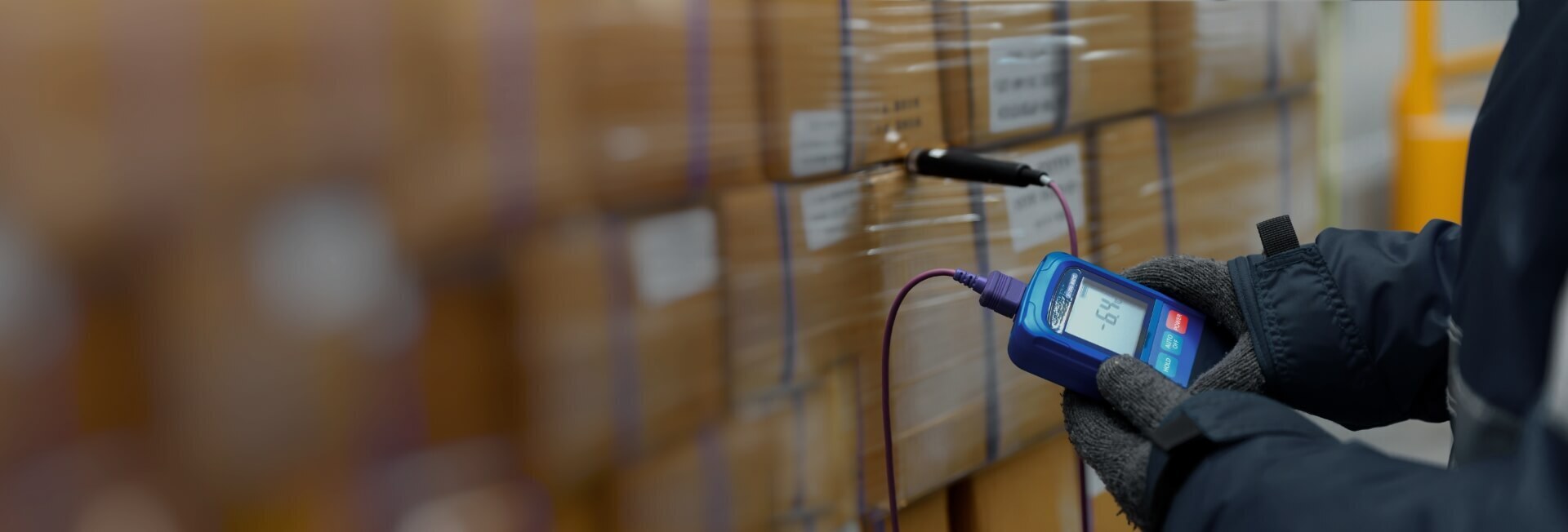
The challenges and opportunities of implementing Industry 4.0 in manufacturing
- Home
- Resources
- Cooling Unit Manufacturing Insights
- The challenges and opportunities of implementing Industry 4.0 in manufacturing
The Future of Manufacturing: Embracing Industry 4.0
Manufacturing has come a long way since the Industrial Revolution. From the introduction of steam power to the automation of assembly lines, each phase of technological advancement has brought forth new challenges and opportunities. Today, we stand on the cusp of a new era in manufacturing - Industry 4.0. This fourth industrial revolution is characterized by the integration of digital technologies into every aspect of the manufacturing process, from design to production to distribution. While this presents its own set of challenges, it also offers unprecedented opportunities for supply chain optimization, manufacturing efficiency, and sustainable practices.
The Challenges of Implementing Industry 4.0
As with any major shift in technology, the implementation of Industry 4.0 in manufacturing is not without its challenges. One of the key hurdles is the need to upgrade existing infrastructure and equipment to be compatible with digital technologies. Many manufacturers still rely on legacy systems that were not designed with connectivity in mind, making it difficult to seamlessly integrate new technologies. Additionally, there is a shortage of skilled workers who possess the necessary expertise to operate and maintain these advanced systems.
Another challenge is the potential for increased cybersecurity risks. With the digitization of manufacturing processes, there is an increased risk of cyberattacks that could compromise sensitive data or disrupt production. Manufacturers must invest in robust cybersecurity measures to protect their operations and ensure the integrity of their supply chains.
