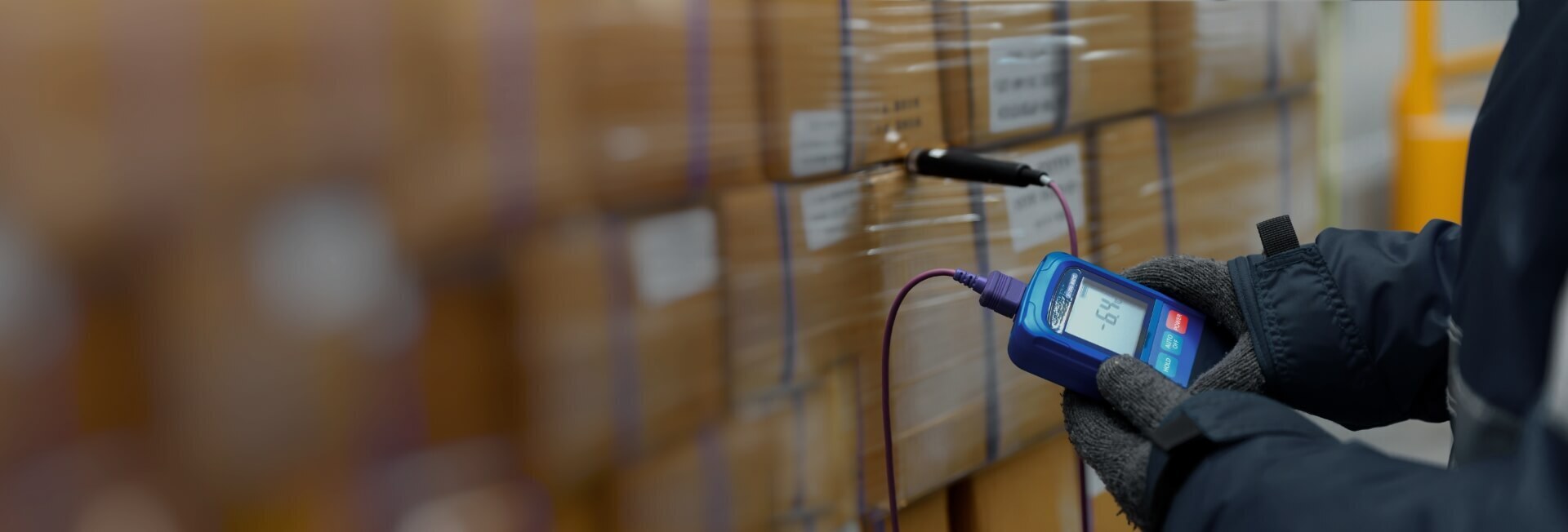
The challenges of maintaining optimal temperature and humidity levels in industrial cooling units
- Home
- Resources
- Cooling Unit Manufacturing Insights
- The challenges of maintaining optimal temperature and humidity levels in industrial cooling units
Industrial cooling units play a vital role in various industries, including production and distribution, manufacturing, and supply chain optimization. These cooling units are responsible for maintaining optimal temperature and humidity levels in order to ensure the efficiency and effectiveness of various processes. However, there are several challenges that come with maintaining these optimal levels, and cooling system manufacturers are constantly working to overcome them. In this article, we will explore the challenges faced in maintaining optimal temperature and humidity levels in industrial cooling units and the solutions that are being implemented.
The Importance of Temperature and Humidity Control in Industrial Cooling Units
Before delving into the challenges, it is important to understand why maintaining optimal temperature and humidity levels is crucial in industrial cooling units. These units are responsible for cooling various processes and equipment, and any deviation from the optimal levels can have serious consequences.
Firstly, temperature control is vital for the proper functioning of machinery and equipment. High temperatures can lead to overheating and subsequent damage to sensitive components. On the other hand, low temperatures can cause inefficiencies and reduce the overall productivity of the system. By maintaining optimal temperature levels, industrial cooling units ensure the longevity and efficiency of the equipment.
Similarly, humidity control is essential in industries where moisture can adversely affect the quality of products. For example, in the food and pharmaceutical industries, excess moisture can lead to the growth of bacteria and mold, compromising the safety and quality of the products. By maintaining optimal humidity levels, industrial cooling units protect the integrity of the products and ensure compliance with industry standards.
