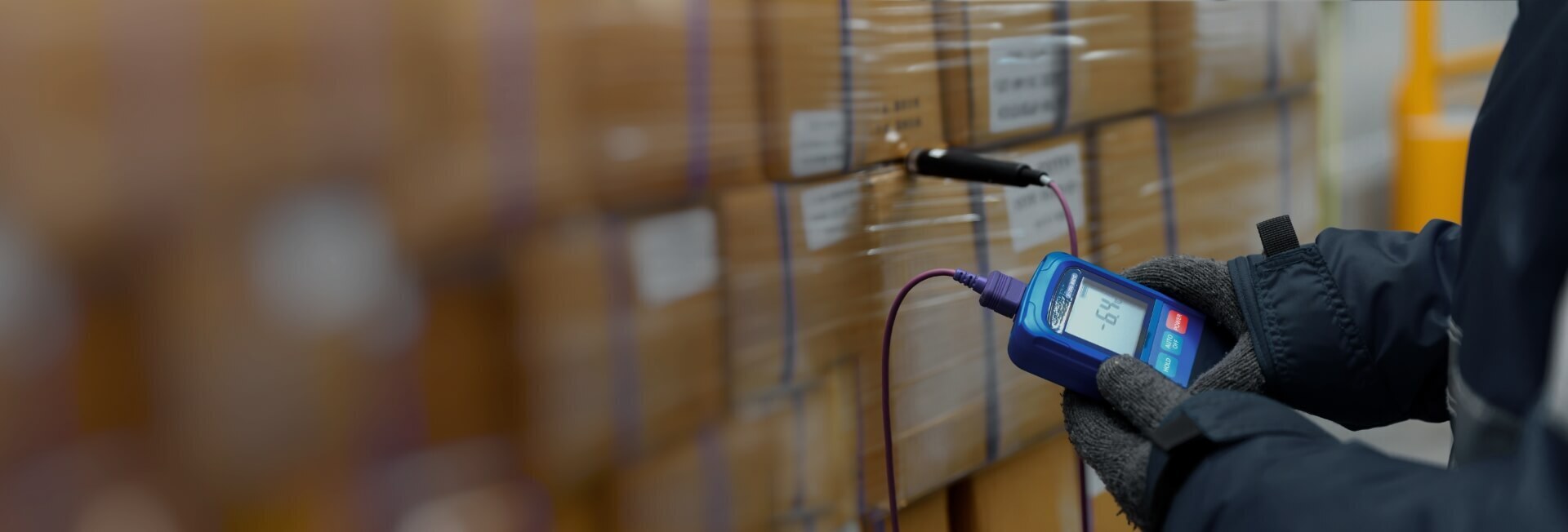
The impact of digital twin technology on achieving streamlined manufacturing
- Home
- Resources
- Cooling Unit Manufacturing Insights
- The impact of digital twin technology on achieving streamlined manufacturing
The Impact of Digital Twin Technology on Achieving Streamlined Manufacturing
In today's fast-paced and highly competitive manufacturing industry, companies are constantly searching for ways to optimize their supply chains, improve manufacturing efficiency, and reduce costs. One technology that is revolutionizing the way manufacturers operate is digital twin technology.
What is Digital Twin Technology?
Digital twin technology is a virtual replica or simulation of a physical object, process, or system. It uses real-time data and advanced analytics to create a digital representation that can be used for analysis, optimization, and prediction. In the context of manufacturing, digital twin technology enables manufacturers to create virtual replicas of their production lines, equipment, and even entire factories.
The Benefits of Digital Twin Technology in Manufacturing
Digital twin technology offers numerous benefits to manufacturers, ranging from improved operational efficiency to better decision-making. Here are some of the key advantages:
1. Supply Chain Optimization
One of the biggest challenges in manufacturing is optimizing the supply chain to ensure the right parts and materials are available at the right time. Digital twin technology can help manufacturers achieve this by creating a virtual representation of the supply chain. This allows manufacturers to track inventory levels, identify bottlenecks, and optimize workflows to improve overall supply chain efficiency.
