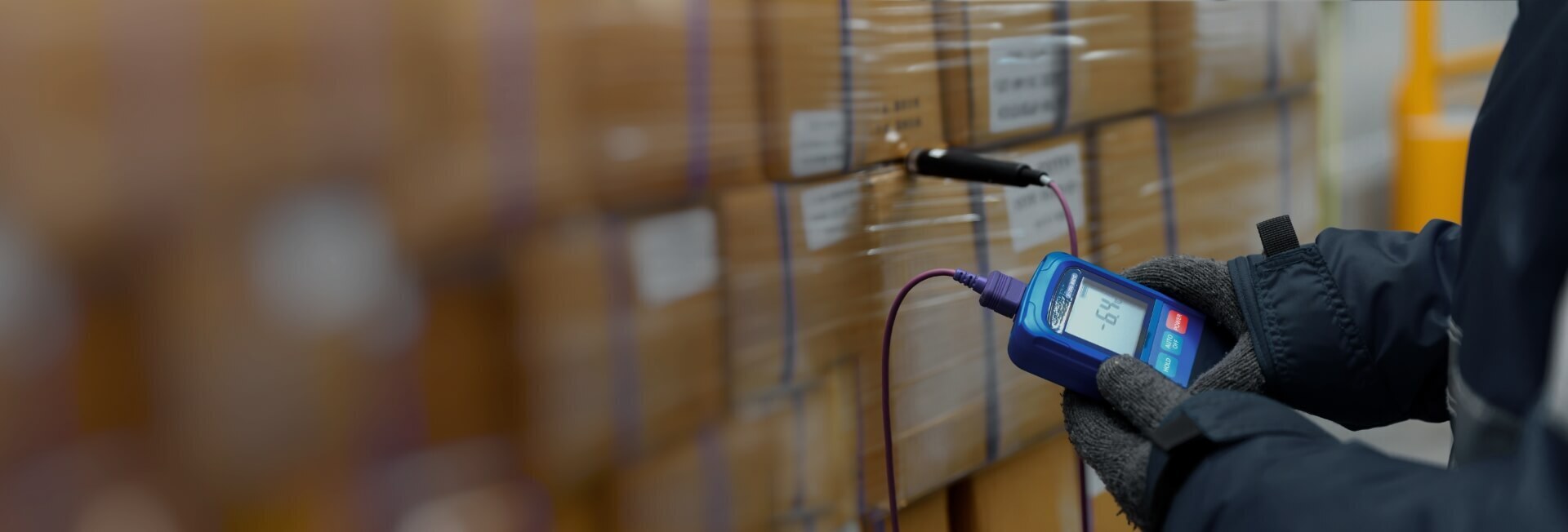
The benefits of preventive maintenance programs for industrial cooling units
- Home
- Resources
- Cooling Unit Manufacturing Insights
- The benefits of preventive maintenance programs for industrial cooling units
The Importance of Preventive Maintenance Programs for Industrial Cooling Units
Industrial cooling units play a crucial role in many manufacturing and production processes. These cooling systems are responsible for maintaining optimal temperatures in various equipment and machinery, ensuring that they operate efficiently and effectively. However, like any other machinery, industrial cooling units are prone to wear and tear, which can lead to breakdowns and costly repairs if not properly maintained. This is where preventive maintenance programs come into play.
What is Preventive Maintenance?
Preventive maintenance refers to the regular and systematic inspection, cleaning, and servicing of equipment to prevent potential issues and ensure optimal performance. It involves proactive measures taken to avoid breakdowns, reduce downtime, and extend the lifespan of industrial cooling units. By implementing a preventive maintenance program, manufacturing facilities can minimize disruptions to their production and distribution processes and optimize manufacturing efficiency.
The Benefits of Preventive Maintenance Programs
There are numerous benefits to implementing a preventive maintenance program for industrial cooling units:
1. Increased Equipment Reliability
Regular maintenance and servicing of cooling units help identify and address potential issues before they escalate into major problems. By detecting and resolving minor faults early on, preventive maintenance programs significantly reduce the risk of unexpected breakdowns and equipment failure. This increases the overall reliability of the cooling units, ensuring uninterrupted operation and minimizing production disruptions.
2. Improved Energy Efficiency
Industrial cooling units can consume a significant amount of energy, especially if they are not operating at peak efficiency. Preventive maintenance programs include measures to optimize the energy efficiency of cooling systems, such as cleaning or replacing filters, checking refrigerant levels, and inspecting motors and compressors. By ensuring that cooling units are running optimally, facilities can reduce energy consumption and lower their carbon footprint.
3. Cost Savings
Preventive maintenance programs can help manufacturing facilities save money in the long run. By identifying and addressing potential issues early on, facilities can avoid expensive repairs and replacements. Additionally, regular maintenance and servicing can help extend the lifespan of cooling units, reducing the need for frequent equipment upgrades. Furthermore, by optimizing energy efficiency, facilities can lower their utility bills and operating costs.
4. Enhanced Safety
Industrial cooling units involve complex machinery and processes that can pose safety risks if not properly maintained. Regular inspections and servicing as part of a preventive maintenance program help identify and address potential safety hazards, such as faulty wiring, leaks, or improper ventilation. By ensuring the safety of cooling units, manufacturing facilities can create a safe working environment for their employees and minimize the risk of accidents or injuries.
Implementing a Preventive Maintenance Program
To reap the benefits of preventive maintenance for industrial cooling units, manufacturing facilities should consider the following steps:
1. Conduct an Initial Assessment
Start by conducting a comprehensive assessment of the existing cooling units and their maintenance history. Identify any potential issues or areas that require immediate attention. This will serve as the foundation for developing a customized preventive maintenance program.
2. Develop a Maintenance Schedule
Create a maintenance schedule that outlines the frequency and type of maintenance tasks to be performed on each cooling unit. This schedule should consider the manufacturer's recommendations, industry best practices, and the specific requirements of the facility. It should also include regular inspections, cleaning, lubrication, and any necessary repairs or replacements.
3. Assign Responsibility
Assign responsibility for the implementation and management of the preventive maintenance program. This may involve designating a dedicated maintenance team or outsourcing the maintenance tasks to a specialized service provider. Ensure that the responsible individuals or teams have the necessary training and expertise to carry out the required tasks effectively.
4. Document and Track Maintenance Activities
Maintain detailed records of all maintenance activities, including inspections, repairs, and replacements. This documentation will serve as a reference for future maintenance tasks and help track the performance and reliability of the cooling units over time. It will also aid in identifying any recurring issues and implementing corrective measures.
5. Regularly Review and Update the Program
Regularly review the preventive maintenance program to assess its effectiveness and identify areas for improvement. Consider feedback from maintenance personnel, monitor the performance of the cooling units, and stay updated on advancements in cooling technology and best practices. Make necessary adjustments to the program to ensure it remains relevant and effective.
Conclusion
Implementing a preventive maintenance program for industrial cooling units is vital for optimizing manufacturing efficiency, reducing energy consumption, and ensuring the longevity and reliability of the equipment. By investing in regular maintenance and servicing, manufacturing facilities can minimize downtime, lower repair costs, improve safety, and contribute to a more sustainable and environmentally friendly manufacturing process. Preventive maintenance is a proactive approach that pays off in the long run, benefiting both the facility and the overall supply chain optimization.
Related Blogs
The importance of education and awareness in promoting the adoption of green cooling technology
Read More