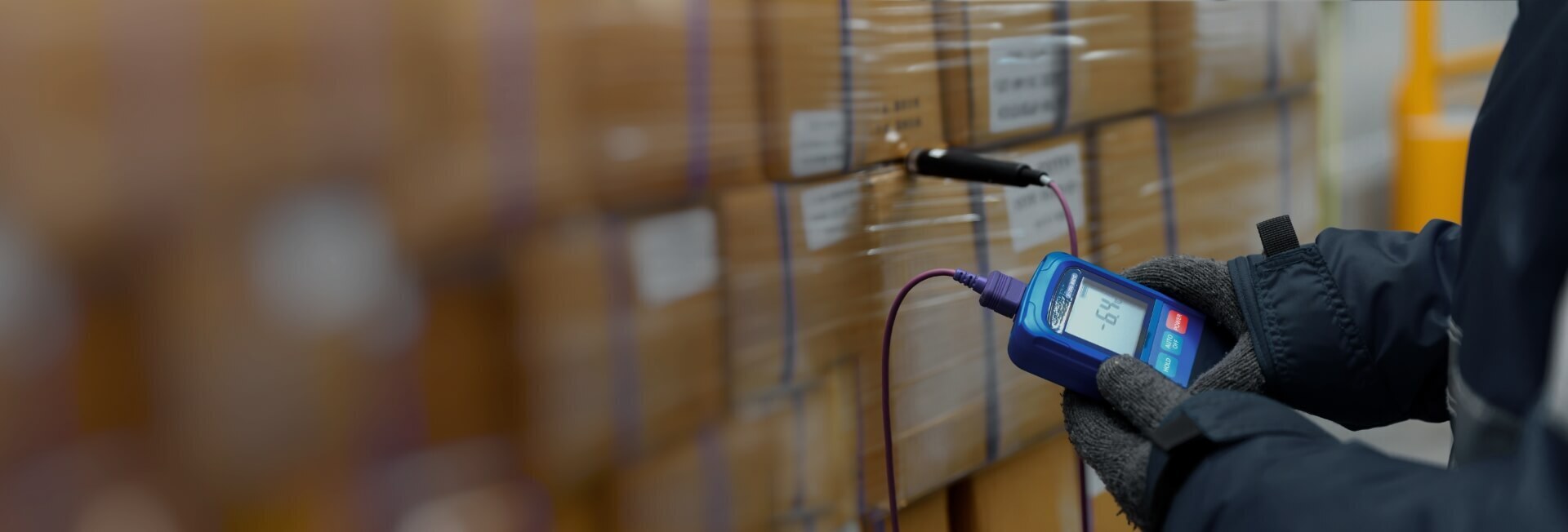
The importance of continuous improvement in achieving streamlined manufacturing
- Home
- Resources
- Cooling Unit Manufacturing Insights
- The importance of continuous improvement in achieving streamlined manufacturing
The Power of Continuous Improvement in Streamlined Manufacturing
Streamlined manufacturing is a crucial aspect of any successful business. It involves optimizing processes, reducing waste, and improving overall efficiency to ensure that products are manufactured and delivered in the most cost-effective and timely manner possible. One of the key strategies for achieving streamlined manufacturing is continuous improvement. By constantly evaluating and refining processes, businesses can stay ahead of the competition and maximize their operational efficiency.
What is Continuous Improvement?
Continuous improvement is an ongoing effort to enhance products, services, or processes. It is a systematic approach that involves identifying areas for improvement, making changes, and then evaluating the results. The goal of continuous improvement is to eliminate waste, reduce costs, and increase productivity. By constantly striving for improvement, businesses can achieve higher levels of efficiency and deliver better products or services to their customers.
The Benefits of Continuous Improvement in Manufacturing
Continuous improvement is essential in manufacturing because it leads to several significant benefits. Let's explore some of the key advantages:
1. Increased Efficiency
Continuous improvement helps businesses identify and eliminate bottlenecks, inefficiencies, and unnecessary steps in the manufacturing process. By streamlining operations, businesses can produce more with fewer resources, reducing costs and increasing overall efficiency. This leads to shorter lead times, faster delivery, and improved customer satisfaction.
