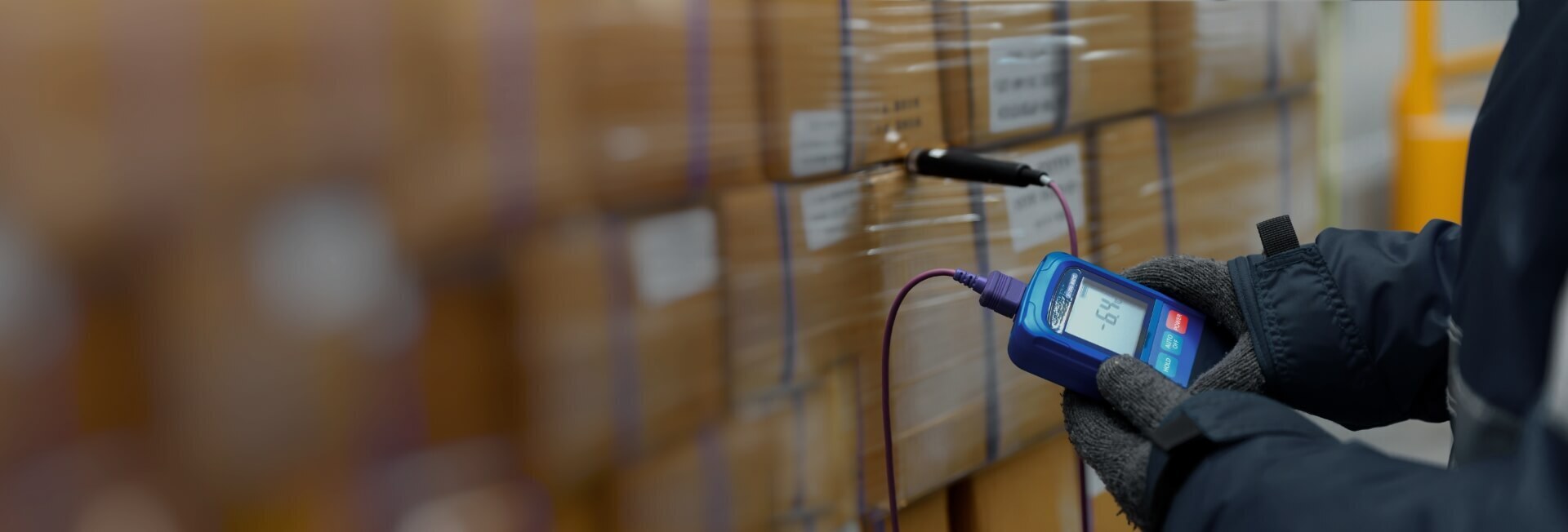
The benefits of implementing single-piece flow in achieving streamlined manufacturing
- Home
- Resources
- Cooling Unit Manufacturing Insights
- The benefits of implementing single-piece flow in achieving streamlined manufacturing
The Benefits of Implementing Single-Piece Flow in Achieving Streamlined Manufacturing
Streamlined manufacturing is a key objective for many companies looking to improve their production processes. By implementing efficient and effective manufacturing practices, businesses can optimize their supply chain, increase manufacturing efficiency, and reduce waste. One such practice that can significantly contribute to achieving streamlined manufacturing is the implementation of single-piece flow.
What is Single-Piece Flow?
Single-piece flow, also known as one-piece flow or continuous flow, is a manufacturing method that focuses on producing one unit of a product at a time, rather than in batches. In this approach, each unit moves through the production process at a steady pace, with minimal waiting time between each step. The goal is to eliminate bottlenecks, reduce lead times, and ensure a smooth and consistent flow of production.
The Benefits of Single-Piece Flow
Implementing single-piece flow in manufacturing can offer several benefits for businesses:
1. Increased Efficiency
Single-piece flow allows for a more efficient production process. By producing one unit at a time, companies can identify and address any issues or defects immediately, rather than waiting for an entire batch to be completed. This reduces the chances of producing defective or non-conforming products, which can lead to costly rework or recalls. Additionally, the continuous flow of production eliminates the need for large inventory levels, saving space and reducing carrying costs.
2. Reduced Waste
Single-piece flow helps to minimize waste in the manufacturing process. With a focus on producing one unit at a time, companies can identify and eliminate any non-value-added activities or processes. By streamlining the production process and reducing unnecessary steps, businesses can reduce the amount of time, energy, and resources required to produce each unit. This leads to significant cost savings and a more sustainable manufacturing operation.
3. Improved Quality Control
With single-piece flow, quality control becomes an integral part of the production process. By inspecting each unit as it moves through the production line, companies can quickly identify and address any quality issues. This ensures that only products that meet the required specifications are passed on to the next stage, reducing the risk of defects or customer dissatisfaction. Additionally, by catching and addressing quality issues early on, companies can prevent the production of defective batches, saving time and resources.
4. Faster Response Times
Single-piece flow enables companies to respond more quickly to changes in customer demand or market conditions. With a continuous flow of production, businesses can easily adjust their production rates or switch between different products without disrupting the entire process. This agility allows companies to meet customer demands more efficiently and reduce lead times, ultimately increasing customer satisfaction.
Implementing Single-Piece Flow
Implementing single-piece flow in manufacturing requires careful planning and consideration. Here are some steps to help businesses successfully adopt this approach:
1. Value Stream Mapping
Before implementing single-piece flow, it is essential to understand the current state of the production process. Value stream mapping can help identify areas of waste, bottlenecks, and opportunities for improvement. By analyzing the entire production process, companies can determine the most efficient and effective way to implement single-piece flow.
2. Standardized Work
Standardized work is crucial for the successful implementation of single-piece flow. By establishing clear and consistent work instructions, companies can ensure that each worker understands their role and responsibilities. This includes defining the sequence of tasks, the time required for each task, and the quality standards to be met. Standardized work helps to minimize variations in the production process and ensures a smooth flow of production.
3. Layout Optimization
The layout of the production facility plays a significant role in achieving efficient single-piece flow. The layout should be designed to minimize the distance and time required to move products from one process to another. This can be achieved by organizing workstations in a logical sequence, eliminating unnecessary movement and transportation, and ensuring a smooth flow of materials and information.
4. Continuous Improvement
Implementing single-piece flow is an ongoing process that requires continuous improvement. By regularly evaluating and analyzing the production process, companies can identify areas for further optimization. This includes identifying and addressing any bottlenecks, streamlining processes, and implementing new technologies or tools to enhance efficiency. Continuous improvement ensures that the benefits of single-piece flow are sustained in the long term.
Conclusion
Implementing single-piece flow in manufacturing can have a significant impact on achieving streamlined manufacturing. By focusing on producing one unit at a time, companies can increase efficiency, reduce waste, improve quality control, and respond more quickly to customer demands. However, it is important to note that implementing single-piece flow requires careful planning, standardized work, layout optimization, and a commitment to continuous improvement. By embracing this approach, businesses can achieve a more efficient, sustainable, and customer-centric manufacturing operation.
Related Blogs
The importance of education and awareness in promoting the adoption of green cooling technology
Read More