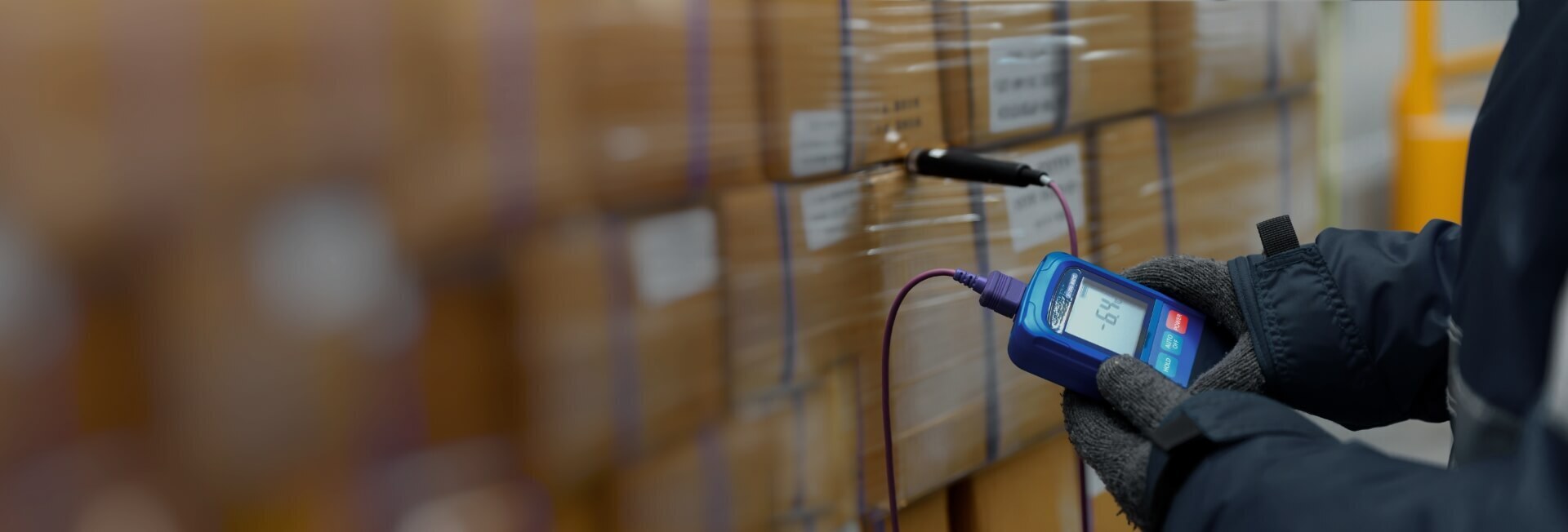
The benefits of implementing total productive maintenance in achieving streamlined operations
- Home
- Resources
- Cooling Unit Manufacturing Insights
- The benefits of implementing total productive maintenance in achieving streamlined operations
The Power of Total Productive Maintenance for Streamlined Operations
Implementing total productive maintenance (TPM) in a manufacturing environment can lead to significant improvements in efficiency, productivity, and overall operational performance. By focusing on the maintenance of equipment and the development of a proactive maintenance strategy, TPM helps organizations optimize their processes and achieve streamlined operations. In this article, we will explore the benefits of implementing TPM and how it can positively impact manufacturing operations.
Improved Equipment Reliability
One of the key benefits of implementing TPM is improved equipment reliability. By conducting regular maintenance activities and addressing any issues promptly, organizations can reduce the occurrence of unexpected breakdowns and equipment failures. This leads to increased uptime and productivity, as well as a reduction in costly downtime and repairs. With TPM, organizations can establish a culture of proactive maintenance, ensuring that equipment is always in optimal condition and ready for production.
Reduced Production Losses
Production losses can have a significant impact on a manufacturing operation's bottom line. Common causes of production losses include equipment breakdowns, changeovers, and setup time. TPM focuses on minimizing these losses by implementing preventive maintenance practices, improving equipment changeover processes, and reducing setup time. By addressing these areas, organizations can significantly reduce production losses and improve overall efficiency.
Enhanced Overall Equipment Efficiency (OEE)
Total Productive Maintenance is closely associated with Overall Equipment Efficiency (OEE), a metric used to measure the effectiveness of equipment utilization. OEE takes into account three key factors: availability, performance, and quality. By implementing TPM practices, organizations can improve all three factors, resulting in a higher OEE score. This, in turn, translates to increased production output, reduced waste, and improved profitability.
Improved Product Quality
Product quality is a critical aspect of any manufacturing operation. By implementing TPM, organizations can minimize defects and enhance product quality. TPM practices often include regular inspections, preventive maintenance, and employee training to ensure that equipment is functioning optimally and producing high-quality products. By maintaining equipment in top condition, organizations can reduce the occurrence of defects and consistently deliver products that meet or exceed customer expectations.
Reduced Costs
Implementing TPM can lead to significant cost savings for manufacturing organizations. By reducing equipment breakdowns and unplanned downtime, organizations can avoid costly repairs and production losses. Additionally, TPM helps optimize maintenance activities, ensuring that resources are utilized effectively. This can lead to reduced maintenance costs and improved overall cost efficiency.
Increased Employee Engagement and Ownership
TPM emphasizes the involvement of all employees in the maintenance and improvement of equipment and processes. By empowering employees and providing them with the necessary training and tools, organizations can foster a culture of ownership and engagement. This not only improves morale but also encourages employees to take responsibility for the equipment they operate and the processes they are involved in. Increased employee engagement can result in improved productivity, higher quality output, and a safer working environment.
Conclusion
Implementing total productive maintenance can bring a multitude of benefits to manufacturing organizations. From improved equipment reliability and reduced production losses to enhanced overall equipment efficiency and increased employee engagement, TPM plays a crucial role in achieving streamlined operations. By prioritizing maintenance and adopting proactive strategies, organizations can optimize their processes, reduce costs, improve product quality, and ultimately, achieve sustainable success in today's competitive manufacturing landscape.
Related Blogs
The importance of education and awareness in promoting the adoption of green cooling technology
Read More