2. Waste Reduction
Another major benefit of continuous improvement is waste reduction. By analyzing the manufacturing process, businesses can identify and eliminate waste in the form of overproduction, excess inventory, defects, and unnecessary motion or transportation. This not only saves costs but also contributes to a more sustainable and environmentally friendly approach to manufacturing.
3. Higher Quality Products
Continuous improvement also helps businesses improve the quality of their products. By identifying and addressing defects or issues in the manufacturing process, businesses can ensure that their products meet or exceed customer expectations. This leads to higher customer satisfaction, increased brand loyalty, and ultimately, higher sales and profitability.
4. Employee Engagement and Empowerment
Continuous improvement involves employees at all levels of the organization. By encouraging employees to identify and suggest improvements, businesses can create a culture of engagement and empowerment. When employees feel valued and involved in the improvement process, they are more motivated, productive, and committed to achieving the company's goals.
Implementing Continuous Improvement in Manufacturing
Implementing continuous improvement in manufacturing requires a systematic approach and a commitment from the entire organization. Here are some key steps to follow:
1. Set Clear Goals
The first step in implementing continuous improvement is to set clear goals. Identify the areas of the manufacturing process that need improvement and define specific, measurable objectives. These goals will serve as the foundation for your improvement efforts and help you track progress along the way.
2. Involve Employees
Engage employees at all levels of the organization in the improvement process. Encourage them to provide feedback, suggestions, and ideas for improvement. This not only helps in identifying areas for improvement but also creates a sense of ownership and accountability among employees.
3. Analyze the Current Process
Analyze the current manufacturing process to identify areas of waste, inefficiency, and opportunities for improvement. Use tools such as value stream mapping, process flowcharts, and data analysis to gain insights into the process. This analysis will help you prioritize improvement efforts and focus on areas that will have the greatest impact.
4. Implement Changes
Once you have identified areas for improvement, develop and implement changes to the manufacturing process. This could involve redesigning workflows, reorganizing workstations, implementing new technology, or training employees on new techniques. Ensure that the changes are well communicated and that employees are provided with the necessary support and resources to implement them effectively.
5. Measure and Evaluate
Measure the impact of the changes implemented and evaluate their effectiveness. Use key performance indicators (KPIs) to track progress towards your goals and identify any further areas for improvement. Regularly review and analyze the data to ensure that the improvements are sustainable and continue to deliver the desired results.
The Role of Technology in Continuous Improvement
Technology plays a crucial role in continuous improvement in manufacturing. Here are some ways in which technology can support the implementation of continuous improvement:
1. Data Collection and Analysis
Technology enables businesses to collect and analyze vast amounts of data related to the manufacturing process. This data can provide valuable insights into inefficiencies, bottlenecks, and areas for improvement. By leveraging data analytics tools and techniques, businesses can make data-driven decisions and prioritize improvement efforts.
2. Automation
Automation technology can streamline manufacturing processes by reducing manual labor, eliminating human error, and increasing speed and accuracy. By automating repetitive tasks, businesses can free up employees' time to focus on more value-added activities, such as problem-solving and process improvement.
3. Communication and Collaboration
Technology facilitates communication and collaboration among employees, departments, and even supply chain partners. With the right collaboration tools, employees can easily share ideas, feedback, and best practices for continuous improvement. This promotes cross-functional collaboration and ensures that improvement efforts are coordinated and aligned across the organization.
4. Real-time Monitoring and Feedback
Real-time monitoring and feedback systems enable businesses to track the performance of the manufacturing process in real-time. By providing immediate feedback on key metrics and performance indicators, businesses can quickly identify issues and make necessary adjustments to ensure continuous improvement.
Conclusion
Continuous improvement is a powerful tool for achieving streamlined manufacturing. By constantly evaluating and refining processes, businesses can enhance efficiency, reduce waste, improve product quality, and engage employees in the improvement process. With the right goals, employee involvement, analysis, implementation, and technology, businesses can stay ahead of the competition and achieve sustainable success in the manufacturing industry.