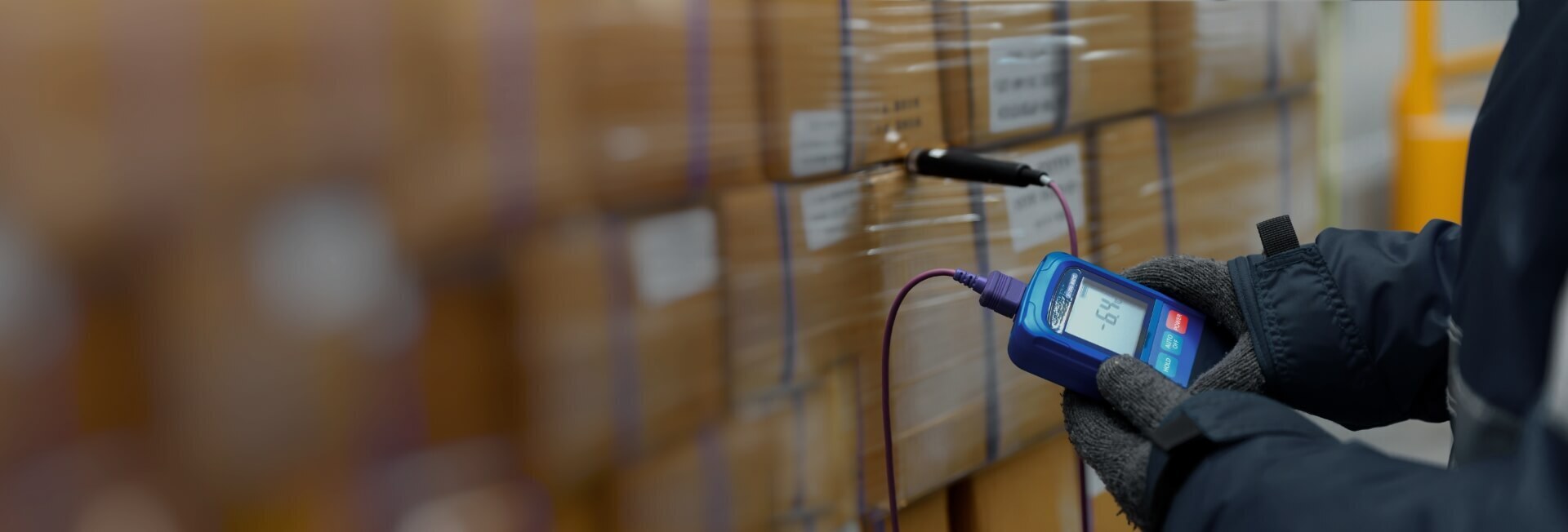
The importance of benchmarking and performance metrics in measuring energy efficiency in manufacturing
- Home
- Resources
- Cooling Unit Manufacturing Insights
- The importance of benchmarking and performance metrics in measuring energy efficiency in manufacturing
The Importance of Benchmarking and Performance Metrics in Measuring Energy Efficiency in Manufacturing
Energy efficiency is a critical aspect of sustainable manufacturing. As companies strive to reduce their environmental footprint and improve their bottom line, measuring and benchmarking energy efficiency becomes crucial. By implementing performance metrics and monitoring energy consumption, manufacturers can identify areas for improvement, optimize their supply chain, and implement sustainable cooling solutions that reduce energy consumption.
Supply Chain Optimization for Energy Efficiency
Supply chain optimization plays a significant role in improving energy efficiency in manufacturing. By analyzing the entire production and distribution process, manufacturers can identify inefficiencies and take steps to reduce energy consumption. One area where supply chain optimization can make a significant impact is cooling technology.
Commercial cooling units are essential in various manufacturing processes, from food production to semiconductor manufacturing. Cooling system manufacturers have been developing custom cooling solutions that prioritize energy efficiency and sustainability. By implementing precision cooling systems and using environmentally friendly cooling units, manufacturers can achieve substantial energy savings.
Supply chain optimization also involves streamlining manufacturing processes to reduce energy consumption. By assessing the energy requirements of each production stage and identifying areas where energy can be saved, manufacturers can make informed decisions to improve efficiency. This could involve investing in energy-efficient machinery, implementing waste heat recovery systems, or optimizing production schedules to minimize energy waste.
Benchmarking and Performance Metrics in Cooling Systems
Benchmarking and performance metrics are essential tools in measuring energy efficiency in cooling systems. By establishing baseline energy consumption and comparing it to industry benchmarks, manufacturers can identify areas for improvement and set energy-saving goals. This allows manufacturers to track their progress over time and make informed decisions to optimize their cooling systems.
One common performance metric used in cooling systems is the coefficient of performance (COP). The COP measures the ratio of cooling output to energy input and is an indicator of how efficiently a cooling system operates. By monitoring the COP and comparing it to industry standards, manufacturers can identify if their cooling systems are operating optimally or if there are opportunities for improvement.
Benchmarking also allows manufacturers to compare the energy efficiency of their cooling systems to similar facilities, identify best practices, and implement changes to improve performance. This could involve upgrading to more energy-efficient equipment, implementing better insulation, or optimizing the cooling system's control algorithms to minimize energy waste.
The Benefits of Energy Efficiency in Manufacturing
Investing in energy efficiency in manufacturing offers numerous benefits, both for the environment and the bottom line. By reducing energy consumption, manufacturers can significantly lower their carbon footprint and contribute to a more sustainable future. This not only aligns with corporate social responsibility goals but can also enhance a company's reputation and attract environmentally conscious customers.
In addition to the environmental benefits, energy efficiency in manufacturing can lead to significant cost savings. By optimizing supply chains, streamlining manufacturing processes, and implementing energy-efficient cooling systems, manufacturers can reduce their energy bills and improve their profitability. This allows companies to allocate resources to other areas of their business, such as research and development or employee training.
Furthermore, energy-efficient manufacturing can also help companies comply with government regulations and avoid potential penalties. Many countries have implemented energy efficiency standards and incentives to encourage businesses to reduce their energy consumption. By meeting or exceeding these standards, manufacturers can avoid fines and take advantage of government rebates or tax credits.
Conclusion
Energy efficiency is a critical aspect of sustainable manufacturing. By implementing benchmarking and performance metrics, manufacturers can measure and improve their energy efficiency, optimize their supply chains, and implement sustainable cooling solutions. The benefits of energy-efficient manufacturing extend beyond reducing environmental impact and can lead to significant cost savings and improved profitability. By prioritizing energy efficiency, manufacturers can contribute to a more sustainable future while enhancing their competitiveness in the market.
Related Blogs
The importance of education and awareness in promoting the adoption of green cooling technology
Read More