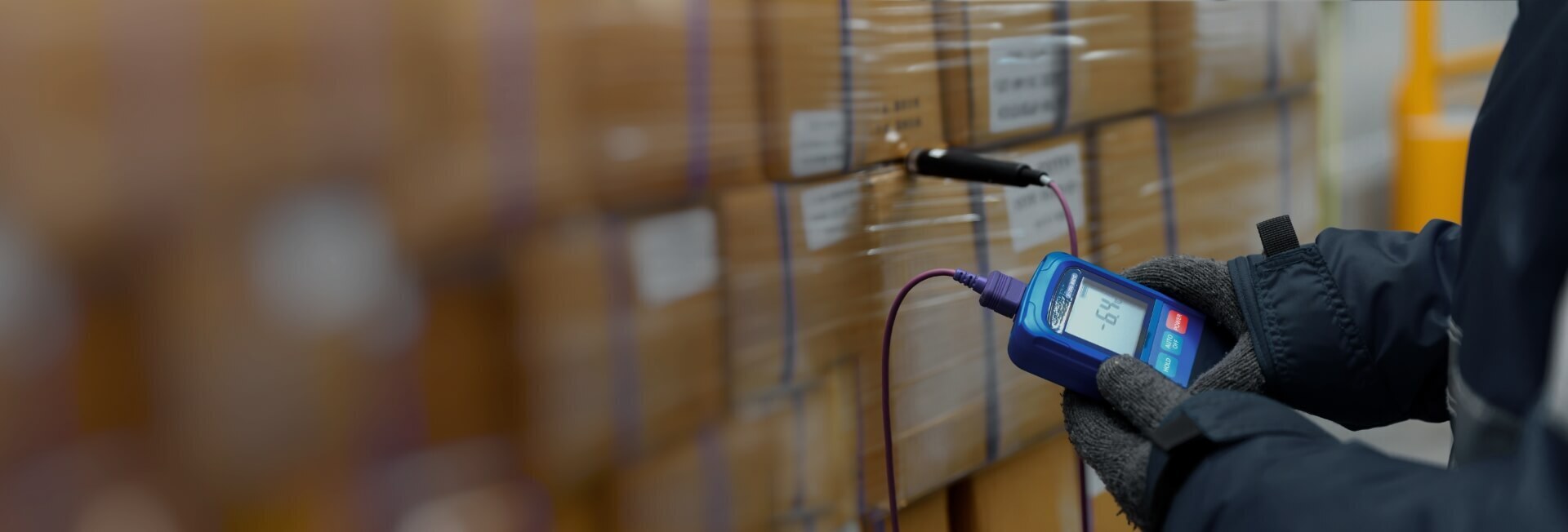
The impact of green cooling technology on reducing the use of refrigerants with high global warming potential
- Home
- Resources
- Cooling Unit Manufacturing Insights
- The impact of green cooling technology on reducing the use of refrigerants with high global warming potential
The Impact of Green Cooling Technology on Reducing the Use of Refrigerants with High Global Warming Potential
The manufacturing industry has long been a significant contributor to global warming and climate change. The production and distribution of goods require large amounts of energy, which often results in the emission of greenhouse gases. One particular area of concern is the cooling systems used in various industrial processes and commercial cooling units. These systems traditionally rely on refrigerants with high global warming potential, which have a detrimental impact on the environment. However, with the advancements in green cooling technology, there is hope for a more sustainable and eco-friendly future.
What is Green Cooling Technology?
Green cooling technology refers to the use of sustainable and environmentally friendly cooling solutions in various industries. It encompasses the development and implementation of energy-efficient cooling systems that minimize the use of refrigerants with high global warming potential. These systems are designed to reduce energy consumption, improve manufacturing efficiency, and minimize the overall environmental impact of cooling processes.
The Benefits of Green Cooling Technology
1. Environmental Impact: One of the primary benefits of green cooling technology is its positive impact on the environment. By reducing the use of refrigerants with high global warming potential, these systems help mitigate climate change and reduce greenhouse gas emissions. They contribute to a more sustainable and eco-friendly future by promoting energy efficiency and reducing the carbon footprint of cooling processes.
2. Energy Efficiency: Green cooling technology is designed to be highly energy efficient. These systems utilize innovative technologies and techniques to optimize energy consumption and minimize waste. By streamlining manufacturing processes and implementing precision cooling systems, energy consumption can be significantly reduced, leading to cost savings and a more sustainable operation.
3. Cost Savings: Implementing green cooling technology can lead to significant cost savings for businesses. By reducing energy consumption and optimizing manufacturing efficiency, companies can lower their operational costs. Additionally, the use of sustainable cooling solutions can result in the reduction of maintenance and repair expenses associated with traditional cooling systems.
4. Compliance with Regulations: As environmental regulations become more stringent, businesses need to adapt and comply with new requirements. Green cooling technology helps companies meet these regulations by minimizing the use of refrigerants with high global warming potential. By implementing sustainable cooling solutions, businesses can ensure compliance while also reducing their environmental impact.
Implementing Green Cooling Technology in Manufacturing
Manufacturing efficiency and supply chain optimization are key factors in implementing green cooling technology. By streamlining manufacturing processes and optimizing energy consumption, companies can achieve substantial energy savings and reduce their environmental impact. This can be achieved through:
1. Energy-Efficient Equipment: Investing in energy-efficient industrial cooling units and commercial cooling systems is crucial for reducing energy consumption. Manufacturers should partner with cooling system manufacturers that specialize in custom cooling solutions to ensure optimal energy efficiency. These customized solutions can be tailored to the specific needs of the manufacturing process, resulting in maximum energy savings.
2. Process Optimization: Analyzing and optimizing manufacturing processes can identify areas of energy waste and inefficiency. By implementing process improvements and incorporating energy-saving measures, manufacturers can reduce energy consumption and minimize environmental impact. This can include measures such as using waste heat recovery systems and implementing efficient cooling control strategies.
3. Sustainable Materials: In addition to energy-efficient equipment, using sustainable materials in manufacturing processes can further enhance the environmental impact. Choosing materials that have a lower carbon footprint and can be recycled or reused can contribute to a more sustainable operation. Manufacturers should partner with suppliers that prioritize sustainability and offer environmentally friendly materials.
The Future of Green Cooling Technology
The future of green cooling technology looks promising, with continued advancements in energy efficiency and sustainability. As more businesses recognize the benefits of implementing sustainable cooling solutions, the demand for green cooling technology is expected to increase. This will drive further innovation and development in the industry, leading to even more energy-efficient and environmentally friendly cooling systems.
Furthermore, as governments and regulatory bodies continue to prioritize environmental sustainability, stricter regulations may be put in place to limit the use of refrigerants with high global warming potential. This will encourage businesses to adopt green cooling technology and invest in sustainable cooling solutions to comply with these regulations.
In conclusion, green cooling technology is making a significant impact on reducing the use of refrigerants with high global warming potential. By promoting energy efficiency, manufacturing efficiency, and environmental sustainability, these sustainable cooling solutions are helping to create a more eco-friendly future. As businesses recognize the benefits of implementing green cooling technology, the industry is expected to continue growing and driving further innovation in the coming years.
Related Blogs
The importance of education and awareness in promoting the adoption of green cooling technology
Read More