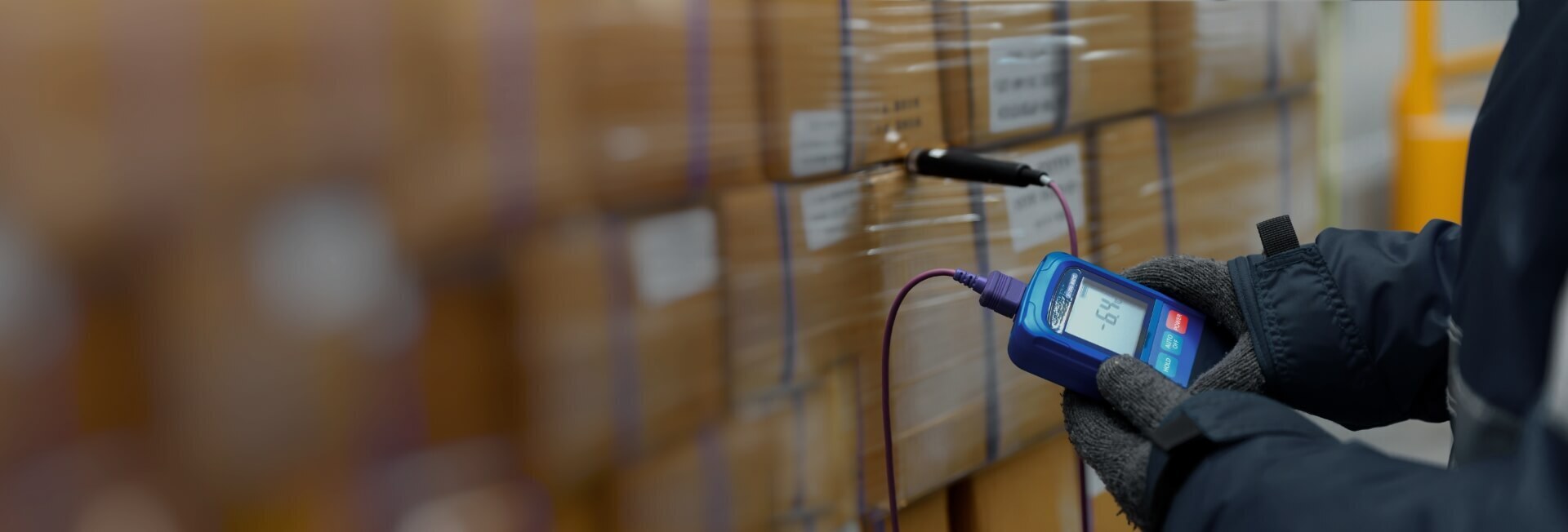
The potential of waste heat recovery systems in improving energy efficiency in manufacturing
- Home
- Resources
- Cooling Unit Manufacturing Insights
- The potential of waste heat recovery systems in improving energy efficiency in manufacturing
The Potential of Waste Heat Recovery Systems in Improving Energy Efficiency in Manufacturing
Manufacturing industries play a significant role in our economy, but they also consume a large amount of energy. It is estimated that manufacturing accounts for nearly 30% of global energy consumption. With increasing concerns about climate change and the need to reduce greenhouse gas emissions, it is crucial for manufacturers to find ways to improve their energy efficiency and minimize their environmental impact. One promising solution is the use of waste heat recovery systems.
What are Waste Heat Recovery Systems?
Waste heat recovery systems are technologies that capture and reuse the heat generated during various industrial processes. In manufacturing, a significant amount of heat is wasted through exhaust gases, cooling water, and other sources. Waste heat recovery systems are designed to capture this heat and convert it into usable energy, such as electricity or heat for other industrial processes.
These systems can be implemented in a wide range of industries, including steel, cement, chemical, and food processing. They can be integrated into existing manufacturing processes or installed as standalone systems. The captured heat can be used to generate electricity, preheat combustion air, heat water, or power other manufacturing processes. By utilizing waste heat, manufacturers can significantly reduce their energy consumption and greenhouse gas emissions.
