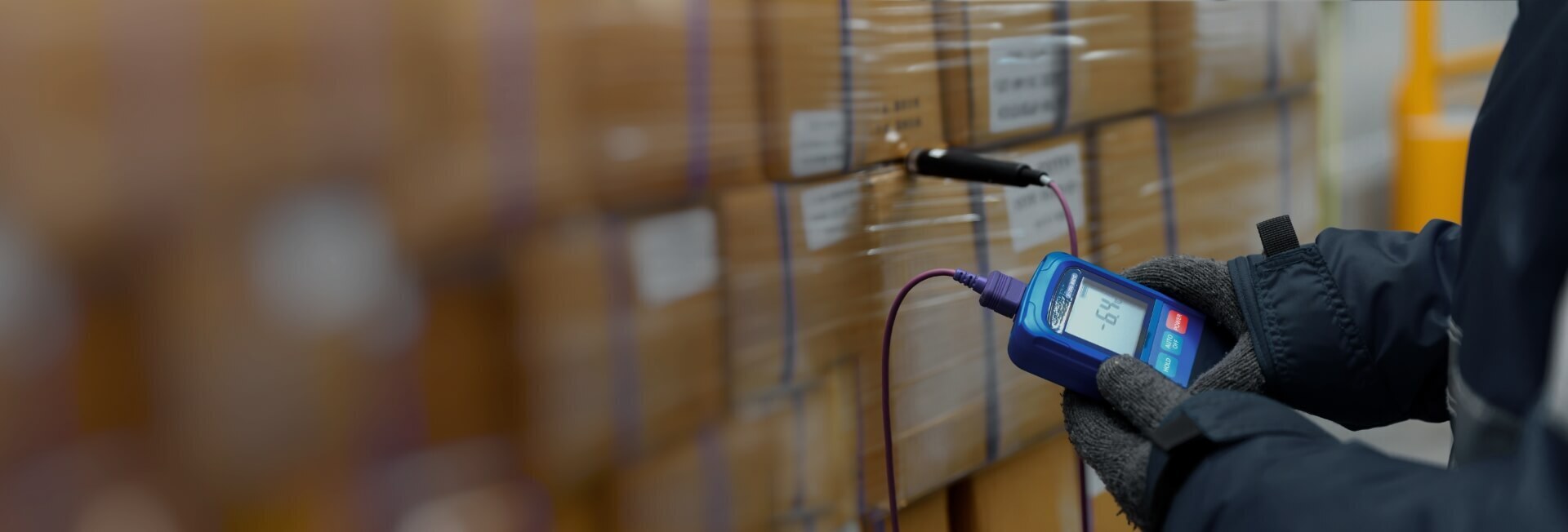
The importance of regular maintenance and proper insulation in maximizing cooling efficiency
- Home
- Resources
- Cooling Unit Manufacturing Insights
- The importance of regular maintenance and proper insulation in maximizing cooling efficiency
The Importance of Regular Maintenance and Proper Insulation in Maximizing Cooling Efficiency
When it comes to manufacturing and commercial cooling units, the efficiency of the cooling system plays a crucial role in both the production process and the distribution of goods. Cooling technology is essential for maintaining optimal temperatures in various industrial settings, such as factories, warehouses, and distribution centers. However, without regular maintenance and proper insulation, the cooling system's efficiency can be compromised, leading to increased energy consumption, higher costs, and reduced productivity. In this article, we will explore the importance of regular maintenance and proper insulation in maximizing cooling efficiency and discuss how these practices can contribute to sustainable and energy-efficient manufacturing processes.
Benefits of Regular Maintenance
Regular maintenance is essential for keeping cooling systems in optimal condition. By conducting routine inspections, cleaning, and servicing, manufacturers can ensure that their cooling units operate at peak performance. Here are some key benefits of regular maintenance:
1. Improved Energy Efficiency
Regular maintenance helps identify and address any issues that may be affecting the energy efficiency of the cooling system. For example, a clogged air filter can restrict airflow, causing the cooling unit to work harder, consume more energy, and operate less efficiently. By regularly cleaning or replacing air filters, manufacturers can improve the unit's energy efficiency and reduce energy consumption.
2. Extended Lifespan
Proper maintenance can significantly extend the lifespan of a cooling unit. During routine inspections, technicians can identify potential problems, such as worn-out components or leaks, before they cause major damage. By addressing these issues promptly, manufacturers can prevent costly breakdowns and increase the longevity of the cooling system.
3. Reduced Downtime
Regular maintenance can help minimize unexpected breakdowns and reduce downtime in manufacturing processes. By scheduling routine maintenance, manufacturers can detect and repair any issues before they escalate and disrupt production. This proactive approach helps minimize the risk of unexpected system failures and ensures uninterrupted cooling for critical operations.
4. Cost Savings
Regular maintenance can lead to significant cost savings in the long run. By improving energy efficiency and reducing the risk of breakdowns, manufacturers can lower their energy bills and avoid costly repairs or replacements. Additionally, proactive maintenance can help identify opportunities for optimization and streamlining, further reducing operating costs in the manufacturing process.
Importance of Proper Insulation
In addition to regular maintenance, proper insulation is crucial for maximizing cooling efficiency. Insulation helps create a barrier between the cooling system and the surrounding environment, preventing heat transfer and ensuring that the cooling unit operates at the desired temperature. Here are some reasons why proper insulation is essential:
1. Energy Conservation
Proper insulation reduces heat transfer between the cooling system and the surrounding environment. By minimizing heat gain or loss, insulation helps the cooling unit maintain the desired temperature more effectively, reducing the need for excessive cooling or heating. This, in turn, leads to energy conservation and lower energy costs.
2. Preventing Condensation
Insulation also helps prevent condensation, which can be detrimental to the cooling system's efficiency and performance. Condensation occurs when warm air comes into contact with a cold surface, causing moisture to form. If condensation forms on the cooling system's components, it can lead to corrosion, mold growth, and other issues that can compromise its efficiency. Proper insulation helps maintain the temperature of the cooling unit's surfaces, preventing condensation and ensuring optimal performance.
3. Enhanced Temperature Control
Proper insulation improves temperature control within the cooling system, allowing manufacturers to maintain the desired temperature more accurately. By minimizing heat transfer, insulation helps the cooling unit distribute cool air evenly and prevent temperature fluctuations. This is especially important in manufacturing processes that require precise temperature control, such as semiconductor fabrication or pharmaceutical production.
4. Noise Reduction
Insulation can also help reduce noise levels generated by the cooling system. By absorbing sound waves, insulation materials can minimize noise pollution in industrial settings, creating a more comfortable and productive working environment. This is particularly beneficial in facilities where noise control is essential, such as research laboratories or medical facilities.
Conclusion
Regular maintenance and proper insulation are essential for maximizing cooling efficiency in manufacturing and commercial cooling units. By conducting routine inspections, cleaning, and servicing, manufacturers can improve energy efficiency, extend the lifespan of their cooling systems, and reduce downtime. Additionally, proper insulation helps conserve energy, prevent condensation, enhance temperature control, and reduce noise levels. By investing in regular maintenance and proper insulation, manufacturers can achieve sustainable and energy-efficient cooling solutions, leading to cost savings, improved productivity, and a reduced environmental footprint.
Related Blogs
The importance of education and awareness in promoting the adoption of green cooling technology
Read More