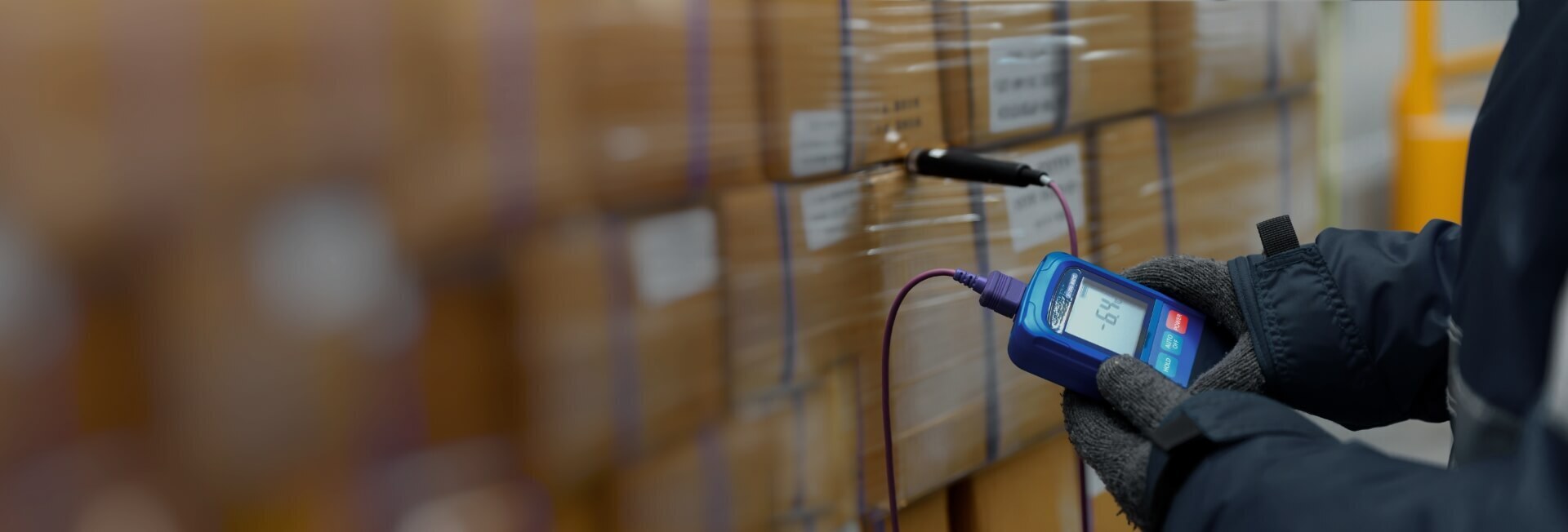
The benefits of implementing total productive maintenance in manufacturing
- Home
- Resources
- Cooling Unit Manufacturing Insights
- The benefits of implementing total productive maintenance in manufacturing
Introduction
Manufacturing efficiency is a critical aspect of any successful business. It determines the productivity, profitability, and competitiveness of a company. One way to optimize manufacturing efficiency is by implementing total productive maintenance (TPM) practices. TPM focuses on maximizing the effectiveness of equipment, processes, and people to eliminate losses and improve overall productivity. In this article, we will explore the benefits of implementing TPM in manufacturing and how it can lead to significant improvements in various areas of operations.
Improved Equipment Reliability
One of the primary goals of TPM is to improve equipment reliability. By implementing TPM practices, manufacturing companies can reduce equipment breakdowns and unplanned downtime. This is achieved through regular maintenance, proactive inspections, and early detection of potential issues. By addressing problems before they escalate, companies can avoid costly repairs and production delays. With improved equipment reliability, manufacturers can ensure a smooth production flow and meet customer demands more efficiently.
Reduced Maintenance Costs
Implementing TPM can also lead to significant cost savings in maintenance. By focusing on preventive and predictive maintenance, companies can reduce the need for emergency repairs and costly replacements. TPM emphasizes early detection of equipment issues, allowing maintenance teams to address them before they become major problems. This proactive approach not only minimizes downtime but also extends the lifespan of equipment, resulting in reduced maintenance costs in the long run. Additionally, TPM practices ensure that maintenance activities are carried out efficiently, optimizing the use of resources and minimizing waste.
Increased Overall Equipment Effectiveness (OEE)
Total productive maintenance aims to improve overall equipment effectiveness (OEE) by minimizing losses in availability, performance, and quality. Availability loss refers to the time when equipment is not available for production due to breakdowns or maintenance. Performance loss occurs when equipment operates below its maximum capacity or experiences frequent stoppages. Quality loss refers to defects or rework that result in production delays and waste. By addressing these three types of losses, TPM helps maximize equipment utilization, improve production output, and enhance product quality.
Enhanced Employee Involvement and Empowerment
TPM promotes a culture of employee involvement and empowerment. It encourages operators and maintenance personnel to take ownership of equipment and processes. Employees are trained to perform routine maintenance tasks, conduct inspections, and identify potential issues. This not only increases their technical skills but also fosters a sense of responsibility and accountability. With empowered employees, companies can leverage their knowledge and expertise to drive continuous improvement and innovation. By involving employees in the maintenance process, TPM creates a sense of ownership and pride, leading to higher job satisfaction and motivation.
Streamlined Manufacturing Processes
Another significant benefit of implementing TPM is the streamlining of manufacturing processes. TPM focuses on eliminating waste, reducing variability, and optimizing production flow. By standardizing work procedures, implementing visual management systems, and conducting continuous improvement activities, companies can achieve a more efficient and predictable production process. This leads to reduced lead times, improved on-time delivery, and better overall customer satisfaction. Streamlined manufacturing processes also enable companies to respond quickly to changing market demands and stay ahead of the competition.
Improved Product Quality
TPM plays a crucial role in improving product quality. By addressing equipment issues, conducting routine inspections, and implementing preventive maintenance, companies can minimize defects and rework. This leads to higher product quality and reduces the risk of customer complaints or recalls. TPM also emphasizes the importance of operator training and skill development, ensuring that employees have the necessary knowledge and expertise to produce high-quality products. By focusing on quality, companies can enhance their reputation, build customer trust, and gain a competitive edge in the market.
Enhanced Safety and Employee Well-being
TPM prioritizes safety and employee well-being in the manufacturing environment. Through regular equipment checks, maintenance activities, and hazard identification, TPM helps create a safer workplace. By addressing potential safety risks and implementing preventive measures, companies can reduce the occurrence of accidents and injuries. TPM also emphasizes the importance of operator training and skill development, ensuring that employees have the necessary knowledge and expertise to operate equipment safely. By promoting a safe and healthy work environment, companies can improve employee morale, reduce absenteeism, and enhance overall productivity.
Conclusion
Total productive maintenance (TPM) offers numerous benefits for manufacturing companies. By improving equipment reliability, reducing maintenance costs, increasing overall equipment effectiveness (OEE), enhancing employee involvement and empowerment, streamlining manufacturing processes, improving product quality, and enhancing safety and employee well-being, TPM can lead to significant improvements in various areas of operations. As manufacturing becomes increasingly competitive, implementing TPM is essential for companies to stay ahead and achieve sustainable success.
Related Blogs
The importance of education and awareness in promoting the adoption of green cooling technology
Read More