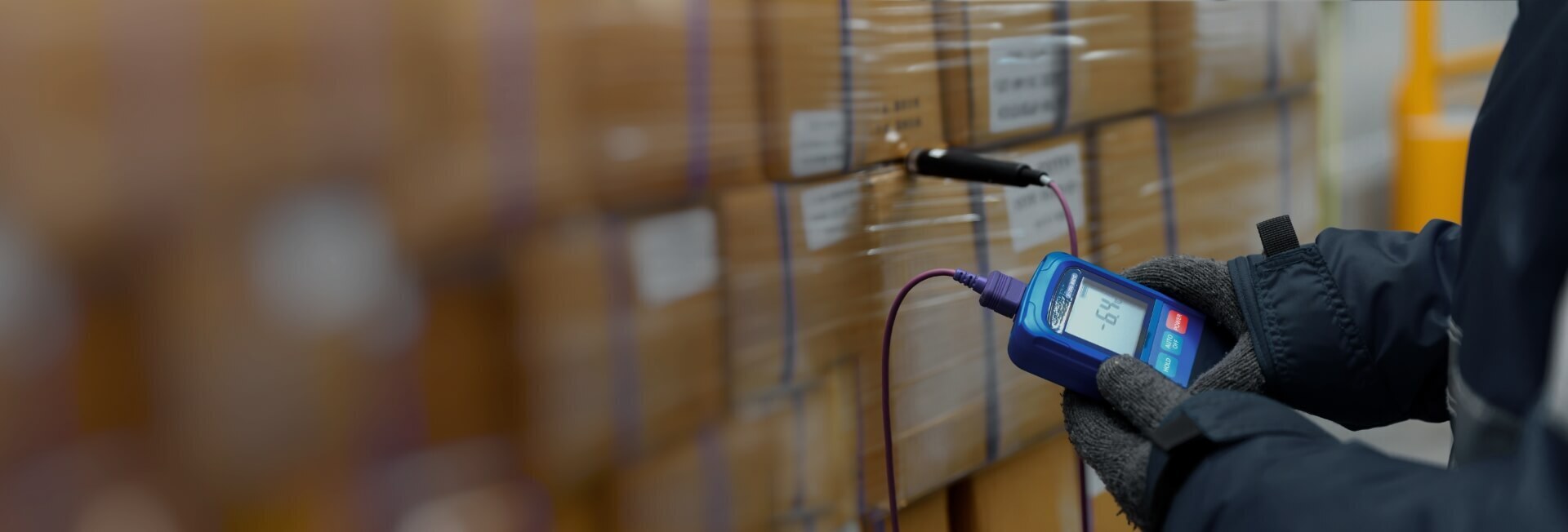
The impact of real-time data monitoring on achieving streamlined manufacturing
- Home
- Resources
- Cooling Unit Manufacturing Insights
- The impact of real-time data monitoring on achieving streamlined manufacturing
Introduction
Manufacturing efficiency is a key factor in today's competitive business landscape. As companies strive to optimize their supply chain and streamline their operations, they are increasingly turning to real-time data monitoring to gain insights into their processes and make data-driven decisions. This article explores the impact of real-time data monitoring on achieving streamlined manufacturing and highlights the role of advanced cooling technology in improving efficiency and sustainability.
Streamlining Manufacturing with Real-Time Data Monitoring
Real-time data monitoring involves collecting and analyzing data from various sources in real-time to gain insights into the performance of manufacturing processes. By monitoring key performance indicators (KPIs) such as production rates, equipment downtime, and quality metrics, manufacturers can identify bottlenecks, inefficiencies, and areas for improvement.
Real-time data monitoring enables manufacturers to make data-driven decisions and take proactive measures to optimize their operations. By having access to up-to-date information, manufacturers can identify and address issues as they arise, minimizing downtime and maximizing productivity. This real-time visibility into the manufacturing process allows for proactive maintenance, reducing the risk of equipment failure and improving overall efficiency.
Furthermore, real-time data monitoring enables manufacturers to track and analyze the performance of their suppliers and partners in the production and distribution process. By monitoring key metrics such as delivery times, inventory levels, and quality standards, manufacturers can ensure that their supply chain is operating smoothly and efficiently.
The Role of Cooling Technology in Streamlined Manufacturing
Cooling technology plays a crucial role in many manufacturing processes, particularly in industries that rely on precision and temperature control. Commercial cooling units are used in a wide range of applications, from food and beverage production to pharmaceutical manufacturing.
Cooling system manufacturers have been focusing on developing custom cooling solutions that are not only energy-efficient but also environmentally friendly. These sustainable cooling solutions help reduce energy consumption and minimize the carbon footprint of manufacturing operations.
Industrial cooling units are designed to provide precise temperature control, ensuring that products are manufactured to the highest quality standards. Precision cooling systems are crucial in industries such as electronics manufacturing, where even slight temperature variations can impact the performance and reliability of the final product.
Green cooling technology is another area of focus for cooling system manufacturers. By using eco-friendly refrigerants and energy-efficient components, these cooling units help reduce greenhouse gas emissions and contribute to a more sustainable manufacturing process.
The Benefits of Real-Time Data Monitoring and Cooling Technology
Integrating real-time data monitoring with advanced cooling technology offers numerous benefits for manufacturers looking to streamline their operations and improve efficiency:
1. Improved Efficiency and Productivity
Real-time data monitoring allows manufacturers to identify inefficiencies and bottlenecks in their processes, enabling them to take corrective actions and optimize their operations. By monitoring equipment performance and environmental conditions, manufacturers can ensure that their cooling systems are operating at peak efficiency, minimizing energy waste and maximizing productivity.
2. Proactive Maintenance
Real-time data monitoring enables manufacturers to detect equipment failures or malfunctions before they cause production disruptions. By monitoring key indicators such as temperature, pressure, and performance metrics, manufacturers can schedule preventive maintenance and avoid costly downtime.
3. Enhanced Quality Control
Real-time data monitoring allows manufacturers to track quality metrics in real-time, ensuring that products meet the highest standards. By integrating cooling technology with data monitoring systems, manufacturers can maintain precise temperature control throughout the production process, resulting in consistent product quality.
4. Sustainability and Environmental Benefits
By using energy-efficient cooling technology and monitoring energy consumption in real-time, manufacturers can reduce their carbon footprint and contribute to a more sustainable manufacturing process. Sustainable cooling solutions help minimize energy waste and greenhouse gas emissions, aligning with the growing demand for environmentally friendly products.
Conclusion
Real-time data monitoring is transforming the manufacturing industry by enabling manufacturers to make data-driven decisions and optimize their operations. By integrating advanced cooling technology into the data monitoring process, manufacturers can achieve streamlined manufacturing, improved efficiency, and sustainability. As the demand for eco-friendly and energy-efficient products continues to grow, the role of real-time data monitoring and cooling technology in manufacturing will become increasingly important.
For manufacturers looking to stay competitive and meet the evolving demands of consumers and regulators, investing in real-time data monitoring and advanced cooling technology is crucial. By leveraging real-time insights and sustainable cooling solutions, manufacturers can achieve significant cost savings, improve product quality, and reduce their environmental impact.
Related Blogs
The importance of education and awareness in promoting the adoption of green cooling technology
Read More