2. Manufacturing Efficiency
By creating a digital twin of their production lines and equipment, manufacturers can analyze and optimize various aspects of their manufacturing processes. For example, they can simulate different production scenarios to identify the most efficient workflows, minimize downtime, and reduce waste. This not only improves productivity but also helps manufacturers deliver products to market faster.
3. Improved Maintenance and Predictive Analytics
Another significant benefit of digital twin technology is its ability to monitor and predict equipment performance. By collecting real-time data from sensors embedded in machinery, manufacturers can create virtual models that mimic the behavior of physical assets. This enables them to identify potential issues before they occur, schedule preventative maintenance, and reduce unplanned downtime.
4. Enhanced Product Development
Digital twin technology can also be used to improve product development and innovation. By simulating and testing new product designs virtually, manufacturers can identify design flaws, optimize performance, and reduce the need for physical prototypes. This not only speeds up the product development process but also reduces costs associated with testing and iteration.
Case Study: How Digital Twin Technology is Transforming the Cooling System Manufacturing Industry
One industry that has greatly benefited from digital twin technology is the cooling system manufacturing industry. Cooling systems are critical for various applications, including data centers, industrial processes, and commercial buildings. The use of digital twin technology has revolutionized the way cooling system manufacturers design, produce, and distribute their products.
1. Custom Cooling Solutions
Digital twin technology allows cooling system manufacturers to create custom cooling solutions tailored to the specific needs of their customers. By simulating the cooling requirements of different applications, manufacturers can design and optimize cooling systems that are highly efficient and precisely meet their customers' needs. This level of customization not only improves performance but also reduces energy consumption and costs.
2. Energy-Efficiency in Manufacturing
Energy-efficiency is a key consideration for manufacturers, as it not only reduces operational costs but also contributes to environmental sustainability. Digital twin technology enables cooling system manufacturers to optimize the energy consumption of their production processes by simulating and analyzing different manufacturing scenarios. By identifying energy-intensive processes and implementing energy-saving measures, manufacturers can reduce their carbon footprint and achieve sustainable manufacturing.
3. Precision Cooling Systems
Digital twin technology allows cooling system manufacturers to design and optimize precision cooling systems that maintain stable temperatures and humidity levels in critical environments. By simulating the behavior of cooling units and their interaction with the surrounding environment, manufacturers can ensure that their products deliver precise and consistent cooling performance. This is particularly important for applications such as data centers, where even slight temperature fluctuations can have significant consequences.
4. Sustainable Cooling Solutions
As the world becomes more conscious of environmental sustainability, the demand for environmentally-friendly cooling solutions is increasing. Digital twin technology enables cooling system manufacturers to design and optimize cooling systems that are energy-efficient and use environmentally-friendly refrigerants. By simulating the performance of different cooling technologies and materials, manufacturers can identify the most sustainable cooling solutions and contribute to a greener future.
The Future of Digital Twin Technology in Manufacturing
The adoption of digital twin technology in the manufacturing industry is expected to continue to grow rapidly in the coming years. As advancements in IoT (Internet of Things) and AI (Artificial Intelligence) continue, digital twin technology will become even more powerful and versatile. Manufacturers will be able to create more detailed and accurate digital replicas, enabling them to optimize their operations, improve product quality, and reduce costs.
In conclusion, digital twin technology has a profound impact on achieving streamlined manufacturing. It offers a wide range of benefits, including supply chain optimization, improved manufacturing efficiency, enhanced maintenance and predictive analytics, and enhanced product development. In the cooling system manufacturing industry, digital twin technology has transformed the way cooling systems are designed, produced, and distributed, leading to custom cooling solutions, energy-efficient manufacturing, precision cooling systems, and sustainable cooling solutions. As the manufacturing industry continues to evolve, digital twin technology will play an increasingly important role in driving innovation, efficiency, and sustainability.
Related Blogs
The importance of education and awareness in promoting the adoption of green cooling technology
Read More