meet customer demand more effectively and reduce lead times.
2. Waste Reduction
Continuous flow production also helps reduce waste in the manufacturing process. By streamlining the production line and eliminating unnecessary steps, companies can minimize the amount of scrap, rework, and defects in their products. This not only saves costs but also improves the overall quality of the goods produced.
3. Cost Efficiency
By reducing waste and increasing productivity, continuous flow production can lead to significant cost savings for companies. The streamlined production process requires fewer resources, such as labor and materials, resulting in lower production costs. Additionally, the reduced lead times and improved quality can also lead to cost savings in terms of customer satisfaction and retention.
4. Flexibility and Adaptability
Contrary to popular belief, continuous flow production does not mean sacrificing flexibility and adaptability. In fact, with the right setup and equipment, companies can achieve a high level of flexibility in their production line. Continuous flow production allows for quick changeovers between different products or variants, enabling companies to respond rapidly to changing market demands and customer preferences.
Implementing Continuous Flow Production
Implementing continuous flow production requires careful planning and investment in the right equipment and technology. Here are some key considerations for companies looking to adopt this production method:
1. Supply Chain Optimization
Supply chain optimization is crucial for the success of continuous flow production. Companies need to ensure a smooth and uninterrupted flow of materials, components, and information throughout the production process. This may involve working closely with suppliers and implementing just-in-time (JIT) inventory management to minimize inventory holding costs and reduce lead times.
2. Automation and Robotics
Automation and robotics play a significant role in continuous flow production. Companies need to invest in advanced manufacturing technologies, such as robotic arms and automated conveyor systems, to achieve a high level of efficiency and productivity. These technologies can handle repetitive tasks, reduce human error, and improve overall process control.
3. Cooling Technology
Cooling technology is essential in many manufacturing processes, especially those involving high temperatures or sensitive components. Companies should invest in commercial cooling units or custom cooling solutions to ensure optimal performance and prevent equipment failure. Choosing energy-efficient and environmentally friendly cooling systems can also contribute to sustainable manufacturing practices.
4. Continuous Improvement
Continuous flow production is not a one-time implementation but an ongoing journey of continuous improvement. Companies should regularly monitor and analyze their production processes, identify bottlenecks and areas for improvement, and implement appropriate changes. By embracing a culture of continuous improvement, companies can further enhance their manufacturing efficiency over time.
Conclusion
Continuous flow production is a highly effective method for improving manufacturing efficiency. By implementing this production method, companies can increase productivity, reduce waste, achieve cost efficiency, and enhance flexibility and adaptability. However, successful implementation requires careful planning, investment in the right equipment and technology, and a commitment to continuous improvement. With the right strategies in place, companies can reap the benefits of continuous flow production and gain a competitive edge in the market.
Related Blogs
The importance of education and awareness in promoting the adoption of green cooling technology
Read More