The Challenges of Temperature Control in Industrial Cooling Units
Despite the importance of temperature control, there are several challenges that arise in maintaining optimal levels in industrial cooling units.
1. Energy-Efficiency in Manufacturing
One of the major challenges is ensuring energy-efficiency in manufacturing processes. Industrial cooling units consume a significant amount of energy, and optimizing their energy usage is crucial for sustainable and cost-effective operations. Cooling system manufacturers are constantly working on developing energy-efficient solutions that minimize energy consumption without compromising the cooling performance.
These solutions may include incorporating advanced technologies such as variable speed drives, which allow the cooling units to adjust their speed based on the cooling load. By matching the cooling capacity to the actual requirements, energy wastage can be minimized. Additionally, the use of energy-efficient components such as high-efficiency compressors and heat exchangers can further improve the energy-efficiency of industrial cooling units.
2. Precision Cooling Systems
Another challenge is maintaining precise temperature control in industrial cooling units. Different processes and equipment may require different temperature ranges, and it is crucial to ensure that the cooling units can deliver the required levels accurately.
Precision cooling systems are designed to provide precise temperature control within narrow tolerances. These systems often incorporate advanced sensors and control algorithms to continuously monitor and adjust the cooling output. By maintaining precise temperature control, industrial cooling units can ensure the consistency and quality of the processes and products.
3. Green Cooling Technology
In recent years, there has been a growing emphasis on sustainability and environmental responsibility in various industries. This has led to an increased demand for green cooling technology that minimizes the environmental impact of industrial cooling units.
Green cooling technology focuses on reducing the use of harmful refrigerants and minimizing energy consumption. Cooling system manufacturers are developing eco-friendly cooling units that use natural refrigerants with low Global Warming Potential (GWP). Additionally, these units are designed to maximize energy-efficiency and minimize waste heat generation.
By adopting green cooling technology, industries can reduce their carbon footprint and contribute to a more sustainable future.
The Challenges of Humidity Control in Industrial Cooling Units
Humidity control is equally important in industrial cooling units, and it comes with its own set of challenges.
1. Moisture Management
Moisture management is a critical aspect of humidity control in industrial cooling units. Excess moisture can lead to condensation on surfaces, which can cause corrosion and damage to the equipment.
Cooling system manufacturers employ various techniques to manage moisture within the units. These techniques may include the use of desiccant dehumidifiers, which remove moisture from the air before it enters the cooling unit. Additionally, proper insulation and sealing of the units can prevent the ingress of moisture from the surrounding environment.
2. Dehumidification Efficiency
Efficient dehumidification is essential in industries where excess moisture can impact the quality of products. However, achieving efficient dehumidification can be challenging in certain conditions, such as high humidity environments.
Cooling system manufacturers are constantly working on improving the dehumidification efficiency of industrial cooling units. This may involve the use of advanced dehumidification technologies such as desiccant wheels or refrigerant-based dehumidifiers. By optimizing the dehumidification process, industrial cooling units can effectively control the humidity levels and ensure the quality of the products.
3. Environmental Considerations
Similar to temperature control, there is a growing emphasis on environmentally friendly humidity control solutions. Cooling system manufacturers are developing sustainable cooling solutions that minimize the use of harmful chemicals and reduce energy consumption.
These solutions may include the use of eco-friendly desiccants and refrigerants with low environmental impact. Additionally, energy-efficient components and control systems are incorporated to minimize energy wastage. By adopting environmentally friendly cooling units, industries can reduce their ecological footprint and contribute to a greener future.
Conclusion
Maintaining optimal temperature and humidity levels in industrial cooling units is crucial for the efficiency and effectiveness of various processes. However, there are several challenges that come with achieving these optimal levels. Cooling system manufacturers are continuously working on developing innovative solutions to overcome these challenges and provide custom cooling solutions that meet the specific requirements of different industries.
From energy-efficient manufacturing to precision cooling systems and green cooling technology, the industry is evolving to address the demands of sustainable and environmentally friendly cooling. By embracing these advancements, industries can optimize their cooling processes, improve manufacturing efficiency, and contribute to a greener future.
Related Blogs
The importance of education and awareness in promoting the adoption of green cooling technology
Read More