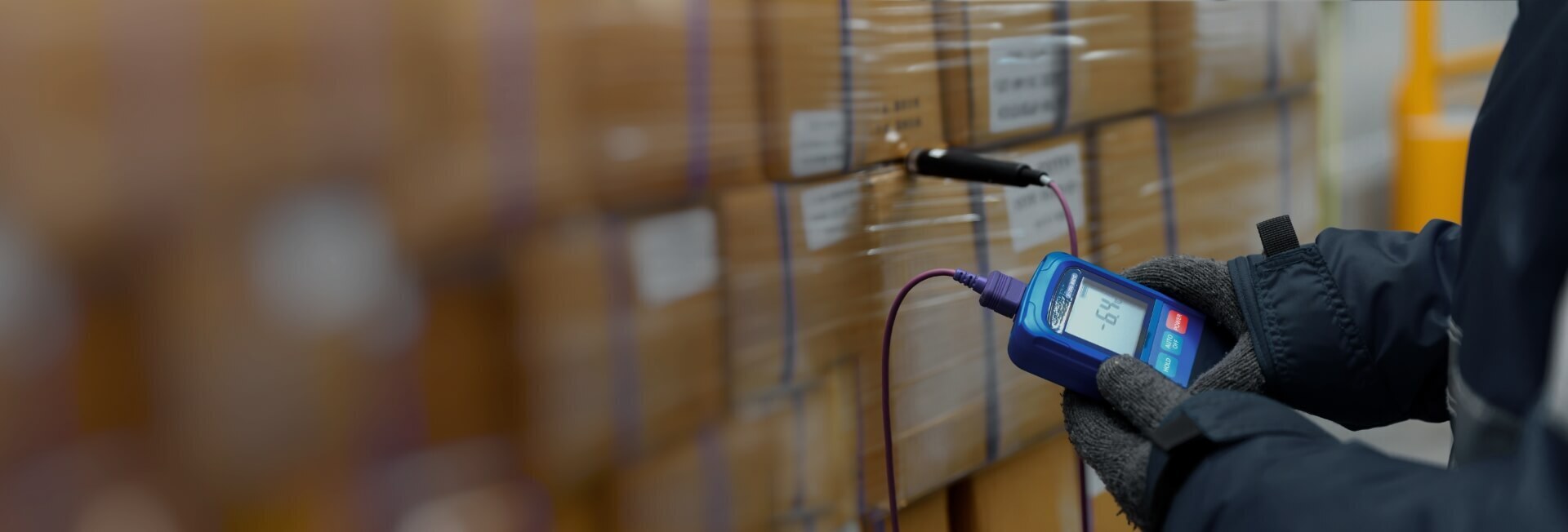
The impact of outsourcing on manufacturing efficiency
- Home
- Resources
- Cooling Unit Manufacturing Insights
- The impact of outsourcing on manufacturing efficiency
Introduction
In today's globalized economy, outsourcing has become a common practice for businesses looking to streamline their operations and improve manufacturing efficiency. By leveraging the expertise and resources of external partners, companies can focus on their core competencies while enjoying the benefits of cost savings, increased productivity, and access to specialized technologies. This article explores the impact of outsourcing on manufacturing efficiency and the various ways in which it can help businesses optimize their supply chain and improve overall performance.
Supply Chain Optimization
One of the key advantages of outsourcing in manufacturing is the opportunity to optimize the supply chain. By partnering with specialized suppliers, companies can improve the flow of materials and components, reduce lead times, and minimize inventory levels. This leads to a more efficient production and distribution process, allowing businesses to respond quickly to changing market demands and reduce the risk of stockouts or excess inventory.
Cooling Technology and Custom Cooling Solutions
Cooling technology plays a crucial role in various industries, particularly those involved in the manufacturing of commercial cooling units, industrial cooling units, and precision cooling systems. Outsourcing to cooling system manufacturers that specialize in custom cooling solutions can significantly improve manufacturing efficiency. These external partners have the expertise and resources to design and produce energy-efficient and environmentally friendly cooling units. By leveraging their knowledge and capabilities, companies can enhance their product offerings, reduce energy consumption, and meet sustainability goals.
Streamlined Manufacturing Processes
Outsourcing certain manufacturing processes can also lead to streamlined operations and improved efficiency. For example, by partnering with external suppliers for component manufacturing, companies can reduce their production cycle times and achieve cost savings. These suppliers are often equipped with advanced machinery and production techniques, enabling them to produce components at a faster rate and with higher precision. This allows the primary manufacturer to focus on assembly and final product testing, resulting in a more efficient manufacturing process.
Benefits of Outsourcing Energy Efficiency in Manufacturing
Energy efficiency is a critical aspect of modern manufacturing. By outsourcing energy-intensive processes to external partners that specialize in sustainable cooling solutions and green cooling technology, companies can reduce their environmental impact and improve overall energy efficiency. These outsourcing partners have the knowledge and experience to design and manufacture eco-friendly cooling units that consume less energy while maintaining optimal performance. This not only helps businesses meet regulatory requirements and sustainability goals but also results in long-term cost savings through reduced energy consumption.
Conclusion
In conclusion, outsourcing can have a significant impact on manufacturing efficiency. By optimizing the supply chain, leveraging specialized technologies, and streamlining manufacturing processes, businesses can improve productivity, reduce costs, and enhance overall performance. Furthermore, by outsourcing energy-intensive processes to partners that specialize in sustainable cooling solutions and green cooling technology, companies can achieve their energy efficiency and sustainability goals. As the global economy continues to evolve, outsourcing will remain a valuable strategy for businesses looking to stay competitive and drive growth in the manufacturing sector.
Related Blogs
The importance of education and awareness in promoting the adoption of green cooling technology
Read More