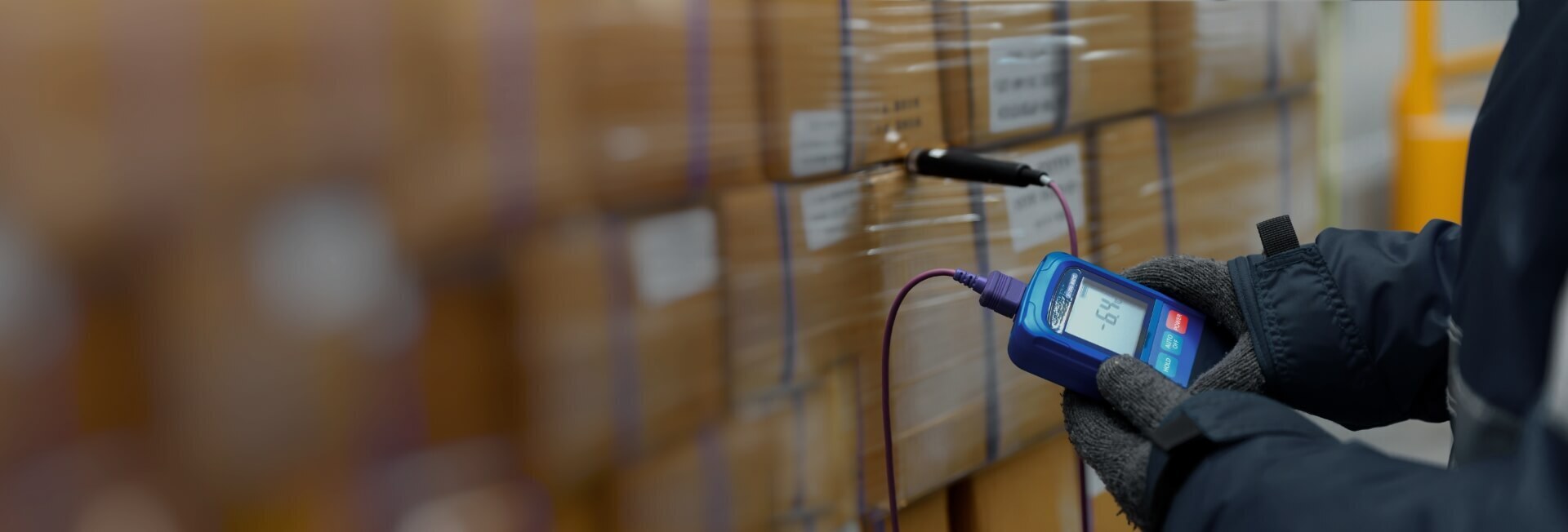
The challenges and opportunities of mass production
- Home
- Resources
- Cooling Unit Manufacturing Insights
- The challenges and opportunities of mass production
The Challenges and Opportunities of Mass Production
Mass production has revolutionized the manufacturing industry, allowing for the efficient production and distribution of goods on a large scale. However, with this increased production comes a number of challenges that manufacturers must navigate. In this article, we will explore the various challenges and opportunities of mass production, as well as the benefits of sustainable and energy-efficient cooling technology.
Supply Chain Optimization
One of the key challenges in mass production is optimizing the supply chain. With large volumes of raw materials and finished goods moving through the supply chain, it is essential to ensure that each stage of the process is streamlined and efficient. Supply chain optimization involves careful planning and coordination to minimize waste, reduce costs, and improve overall efficiency.
Manufacturers must consider factors such as transportation, inventory management, and production scheduling to ensure that products are delivered to customers in a timely manner. By implementing advanced technologies and strategies, such as real-time tracking and predictive analytics, manufacturers can gain better visibility into their supply chains and make data-driven decisions to optimize operations.
Manufacturing Efficiency
Another challenge in mass production is maintaining high levels of manufacturing efficiency. With large-scale production, it is crucial to minimize downtime, reduce errors, and maximize productivity. Manufacturers must continuously strive to improve their processes and eliminate inefficiencies to meet the demands of mass production.
One way to improve manufacturing efficiency is through the use of automation and robotics. By automating repetitive tasks and utilizing advanced robotics, manufacturers can increase production speeds, reduce errors, and improve overall quality. Additionally, implementing lean manufacturing principles, such as just-in-time production and waste reduction, can further enhance efficiency and reduce costs.
Cooling Technology
Cooling technology plays a vital role in mass production, particularly in industries where temperature control is critical, such as food and beverage, pharmaceuticals, and electronics. Commercial cooling units are used to maintain optimal temperatures during various stages of production, ensuring product quality and safety.
Cooling system manufacturers are constantly innovating to develop custom cooling solutions that are energy-efficient and environmentally friendly. Precision cooling systems are designed to provide precise temperature control, minimizing energy consumption and reducing environmental impact. Green cooling technology utilizes sustainable refrigerants and advanced cooling techniques to further enhance energy efficiency and reduce greenhouse gas emissions.
Sustainable Cooling Solutions
As the world becomes more conscious of the environmental impact of manufacturing processes, there is a growing demand for sustainable cooling solutions. Manufacturers are increasingly investing in eco-friendly cooling units that not only meet regulatory requirements but also align with their sustainability goals.
By adopting sustainable cooling solutions, manufacturers can reduce their carbon footprint, conserve natural resources, and contribute to a greener future. Energy-efficient cooling units not only save costs in the long run but also help mitigate the effects of climate change by reducing greenhouse gas emissions.
The Future of Mass Production
Despite the challenges, mass production presents significant opportunities for manufacturers. With advancements in technology and the increasing demand for customized products, there is immense potential for growth and innovation in the manufacturing industry.
Streamlined manufacturing processes, coupled with sustainable and energy-efficient cooling technology, can help manufacturers meet the demands of mass production while reducing their environmental impact. By embracing automation, robotics, and lean manufacturing principles, manufacturers can improve efficiency, reduce costs, and enhance product quality.
Looking ahead, the future of mass production lies in the integration of smart manufacturing, data analytics, and artificial intelligence. These technologies will enable manufacturers to achieve even higher levels of efficiency and productivity, while also driving sustainability and environmental responsibility.
Conclusion
Mass production presents both challenges and opportunities for manufacturers. By optimizing the supply chain, improving manufacturing efficiency, and adopting sustainable cooling solutions, manufacturers can overcome these challenges and position themselves for success in the industry.
The integration of advanced technologies, such as automation, robotics, and data analytics, will continue to drive innovation and improve productivity in mass production. As the world becomes increasingly conscious of the environmental impact of manufacturing, sustainable and energy-efficient practices will become even more critical.
Manufacturers must embrace these opportunities and strive for continuous improvement to stay competitive in the ever-evolving landscape of mass production. By doing so, they can not only meet the demands of the market but also contribute to a more sustainable and environmentally friendly future.
Related Blogs
The importance of education and awareness in promoting the adoption of green cooling technology
Read More