The Benefits of Waste Heat Recovery Systems
Implementing waste heat recovery systems in manufacturing offers several benefits, both for the environment and for businesses:
1. Improved Energy Efficiency
By capturing and reusing waste heat, manufacturing facilities can significantly improve their energy efficiency. Waste heat recovery systems can convert wasted heat into usable energy, reducing the need for additional energy sources. This not only reduces energy costs but also lowers greenhouse gas emissions associated with energy production.
2. Cost Savings
Waste heat recovery systems can help manufacturers reduce their energy costs. By utilizing waste heat instead of relying solely on traditional energy sources, businesses can lower their energy consumption and, in turn, reduce their energy bills. Additionally, some governments offer incentives and grants to encourage the adoption of energy-efficient technologies, further reducing the financial burden of implementing waste heat recovery systems.
3. Environmental Benefits
One of the most significant advantages of waste heat recovery systems is their positive impact on the environment. By reducing energy consumption and greenhouse gas emissions, these systems help combat climate change and contribute to a more sustainable future. Implementing energy-efficient technologies is also an essential step towards achieving global environmental targets and reducing the carbon footprint of manufacturing industries.
4. Increased Competitiveness
Manufacturers that prioritize energy efficiency and sustainability are more likely to attract environmentally conscious customers and investors. By implementing waste heat recovery systems, businesses can demonstrate their commitment to reducing their environmental impact and operating in a more sustainable manner. This can enhance their reputation, increase brand value, and ultimately improve their competitiveness in the market.
The Challenges of Implementing Waste Heat Recovery Systems
While waste heat recovery systems offer significant benefits, there are also challenges associated with their implementation:
1. Technical Complexity
Integrating waste heat recovery systems into existing manufacturing processes can be technically complex. Each facility has unique requirements and limitations, making it necessary to design custom solutions for each case. This technical complexity can increase the initial costs and require specialized expertise for installation and maintenance.
2. Cost Considerations
The cost of implementing waste heat recovery systems can be a barrier for some manufacturers. The initial investment required for equipment and installation may be substantial, and the return on investment may take several years. However, it is essential to consider the long-term cost savings and potential incentives available to offset the initial expenses.
3. Operational Considerations
Integrating waste heat recovery systems into manufacturing processes requires careful planning and consideration. The implementation process may disrupt operations, and adjustments may need to be made to accommodate the new system. Additionally, ongoing maintenance and monitoring are necessary to ensure the efficient operation of the waste heat recovery systems.
The Future of Waste Heat Recovery Systems
As the demand for energy-efficient and sustainable manufacturing practices continues to grow, waste heat recovery systems are expected to play an increasingly important role. Advancements in technology and increased awareness of environmental issues are driving the development of more efficient and cost-effective waste heat recovery solutions.
Manufacturers are also exploring innovative ways to utilize waste heat, such as integrating it into district heating systems or leveraging it for onsite power generation. Research and development efforts are focused on improving the efficiency of waste heat recovery systems, reducing their costs, and making them more adaptable to different manufacturing processes.
Additionally, governments and regulatory bodies are recognizing the importance of energy efficiency in manufacturing and are implementing policies and incentives to encourage the adoption of waste heat recovery systems. These initiatives aim to accelerate the transition towards more sustainable manufacturing practices and support the development of a circular economy.
Conclusion
Waste heat recovery systems have the potential to significantly improve energy efficiency in manufacturing and contribute to a more sustainable future. By capturing and reusing waste heat, manufacturers can reduce their energy consumption, lower their greenhouse gas emissions, and save on energy costs. While there are challenges associated with implementing these systems, advancements in technology and supportive policies are making waste heat recovery increasingly viable.
As manufacturers continue to prioritize energy efficiency and sustainability, waste heat recovery systems will become an integral part of their operations. By embracing these technologies, businesses can streamline their manufacturing processes, reduce their environmental impact, and gain a competitive edge in the market.
Related Blogs
The importance of education and awareness in promoting the adoption of green cooling technology
Read More