Furthermore, the transition to Industry 4.0 requires a significant investment in capital and resources. Small and medium-sized enterprises (SMEs) may struggle to afford the upfront costs associated with upgrading their systems and training their workforce. This creates a digital divide between larger corporations that have the financial means to adopt new technologies and smaller businesses that may be left behind.
Despite these challenges, the potential benefits of implementing Industry 4.0 in manufacturing are too great to ignore. By embracing digital technologies and automation, manufacturers can streamline their operations, improve productivity, and reduce costs. The key lies in finding the right solutions and strategies to overcome the obstacles and maximize the opportunities offered by Industry 4.0.
Opportunities for Supply Chain Optimization
One of the most significant opportunities presented by Industry 4.0 is the ability to optimize supply chain management. With the integration of digital technologies, manufacturers can gain real-time visibility into their supply chains, enabling them to make data-driven decisions and respond quickly to changes in demand. This level of transparency and agility allows for better coordination between suppliers, manufacturers, and distributors, leading to improved efficiency and reduced costs.
Furthermore, the use of advanced analytics and predictive modeling can help identify potential bottlenecks and inefficiencies in the supply chain. By analyzing large volumes of data, manufacturers can uncover patterns and trends that may not be apparent through traditional methods. This knowledge can then be used to optimize inventory levels, minimize lead times, and ensure the timely delivery of products to customers.
Another aspect of supply chain optimization in Industry 4.0 is the integration of production and distribution processes. With the help of connected systems and smart devices, manufacturers can achieve a high level of coordination between production lines and distribution networks. This enables just-in-time manufacturing, reducing the need for excess inventory and minimizing the risk of obsolescence.
Improving Manufacturing Efficiency through Automation
Automation is a key component of Industry 4.0 and offers significant opportunities for improving manufacturing efficiency. By employing robots and autonomous systems, manufacturers can eliminate repetitive and labor-intensive tasks, freeing up human workers to focus on more complex and value-added activities. This not only improves productivity but also enhances the overall quality of products.
Moreover, automation enables manufacturers to achieve a higher degree of precision and consistency in their production processes. With the use of advanced sensors and machine learning algorithms, machines can detect and correct errors in real-time, reducing the occurrence of defects and waste. This leads to higher product quality and customer satisfaction.
Another area where automation can drive efficiency is in the maintenance of manufacturing equipment. By leveraging the power of artificial intelligence and predictive analytics, manufacturers can detect potential equipment failures before they occur, allowing for proactive maintenance and minimizing downtime. This predictive maintenance approach not only reduces costs but also extends the lifespan of machinery.
Sustainable Practices and Environmental Considerations
Industry 4.0 also presents opportunities for manufacturers to adopt sustainable practices and reduce their environmental footprint. One such area is in cooling technology, where the use of energy-efficient and environmentally friendly cooling units can significantly reduce energy consumption and greenhouse gas emissions.
Cooling system manufacturers are developing custom cooling solutions that are specifically designed for industrial applications. These precision cooling systems not only provide optimal cooling performance but also minimize energy usage. By utilizing advanced technologies such as variable speed compressors and intelligent controls, these units can adapt to the specific cooling requirements of different manufacturing processes, further optimizing energy efficiency.
Furthermore, the integration of green cooling technology in Industry 4.0 enables manufacturers to actively contribute to sustainability goals. By utilizing renewable energy sources, such as solar or wind power, to generate the electricity needed for cooling, manufacturers can reduce their reliance on fossil fuels and make significant progress towards a carbon-neutral operation.
Another aspect of sustainable manufacturing in Industry 4.0 is the concept of circular economy. By implementing closed-loop systems and recycling initiatives, manufacturers can minimize waste and maximize the reuse of materials. This not only reduces the environmental impact but also creates new business opportunities and revenue streams.
Conclusion
As manufacturing enters the era of Industry 4.0, there are both challenges and opportunities to be faced. The successful implementation of digital technologies and automation requires careful planning, investment, and collaboration. However, the benefits are immense - from improved supply chain optimization and manufacturing efficiency to sustainable practices and environmental considerations. By embracing the potential of Industry 4.0, manufacturers can position themselves at the forefront of innovation and secure a competitive advantage in an increasingly interconnected and digital world.
Related Blogs
The importance of education and awareness in promoting the adoption of green cooling technology
Read More